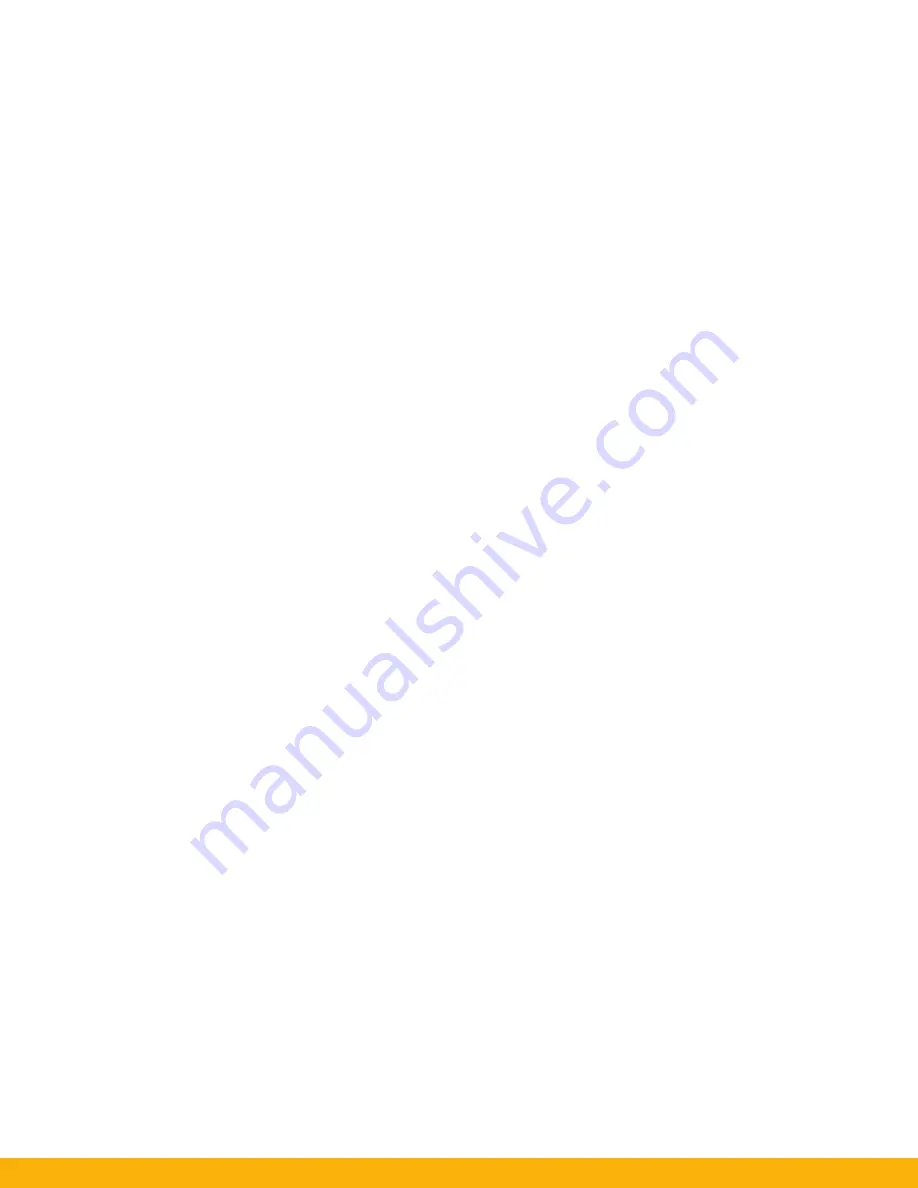
19
Parts should be replaced as required.
Remove the unicells and inspect for the following:
Collector Cell Conditions Causing Failure
• Dirty collector cell(s) (contaminant build up bridging the cell plates
and or on cell triangular insulators front/rear) requiring manual
cleaning.
• “Wet” collector cell(s), not properly dried after a wash cycle or
manual cleaning procedure, use compressed air to accelerate the
drying time.
• Deformed collector cell contact springs contacting a “grounded
surface”.
