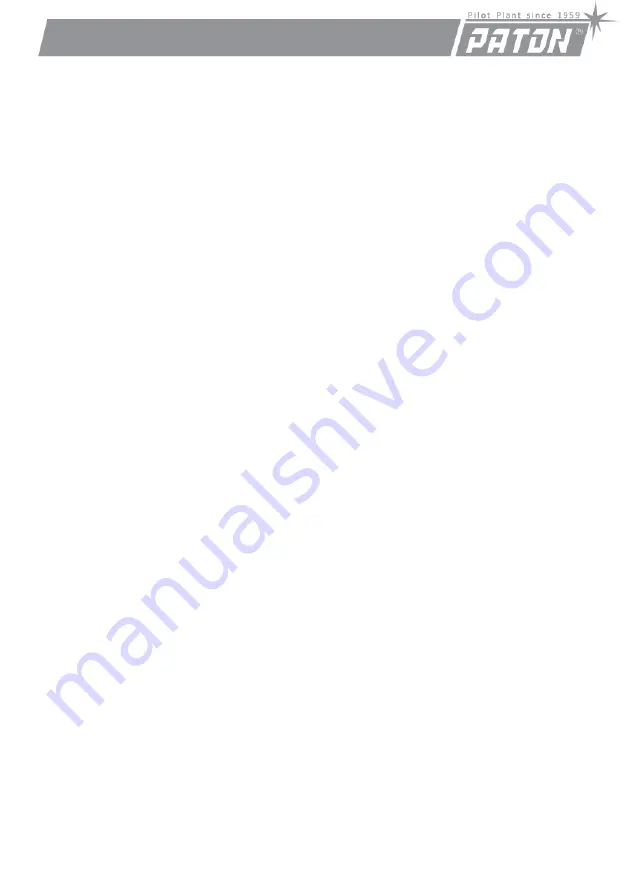
PATON
StandardMIG
MMA/TIG/MIG/MAG
-24 -
By default, the output time is set to 0.1 seconds, that is, in fact, it is turned off.
See Clause 6.1 for sequence of changing the value of any function in the current
welding mode. Use the right indicator of the wire-feeding machine.
5.5 FUNCTION OF VOLTAGE FADE‐OUT IN THE END OF WELDING
This function is intended for the smooth welding of a crater formed in the weld
pool under the action of an electromagnetic blast by an electric arc and,
subsequently, a source of defects in the weld. The signal to the beginning of the
function is the release of the torch button at the end of the welding process, while
it is necessary to stop the torch movement and brew a hole (this is the crater) in the
weld with a falling voltage. The time of voltage drop [t.dn] in the source, as well as
the time of drop of the wire-feeding speed [t.dn] of the wire-feeding machine is
responsible for the regulation of the smoothness of this process. These values must
match for correct operation. By default, both are set to 0.1 seconds, that is, in fact,
in the “OFF” state. This value can be changed at your discretion; see Clause 6.1 for
sequence of changing the value. Use the left source indicator and the right
indicator of the wire-feeding machine.
5.6 FUNCTION OF POST‐PURGING WITH SHIELDING GAS
This function consists in the subsequent purging of the welding zone with a
shielding gas after the extinction of the welding arc, since the red-hot weld pool is
afraid of the harmful effects of atmospheric air for some time. By default, the post-
purging time [t.Po] is set to 1.5 seconds; this value can be changed at any time at
your discretion. See Clause 6.1 for sequence of changing the value of any function
in the current welding mode. Use the left source indicator and the right indicator of
the wire-feeding machine.
5.7 PULSED VOLTAGE WELDING FUNCTION
This function is designed to facilitate control over the welding process in
spatial positions other than downhand position, as well as during welding of
non‐ferrous metals. This function affects directly weld metal dilution; therefore, it
primarily affects the shape of weld. It also forces drop transfer from the filler wire
into the weld pool and, consequently, affects the process stability. Just as other
types of welding, this process substitutes movements of welder’s hand to some
extent—this is especially important in hard‐to‐reach places. In addition to weld
shape, correct setting also determines the quality of the weld forming, thus
reducing risk of porosity and grain structure of the weld and consequently
increasing weld strength.
Summary of Contents for StandardMIG-160
Page 1: ......
Page 2: ...PATON StandardMIG MMA TIG MIG MAG 2 ...