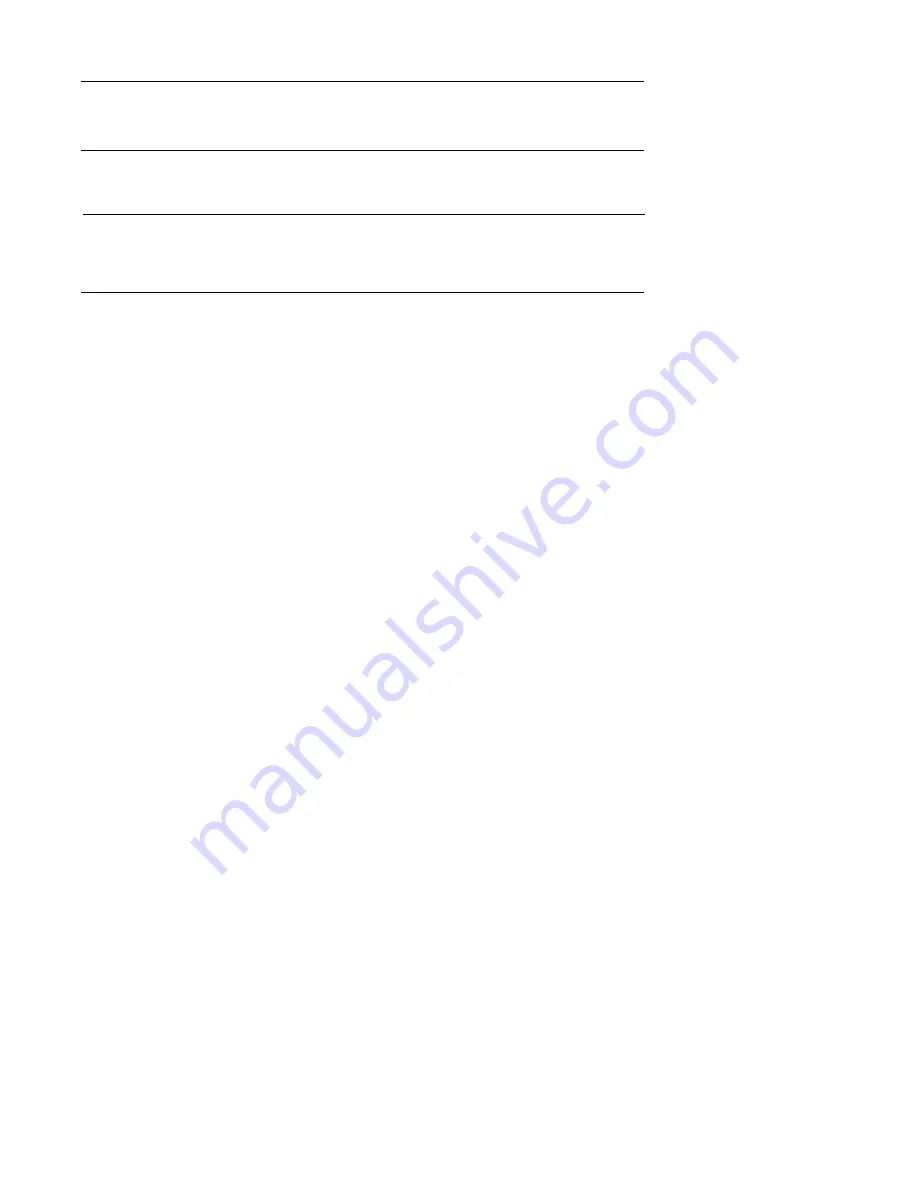
49
Momentary ER 70 -
1. May occur when incrementing or decrementing a
Controller unable to respond
value. Error clears itself.
within 250 milliseconds
Momentary ER 71 -
1. Computer program must wait longer for a response
Byte received before the
from the instrument.
response was transmitted
Momentary Er 72 -
1. Data received not valid, possible corruption on the
Incorrect Block Check
comm line. Possible noise problems. Check baud
character was received
rates, instrument addresses, line connections, and
termination.
Momentary Er 73 -
1. Check baud rate.
Byte received with incorrect
2. Possible noise problems. Check instrument
parity.
addresses, line connections, and termination.
Summary of Contents for MRC 7000
Page 27: ...27 CbS CAd1 CAd2 CCon D Com Optional Coo...
Page 61: ...61...
Page 62: ...62...
Page 63: ...63...
Page 64: ...64...