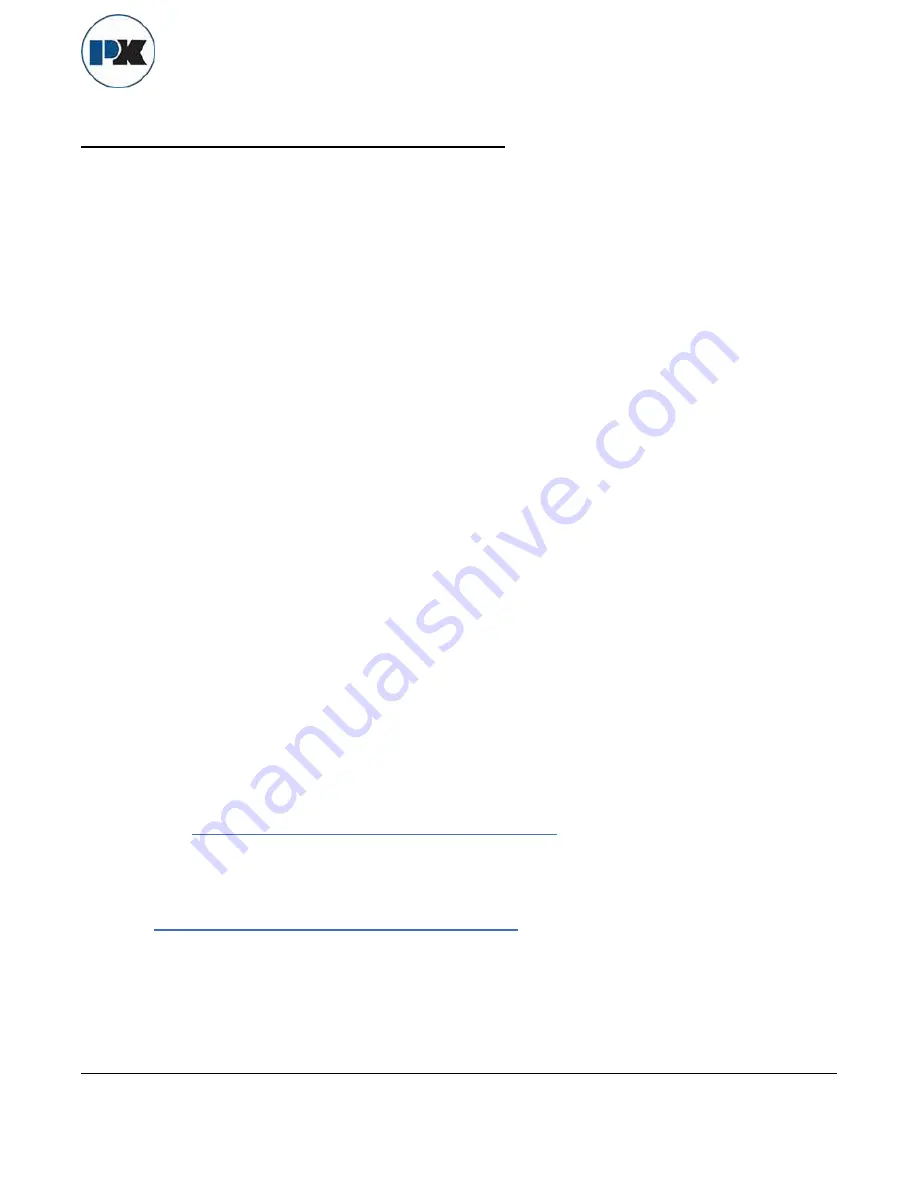
P-K MACH
®
Gas Fired Boiler
Technical Service 1.877.728.5351
Revised: January 3, 2020
Released: January 3, 2020
Patterson-Kelley 2020
All Rights Reserved.
1004905981 P-K MACH C1500H-C4000 Installation and
Owners Manual (Rev F Jan-2020).docx
Page 117
Appendix D
– Best Practices For New & Retrofit Systems
BEST PRACTICES FOR ALL BOILER INSTALLATIONS
1. Patterson-Kelley recommends and most installation codes require isolation valves on both the
boiler’s inlet (return) and outlet (supply) pipe runs. These are used to hydraulically isolate the
boiler from the hydronic system, which should be standard practice when flushing or adding
concentrated cleaning chemicals.
2. Patterson-
Kelley recommends installing purge valves on the system side of the boiler’s isolation
valves. These valves should be used to purge the hydronic system of debris and sediment prior
to the initial startup of the boiler equipment. Since the purge valves are located on the system
side of the boiler’s isolation valves, the debris and sediment will not be routed in direct proximity
to the boiler’s heat exchanger.
3. Patterson-Kelley recommends installing a standard mesh strainer (maximum 20 mesh) on the
each boiler’s return (inlet) piping. This is intended to prevent large particles, foreign debris, etc.
from entering and obstructing flow or heat transfer through the boiler’s heat exchanger. Each
strainer should feature a manual blow-down valve in order to purge the debris from the strainer.
NOTE:
This strainer is not intended to remove fine particulate matter from the boiler system
which will be discussed later in this appendix.
4. Patterson-Kelley recommends installing a water meter on the cold water fill piping. The intention
of this device is to periodically monitor the amount of fresh water introduced into the system
piping. It can also be used to establish a rough estimate of the total system volume during the
initial fill. In general, the annual amount of fresh water make-up should be less than 10% of the
total system volume. A water meter can also be useful to detect a leak in the hydronic system if
you notice an unexpected increase in the volume of fill water.
5. Oxygen (O
2
) elimination is critical to the longevity of any hydronic system. Patterson-Kelley
recommends installing an Air Separator (micro-bubbler style) that is capable of eliminating the
dissolved Oxygen levels introduced from the cold water fill. In general, air separators are most
effective when the boiler water is at highest temperature and lowest pressure.
6. Patterson-Kelley recommends installing an Automatic Air Vent on the Air Separator. In order for
the Air Separator to continually purge the system of dissolved Oxygen, an Automatic Air Vent is
preferred over a manual air vent.
7. The maximum flow rate requirements vary between Patterson-Kelley boiler models. Please
– Installation and Quick Reference
a complete listing of the maximum
flow rates per boiler model. Exceeding the maximum flow rate of a boiler can cause erosion of
the boiler’s heat exchanger or piping materials and can damage the paddle type flow switch.
8. The minimum flow rate requirements vary between Patterson-Kelley boiler models. Please refer
to
– Installation and Quick Reference
for a complete listing of the minimum flow
rates per boiler model. Flowing below the minimum flow rates can lead to overheating of the
boiler’s heat exchanger materials and the formation of steam bubbles within the water
passages.
9. Well in advance of the equipment startup, turn off all circulation pumps and close the isolation
valves on each boiler’s inlet (return) and outlet (supply) pipe runs. Connect a hose to the purge
valves and run this hose to a nearby floor drain. Open each purge valve to flush out debris that