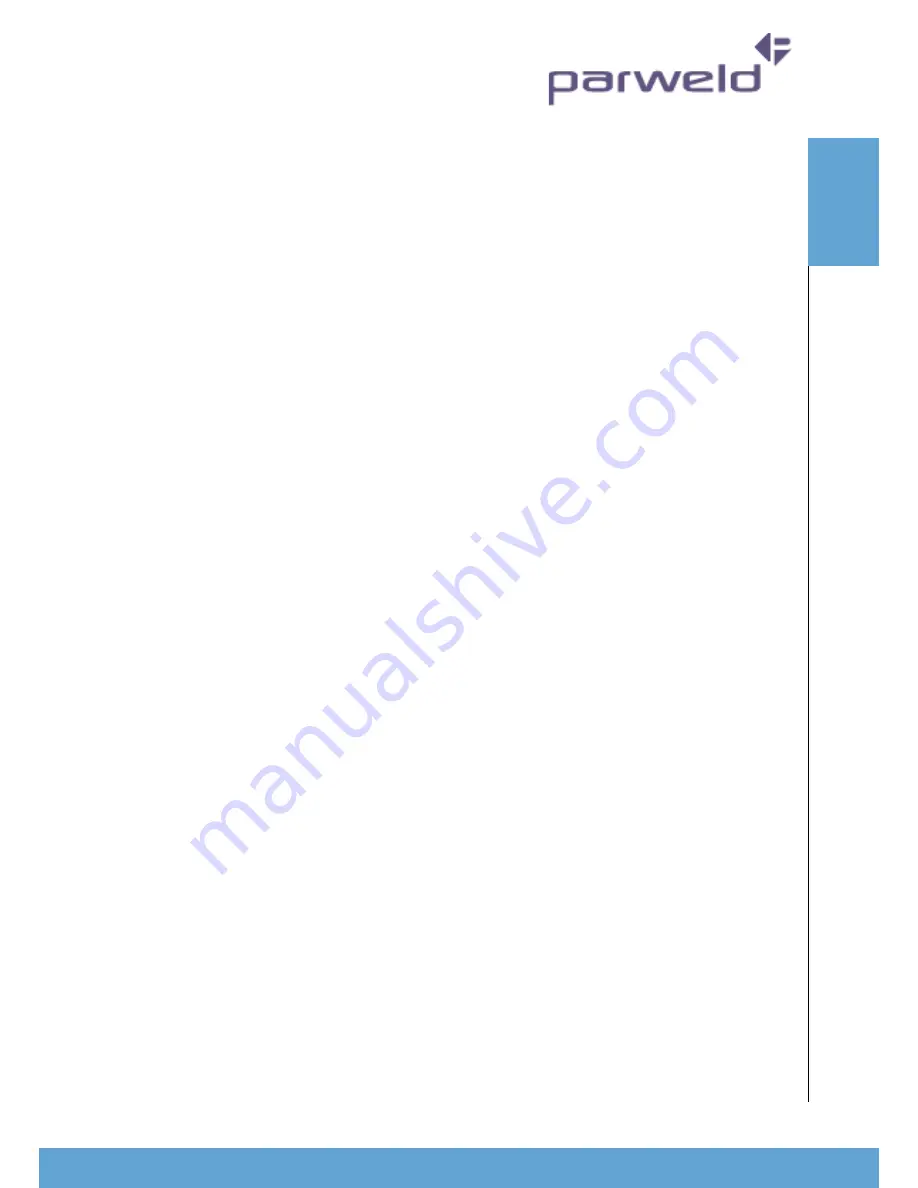
www.parweld.com
www.parweld.com
7
5.1 Unpacking the Machine
Carefully remove the machine from the packaging, we recommend
you retain the packaging until the machine has been fully installed
and tested incase it has been damaged in transit and has to be
returned to the re-seller.
5.2 location
Be sure to locate the welder according to the following guidelines:
In areas, free from moisture and dust.
Ambient temperature between 0-40
0
C.
In areas, free from oil, steam and corrosive gases.
In areas, not subjected to abnormal vibration or shock.
In areas not exposed to direct sunlight or rain.
Place at a distance of 12” (300 mm) or more from walls or similar
that could restrict natural airflow for cooling.
5.3 Input and grounding connection
WarnInG
Before starting the installation, check that your power supply
is adequate for the voltage, amperage, phase, and frequency
specified on the Machine nameplate.
Operate the welding power source from a single-phase 50/60 Hz,
AC power supply. The input voltage must match one of the electrical
input voltages shown on the input data label on the unit nameplate.
The XIT 160M machine should only be used on 230V supply. Refer
to the specifications table for voltage tolerances.
Have a qualified electrician connect the input plug. For long runs
over 30m , larger copper wires should be used. The green/yellow
wire in the input cable connects to the frame of the machine. This
ensures proper grounding of the machine when the machine plug is
inserted into the receptacle.
5.4 MIG welding torch setup
The welder, as shipped from the factory, is connected for electrode
positive (+) polarity. This is the normal polarity for MIG welding. The
polarity of the welding set cannot be changed.
5.4.1 Changing drive roll sets
1. Turn off the power source.
2. Release the pressure on the idle roll by pulling the pressure
adjuster towards the wire spool holder. The idle roll assembly
should now hinge down away from the pressure roll.
3. Unscrew the plastic knob retaining the grooved drive roll and
side off the drive roller.
4. Ensure the wire size marked on the side of the feed roller
matches the wire size to be used.
5. Replace the drive in reverse of the above procedure ensuring
the wire size to be used is marked on the outward facing side of
the roller as it is refitted.
nOte: Be sure that the torch liner and contact tip are also sized
to match the selected wire size.
5.4.2 Welding wire installation
Open the Wire Drive Compartment Door
6. Unscrew the plastic retaining wheel from the end of the spool
holder shaft.
7. Position the wire spool so that it will rotate in a direction when
feeding so as to be de-reeled from the bottom of the coil.
8.
Slide the wire spool all the way onto the shaft and refit the
plastic retaining nut.
note:- there is a friction brake on the reel hub assembly to
prevent the wire spool over running when welding stops ensure
the this is slackened to the minimum setting. It can be adjusted
by means of the nut visible when the plastic nut is removed.
9. Turn the Spool until the free end of the electrode is accessible.
While securely holding the electrode, cut off the bent end and
straighten the first 100mm. (If the electrode is not properly
straightened, it may not feed properly through the wire drive
system Manually feed the wire from the wire reel and through
the wire guide and then over the top of the wire feed roller
(ensure the pressure arm is in its raised position.)
10. Continue to feed the wire through the outlet guide until 20mm of
wire is protruding from the front of the machine torch connector.
11. Reposition the adjustable pressure arm to its original position to
apply pressure. Adjust pressure as necessary.
Note the pressure arm should be adjusted in order to give
the minimum amount of pressure on the wire to allow reliable
feeding,
5.4.3 torch installation
Your Parweld MIG/MAG Welding Torch has been supplied ready to
weld. It has been supplied with the standard consumables denoted
in the product brochure.
To connect the torch to the power source:-
1. Remove the tip adaptor and contact tip
2. Inch the wire from the exit of the wire guide on the feed unit
as Figure 1. Ensure that it does not short out on any machine
panels.
3. Carefully slide the electrode wire into the torch liner and
slowly locate the torch gun plug body into the feed unit central
connector and tighten the gun plug nut as Figure 2
Note; To aid the initial location of a new torch and to prevent
O
pera
tIO
n