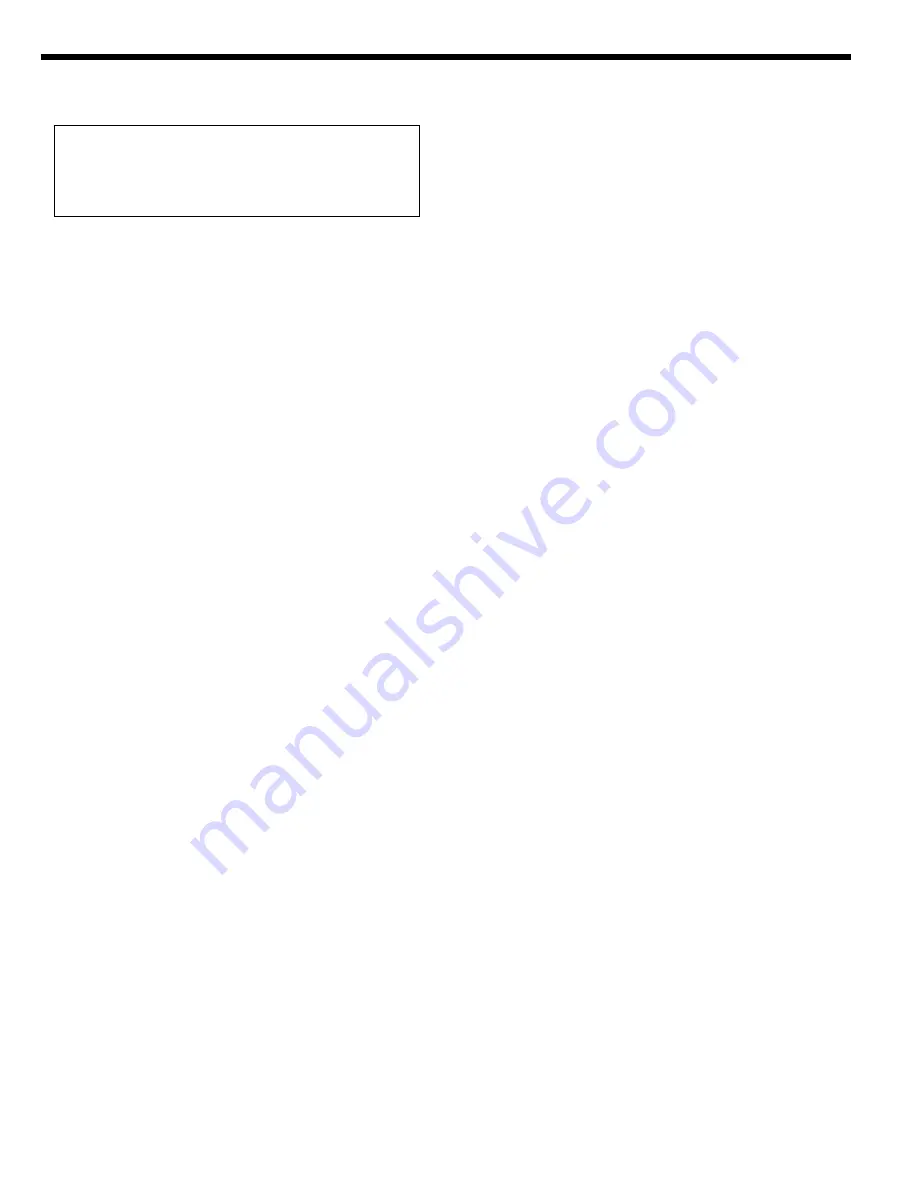
4
REMOVAL OF ACTUATOR FROM VALVE BODY
ASSEMBLY
Close inlet and outlet stop valves. Be sure valve body is not
under pressure. Remove all accessories from control valve.
Refer to Figure 2.
Reverse Acting Pneumatic Actuator
Loosen stem nuts (24) and move to approximately 1/3 down
valve stem. Re-tighten being careful not to move valve stem.
Energize actuator with air to lift the plug off the seat. Disengage
lock nut (26) from bonnet (25). De-energize actuator. The
actuator and yoke should move away from bonnet. Lift actuator
and yoke assembly along with plug (39) off the seat. With an
adjustable wrench, unthread valve stem from actuator stem (Fig.
6, #16) until valve stem is disengaged from actuator stem .
Remove stem nuts, indicator, packing nut and lock nut.
Direct Acting Pneumatic Actuator
Energize actuator with air slightly (in case of back seating).
