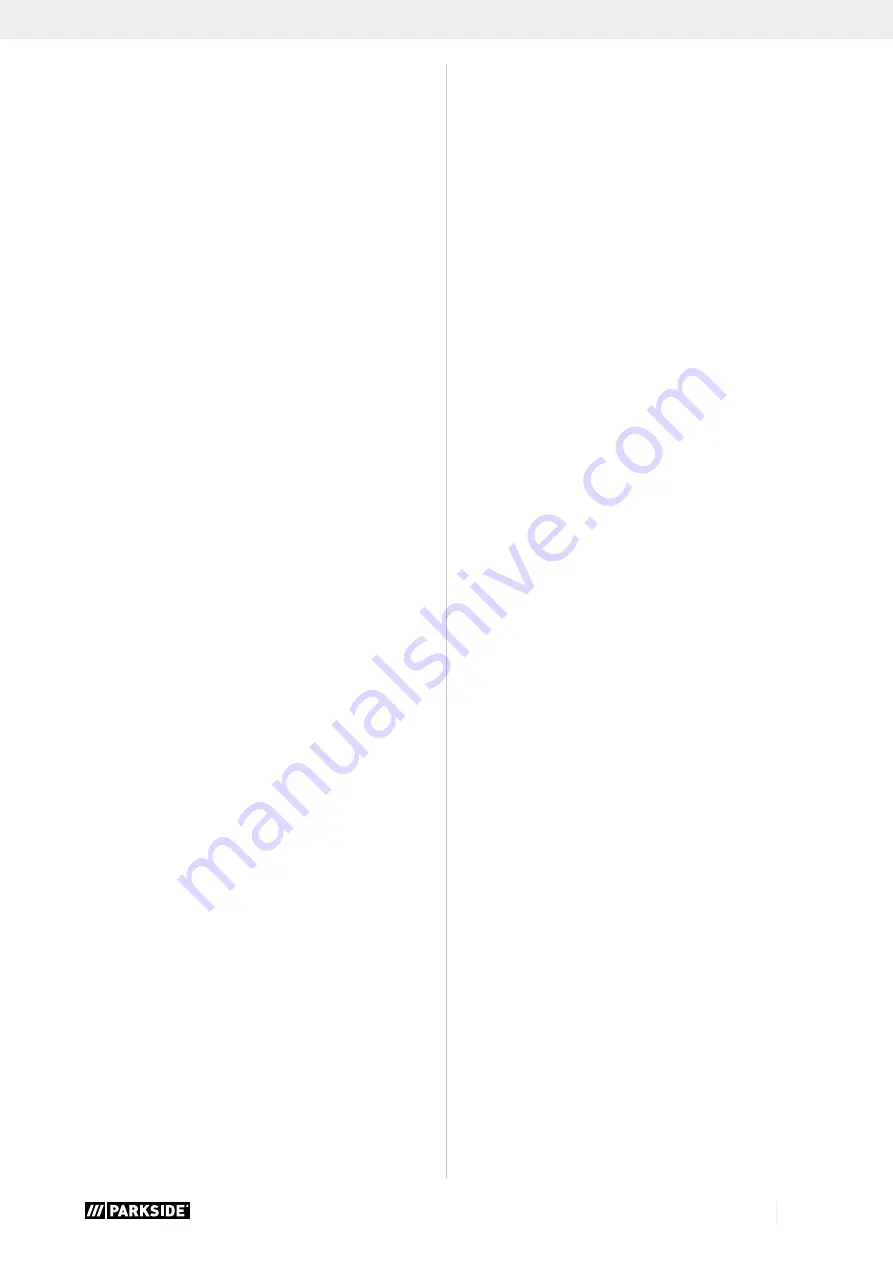
9
GB/CY
9.4 Precision adjustment of the stop for mitre cut
45° (fig. 1/2/5/9/10)
Tools required:
-
Allen key 6 mm
-
Open-ended spanner SW13 (not included in the scope of
delivery)
• No stop angle included.
• Lower the machine head (4) and secure it using the locking
bolt (23).
• Fix the rotary table (14) in the 0° position.
Attention!
For bevel cuts (inclined saw head), the moveable stop rail
(16a) must be fixed in the outer position. (
Left side
).
• Open the set screw (16b) for the moveable stop rail (16a)
and push the moveable stop rail (16a) outwards.
• The moveable stop rail (16a) must be fixed far enough in
front of the innermost position that the distance between the
stop rail (16a) and the saw blade (6) amounts to a maxi-
mum of 8 mm.
• The moveable stop rail (28) must be fixed in the inner posi-
tion. (
Right side
).
• Before making a cut, check that the stop rail (16a) and the
saw blade (6) cannot collide.
• Loosen the set screw (22) and use the handle (1) to angle
the machine head (4) 45° to the left.
• 45° - position angle stop (B) between the saw blade (6) and
rotary table (14).
• Loosen the lock nut (27a) and adjust the screw (27) until the
angle between the saw blade (6) and the rotary table (14)
is precisely 45°.
