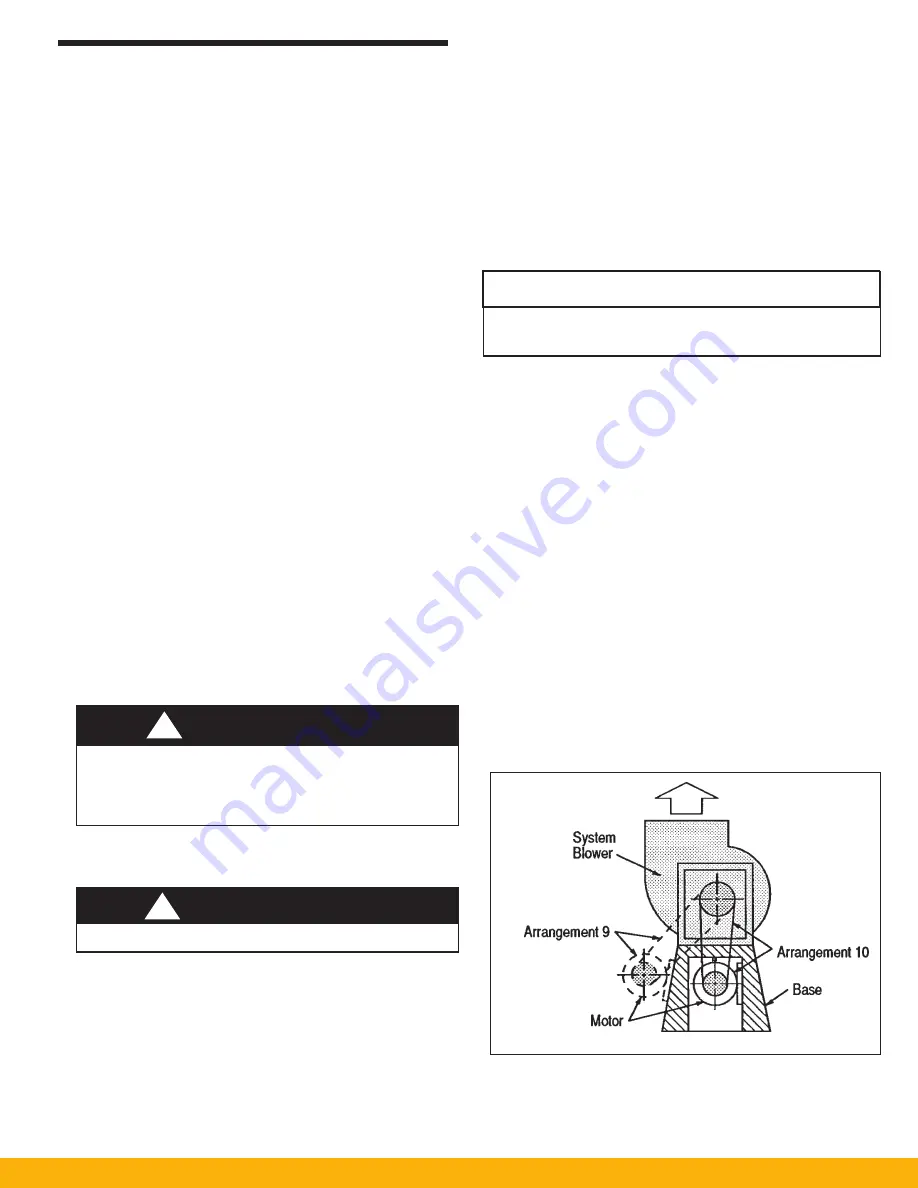
9
4. Operation
4.1 Start-up Checks
4.1.1 Installing Components
If unicells and filter media were removed for shipment or
installation, refer to Figure 6 for proper installation and electrical
contact alignment. Filter media is installed as after filters (after
the unicell) with In Place Cleaning. Do not install filter media
as pre filters (before the unicell) with In Place Cleaning. This
will reduce the effectiveness of the wash cycle by 50 percent.
The filter media is utilized as pre and after filters if the PSG is
not equipped with In Place Cleaning. The PSG inlet plenum, if
supplied by Parker, will have baffle filters or aluminum media.
The inlet plenum should be inspected that all baffle filters or
aluminum filters are installed.
4.1.2 Ducting Connections
Blower speeds are factory set by the blower manufacturer to
compensate for static pressure losses in ducting as specified
by others. Starting the blower before ducting is complete or
before debris is removed can result in motor overload or other
system damage.
4.1.3 Blower Rotation
For proper airflow, the blower should be operating in the correct
direction. If the blower is operating in the reverse direction, air
will move in the proper direction, but at significantly reduced
rates. To check rotation:
1. Place PSG unit off line.
2. Remove blower housing from the blower to observe the
pulley rotation.
3. Place the PSG unit on line for approximately one minute.
4. Place PSG unit off line.
5. As the blower pulley slows down, observe the direction of
rotation.
6. Note directional arrow located on the blower housing.
Extreme care should be exercised when operating
blowers with motor/drive belts exposed. Loose
fitting clothing can easily be drawn into these
moving parts.
7. If blower wheel was not rotating in the correct direction,
disengage main three-phase fused disconnect switch.
Do not attempt to rewire “live” electrical connections.
8. Open power panel and reverse any two of the three wires
at the terminal strip (Ll, L2, and L3).
9. Engage the main three phase fused disconnect switch and
place the PSG on line, checking blower rotation.
!
WARNING
!
WARNING
4.1.4 Blower Belt Tension
The drive belt tension adjustment is critical within the first 24
hours of the system exhaust blower operation. During this 24
hour period, the initial stretch of the belt occurs which requires
a belt tension adjustment. If this tension adjustment is not
completed the belt will wear prematurely, requiring a replacement. A
drive belt tension gage should be used for adjusting belt tension. If
fan belt tension is improper, set tension by adjusting the motor slide
base. Loosen four bolts holding the motor to the base and turn the
adjustment bolt(s) on the base. Check with a steel straight edge to
make sure that motor pulley and blower pulley is still aligned. Tighten
motor mounting bolts. Figure 7 illustrates a typical motor/blower
arrangement (motor/blower configurations will vary).
Improper tension on drive belts will cause premature
failure of belts.
4.1.5 Blower Current Measurement
Using an ammeter measure the current amperage of the blower
motor. The measurement should not exceed the full load ampere
(FLA) rating identified on the blower motor nameplate. If the over-
load relay is tripping perform the following: check overload relay
for proper setting per motor FLA, measure blower rpm and design
static pressure to determine that actual conditions are per blower
specifications. Blower rpm can be measured with a tachometer.
Design or total static pressure (TSP) is the summation in static pres-
sure between the blower inlet and outlet. This summation is best
checked with a manometer and pitot tube measuring readings from
(a) the exhaust transition near the blower inlet and (b) the exhaust
stack after the blower outlet. If the actual static pressure is higher
than the blower specifications, and or the blower rpm is higher than
the blower specifications, reduce the blower speed by opening the
variable pitch pulley as described in the next procedure. Blower
specifications or blower curve refers to the established operating
conditions set by the blower manufacturer, rpm, cfm (air volume),
and TSP. A reduction in blower rpm will decrease the TSP. A new
pulley set may be required to reduce the blower rpm and amperage.
The blower can be supplied either by Parker or by others. A blower
curve can be requested through the blower manufacturer with the
serial number.
Figure 7
Typical Motor/Blower Configuration
CAUTION