Loosen stem nuts (24) and re-tighten approximately 1/8” away
from actuator stem (Fig. 6, #16). Disengage lock nut (26) from
bonnet (25). With an adjustable wrench, unscrew valve stem
from actuator stem. When valve stem reaches seat, lift actuator
(to prevent galling seat and plug). Remove stem nuts, indicator
and lock nut.
DISASSEMBLY OF VALVE BODY
Remove stem nuts (24), indicator (32) and lock nut (26). Lift yoke
off bonnet (25). To complete body disassembly, unscrew bonnet
for K1 and cap (42) for K4. For K4 remove bonnet nuts (34) and
lift off blind flange (35), bonnet, stem and plug assembly (37).
Remove gasket (36). A new gasket should be installed each time
valve body is disassembled. Turn stem and plug assembly out
of bonnet through packing. Replace packing if necessary. All
parts should be inspected for wear and cleaned thoroughly
before re-assembling valve body.
DISASSEMBLY OF ACTUATOR
Remove actuator from valve. Remove regular casing bolts (4)
and casing nuts (5). Gradually loosen nuts on remaining long
casing bolts (14) to allow pre-compression of actuator springs.
Remove upper casing (2). Pull actuator stem (16), along with
diaphragm (15), springs (3) and piston (13), out through bushing
(7). Place a wrench on the machined flats of actuator stem, and
remove stem nut (10) or travel stop (22), seal washer (12) and
stem washer (11). Remove o-ring (8) from bushing and replace if
necessary. Lubricate o-ring after installing.
RE-ASSEMBLY OF ACTUATOR
Refer to Figure 6 for correct orientation of casings, diaphragm
(15), piston (13), stem (16) and springs (3) for direct or reverse
action. Be sure piston spring recesses line up between casing
ribs as shown in Figure 8C. Lubricate bushing O-ring (8) and
insert actuator stem through bushing. Re-attach upper casing
(2) with long bolts (14) & nuts (5), tightening alternately. Install
remaining casing nuts and bolts. Apply air to diaphragm case
and check for leakage, full travel and dead band less than .2 psi.
LAPPING PLUG INTO SEAT
Seats and plugs should never require more than the lightest
touch up with very fine (400 grit) grinding compound. Heavy
lapping will produce galling, a wider seating surface and a
groove in the plug, all of which tend to cause leakage. Reface a
damaged surface before attempting to grind it in. Lap sparingly.
Replace stem and plug (39) in bonnet (25) through packing.
Apply lapping compound to plug. Place bonnet and bonnet
flange (35 for K4 only) on body. After lapping, disassemble and
clean all parts thoroughly.
PACKING REPLACEMENT
Check stem for gouges if packing leaks. Replacement packing
cartridges can be installed.
RE-ASSEMBLY OF VALVE BODY (K1)
Tighten bonnet (25) to body. Replace yoke (9), lock nut (26),
stem nuts (24) and travel indicator (32) over stem (34).
RE-ASSEMBLY OF VALVE BODY (K4)
Install a new gasket (36). Attach bonnet (26) and bonnet flange
(35) to body with bonnet studs and nuts (33, 34). Be sure to
tighten bolts alternately and evenly to ensure proper seating of
the plug. Replace yoke (9), lock nut (27), stem nuts (31) and
travel indicator (23) over stem (30).
REPLACING ACTUATOR ON VALVE BODY -
PNEUMATIC
Put actuator assembly over valve stem. Place lock nut (Fig. 2,
#26), and stem nuts (24) with travel indicator (32) on valve stem.
Rest actuator stem (16) on valve stem. Tighten stem nuts approx-
imately 2/3 down valve stem. Lift actuator assembly and engage
valve stem with actuator stem (be careful not to gall plug & seat).
Reverse Acting
When sufficient engagement is met, the actuator can be
energized with air to place the yoke on the bonnet (25) and lift
the plug off the seat. Tighten lock nut and packing nut.
Direct Acting
Engage valve stem with actuator stem so no contact is made
between plug and seat when bottom of yoke is rested on
bonnet. Tighten lock nut.
ACTUATOR ADJUSTMENT - PNEUMATIC
Close inlet and outlet stop valves. Be sure valve body is not
under pressure. Place a wrench on the machined flats of
Warning: Injury or death can occur due to failure
to completely isolate valve from all sources of
pressure before beginning disassembly. Do not
proceed until valve has been completely isolated
from process stream and vented to atmosphere.
MAINTENANCE