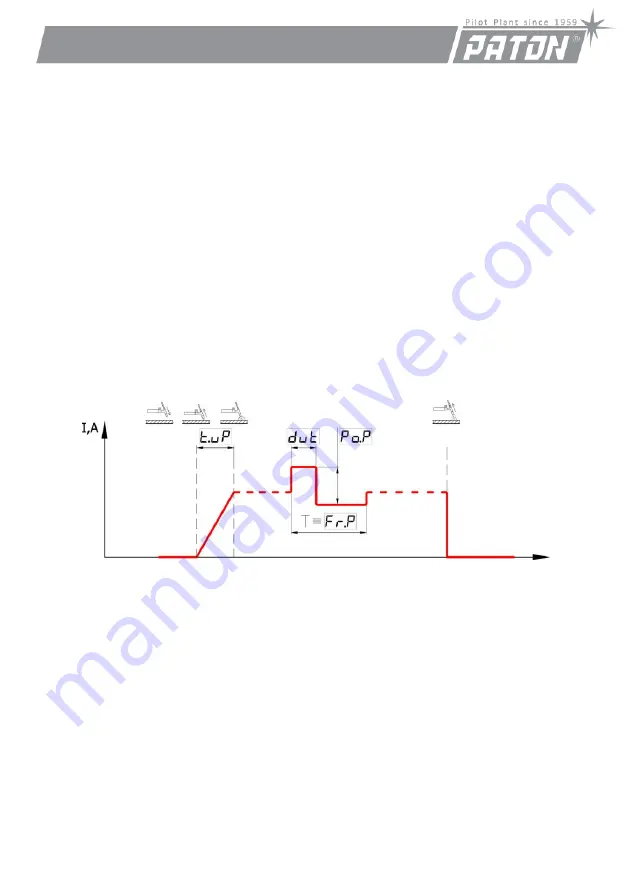
PATON
MultiPRO series
DC MMA/TIG/MIG/MAG
- 16 -
4. TUNGSTEN ARC INERT GAS WELDING (TIG)
In this welding mode, the wire-feeding machine is not needed!
Attention!
The TIG-2T welding cycle is set by default, see Clause 4.2.1.
Shielding gas is most often pure argon “Ar”, sometimes helium “He”, as well as
their mixtures with different ratios.
Example: argon + helium “40%Ar+60%Не”.
EXCLUDE usage of combustible gases! Other gases can only be used upon
approval of the equipment manufacturer.
Attention!
A common mistake is “needle‐like” electrode sharpening; in this
case, the arc may wag from side to side. A correctly sharpened electrode has
slightly blunted neg, and the smaller is the “butt” withstanding set current, the
better. Remember that a very sharp‐pointed electrode flashes off very easily at
high arc currents due to low heat emission. In addition, sharpening notches shall be
located along the electrode axis.
4.1.1 WELDING CYCLE – TIG-LIFT
See Clause 6.1 for sequence of changing the value of any function in the
current welding mode.
t, s