•
Misaligned contact springs (contacting a grounded surface)
between the outer and inner most cells if module is equipped with
two unicells and or at high voltage feed through insulators. Refer
to Figure 6.
• Bent cell plate(s) contacting the opposing cell plate(s).
• Warped cell plate (s) which could be due to high duct operating
temperature, consult Parker.
• Carbon tracking to the cell high voltage feed through insulator and
or cell triangular insulators, imbedded black streak which cannot
be removed by cleaning (replace insulator).
• Surface oxidation to unicell component requiring a replacement.
• Unicell is structurally weak, loose steel rivets, deterioration to cell
plate spacers or paper thin cell plates due to utilizing the improper
detergent.
• Place power in the off position, open the component
door, and remove unicell(s).
• Place toggle switch in the on position and engage
interlock switch. If the indicator light is illuminated the
problem is within the ionizer section. If the indicator light
is flashing the problem is the high voltage feed through
insulator (dirty, cracked, carbon tracking) and or the
high voltage wire (broken wire or wire insulation has
deteriorated causing a dead short condition).
Parts should be replaced as required.
Remove the unicell(s) and inspect for the following:
Ionizer Conditions Causing Failure
•
Dirty ionizer(s) (contaminant build up) requiring manual
cleaning.
•
“Wet” ionizer(s), not properly dried after a wash cycle
or manual cleaning procedure, use compressed air to
accelerate the drying time.
• Deformed ionizer contact springs contacting a “grounded
surface”.
• Misaligned contact springs (contacting a grounded surface)
between the outer and inner most ionizer, if module is
equipped with two unicells, or at the ionizer high voltage feed
through insulator. Refer to Figure 6.
• Broken ionizer wires.
•
Contaminant build up and or cracked ionizer stand off
insulators and or high voltage feed through insulators.
•
Carbon tracking (black streak) to the ionizer stand off
insulators and or high voltage feed through insulator (replace
insulator)
• Ionizer wires not “taut” contacting the ground plates.
• Bent ionizer wire support bar contacting a “grounded
surface.”
• Bent ground plates contacting the ionizer wires.
• Surface oxidation to unicell component requiring
areplacement.
10.5 STEP 2 — Checking the Unicell
Components Indicator Light is Flashing
Do not proceed with step (2) until step (1) is completed. The
following steps are the process of elimination in identifying the
problems to the ionizer/collector cell circuits. There are four
conditions which could occur with a flashing indicator light.
1. The high voltages are below specifications to the ionizer and
or the collector cell circuit(s).
2. There is an arcing condition to the ionizer and or collector cell
circuit(s).
3. There is a dead short condition.
4. The power pack has failed. Refer to Step 1.
(a) Place the toggle switch in the off position, and open power pack
lid door. Disconnect high voltage wire #8 to the ionizer connector
with high voltage wire #7 (Collector) connected to the power
pack and place the toggle switch in the on position, and engage
interlock switch.
The indicator light should be illuminated. If so, the cell circuit is
operational proceed to (b). If indicator light is flashing perform the
following.
• Place toggle switch in the off position, open component
door, and remove the unicell(s).
• Place toggle switch in the on position, and engage interlock
switch. The indicator light should be illuminated. If the
indicator light is illuminated the problem is within the collector
cell section. If the indicator light is flashing the problem is the
high voltage feed through insulator (dirty, cracked, carbon
tracking) and or the high voltage wire (broken wire or wire
insulation has deteriorated causing a dead short condition).
Parts should be replaced as required or replacement of
unicell.
Sometimes a flashing indicator light will clear itself by
removing the unicell(s) from the module and then installing
the unicell(s) back into the module.
The Bench Test Procedure will determine which unicell(s) are
causing a flashing indicator light. Refer to Section 10.7.
Place toggle switch in the off position; connect all wires
which have been disconnected and install unicell(s).
(b) Indicator light is illuminated with the high voltage wire
#7 connected to the collector cell connector on the power
pack. Place toggle switch in the off position and connect
high voltage wire #8 to the ionizer connector on the power
pack. Place the toggle switch to the on position and engage
the interlock switch.
The indicator light should be illuminated? If so, the unicell(s)
are operational. If the indicator light is flashing perform the
following.