• Tighten the lock nut (27a) again.
• Subsequently check the position of the angle indicator. If
necessary, loosen the pointer (19) using a Philips screwdriv-
er, set to position 45° on the angle scale (18) and re-tighten
the retaining screw.
10. Operation
10.1 Using the laser (fig. 18)
• To switch on:
Press the ON/OFF switch laser (33) 1x. A
laser line is projected onto the material you wish to process,
providing an exact guide for the cut.
• To switch off:
Press again the ON/OFF switch laser (33).
10.2 Limiting the cutting depth (fig. 3/13)
• The cutting depth can be infinitely adjusted using the screw
(24). To do this loosen the knurled nut (24a) on the screw
(24). Turn the screw (24) in or out to set the required cutting
depth. Then re-tighten the knurled nut (24a) on the screw
(24).
• Check the setting by completing a test cut.
10.3 Serial cutting
For repeated cuts of the same length, the length stop (37) can
be opened. You can use the length stop (37) on the right and
on the left.
• Fold up the length stop (37).
• Loosen the set screw for workpiece support (9).
• Pull out the workpiece support (8).
• Set the required dimension between saw blade and length
stop (37).
• Re-tighten the set screw for workpiece support (9).
• Perform cutting as described in sections 10.4 to 10.7.
10.4 Crosscut 90° and turntable 0° (fig. 1/2/7)
In the case of cutting widths up to approx. 100 mm it is possible
to fix the traction function of the saw with the set screw (20) in
the rear position. In this position the machine can be operated
in cross cutting mode. If the cutting width is over 100 mm then
it is necessary to ensure that the set screw (20) is loose and the
machine head (4) can move.
Attention!
For 90° crosscuts, the moveable stop rail (16a) must be fixed
in the inner position.
• Open the set screw (16b) for the moveable stop rail (16a)
and push the moveable stop rail (16a) inwards.
• The moveable stop rail (16a) must be locked in a position far
enough from the inner position that the distance between the
stop rail (16a) and the saw blade (6) is no more than 8 mm..
• Before making the cut, check that the stop rail (16a) and the
saw blade (6) cannot collide.
• Re-tighten the set screw (16b).
• Move the machine head (4) to its upper position.
• Use the handle (1) to push back the machine head (4) and
fix it in this position if required (dependent on the cutting
width).
• Place the piece of wood to be cut at the stop rail (16) and
on the turntable (14).
• Lock the material with the clamping devices (7) on the fixed
saw table (15) to prevent the material from moving during
the cutting operation.
• Release the lock switch (3) and press the ON/OFF switch
(2) to start the motor.
• With the drag guide (21) fixed in place (21):
: use
the handle (1) to move the machine head (4) steadily and
with light pressure downwards until the saw blade (6) has
completely cut through the work piece.
• With the drag guide (21) not fixed in place (21):
pull the machine head (4) all the way to the front. Lower the
handle (1) to the very bottom by applying steady and light
downward pressure. Now push the machine head (4) slowly
and steadily to the very back until the saw blade (6) has
completely cut through the work piece.
• When the cutting operation is completed, move the machine
head back to its upper (home) position and release the ON/
OFF button (2).
Attention!
The machine executes an upward stroke auto-
matically due to the return spring, i.e. do not release the han-
dle (1) after completing the cut; instead allow the machine
head to move upwards slowly whilst applying light counter
pressure.
10.5
Crosscut 90° and turntable 0° - 45°
(fig. 1/7/8)
The crosscut, drag and mitre saw can be used to make cross-
cuts of 0° -45° to the left and 0° -45° to the right in relation
to the stop rail.
Summary of Contents for 3901227974
Page 66: ...61 BG 1 BG BG BG BG BG BG BG II...
Page 68: ...63 BG 4 2 x 7 2 x 8 17 6 mm C 3 mm D 5 6 m 1 2...
Page 69: ...64 BG 3 4...
Page 70: ...65 BG 5 a b 100 mm c d e f 100 mm g h i j k l m n...
Page 78: ...73 BG 15 2012 19 E 16...
Page 79: ...74 BG 17 3 112 115 IAN 331932_1907...
Page 81: ...76 BG 2 1 3 1 1 www lidl service com QR Lidl Service www lidl service com IAN 331932_1907...
Page 83: ...78 GR CY 1 GR CY GR CY GR CY GR CY GR CY GR CY GR CY II...
Page 85: ...80 GR CY 4 2 x 7 2 8 17 6 mm C 3 mm D 5 6 m 1 2...
Page 86: ...81 GR CY 3 4...
Page 87: ...82 GR CY 5 a b 100 mm c d e f 100 mm g h i j k...
Page 88: ...83 GR CY l m n o p q r E s 1 2 3 4 5 6 EN 847 1 7 HSS 8 9 10 11 12 13 14 1 3 15 16 17 18 19 20...
Page 95: ...90 GR CY VDE DIN 220 240 V 25 m 1 5 15 2012 19...
Page 96: ...91 GR CY 16...
Page 114: ......
Page 115: ......