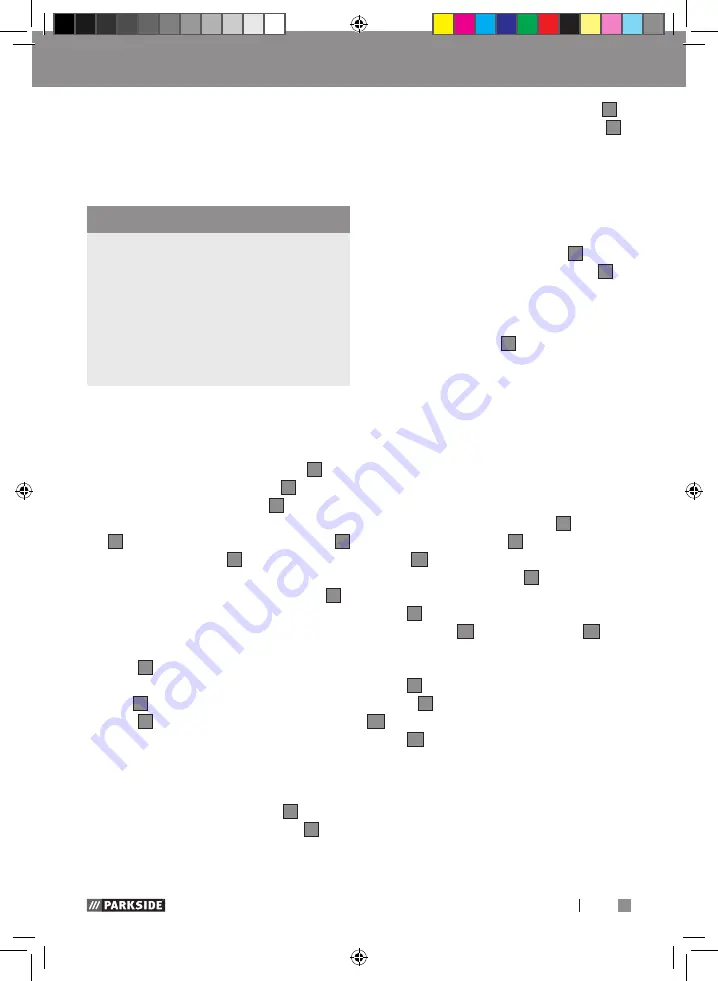
17
GB/CY
It must be operated in a dry and well
ventilated working environment.
• Connecting compressed air
PLEASE NOTE!
f
This device is designed for operating
pressure (output pressure at the com-
pressor) of up to 6.3 bar. Please bear in
mind that the pressure can lower while
setting the air pressure. Thus, in a hose
length measuring 10 m and an internal
diameter of 9 mm it drops by approx.
0.6 bar.
The compressed air source must have a filter
and regulator.
Connect the compressed air hose
16
on
the back of the plasma cutter
1
to the
compressed air connection
20
. To do so,
insert the side of the compressed air hose
16
into the compressed air connection
20
of the plasma cutter
1
without a quick
connector (see Fig. I).
The pressure can be set via the knob
21
on the condensate separator (see
Fig. I-L). Select a pressure of 4–4.5 bar.
In order to release the compressed air
hose
16
, you must press the locking
mechanism of the compressed air connec-
tion
20
and pull out the compressed air
hose
16
at the same time (see Fig. I).
• Connecting the cutting torch
Insert the plasma burner plug
7
into the
plasma burner connection socket
12
and tighten the union nut hand-tight
(see Fig. A+B).
Insert the plasma burner power plug
6
into the plasma burner power socket
10
and tighten the union nut hand-tight
(see Fig. A+B).
• Connecting the ground cable
Connect the ground terminal plug
5
with
the ground terminal - connection socket
11
.
Make sure that the connecting shaft is first
connected and then turned. The connecting
shaft must face upwards when plugging in
the ground cable plug
5
. After plugging in,
the connecting shaft must be rotated in a
clockwise direction until it reaches the stop,
in order to lock it in place (see Fig. A+B).
This does not require force!
• Fitting the removable roller
guide (optional)
Push the removable roller guide
23
over the
nozzle clamping sleeve
8b
, until the locking
screws
23a
are completely above the black
area of the plasma burner
8
(behind the
gap at the back of the nozzle clamping
sleeve
8b
) (see Fig. A+B). Now fix the
locking screws
23a
. The guide rollers
23c
are
now positioned such that the required
distance between the workpiece and burner
sleeve
8c
is set. The roller guide is then fixed
in place
23
by tightening the fixing screws
23b
(see Fig. N). Make sure that both guide
rollers
23c
are always set to the same height,
in order to enable straight cutting. You can
see a correctly fitted roller guide in Fig. N.
Before use
327358_Plasmaschneider_PPS_40_B2_content_LB7.indb 17
13.09.2019 08:42:44
Summary of Contents for 327358 1904
Page 26: ...26 GB CY 327358_Plasmaschneider_PPS_40_B2_content_LB7 indb 26 13 09 2019 08 42 45 ...
Page 48: ...48 HR 327358_Plasmaschneider_PPS_40_B2_content_LB7 indb 48 13 09 2019 08 42 48 ...
Page 141: ...141 DE AT CH 327358_Plasmaschneider_PPS_40_B2_content_LB7 indb 141 13 09 2019 08 43 01 ...
Page 142: ...142 DE AT CH 327358_Plasmaschneider_PPS_40_B2_content_LB7 indb 142 13 09 2019 08 43 01 ...
Page 143: ...143 DE AT CH 327358_Plasmaschneider_PPS_40_B2_content_LB7 indb 143 13 09 2019 08 43 01 ...
Page 144: ...144 DE AT CH 327358_Plasmaschneider_PPS_40_B2_content_LB7 indb 144 13 09 2019 08 43 02 ...