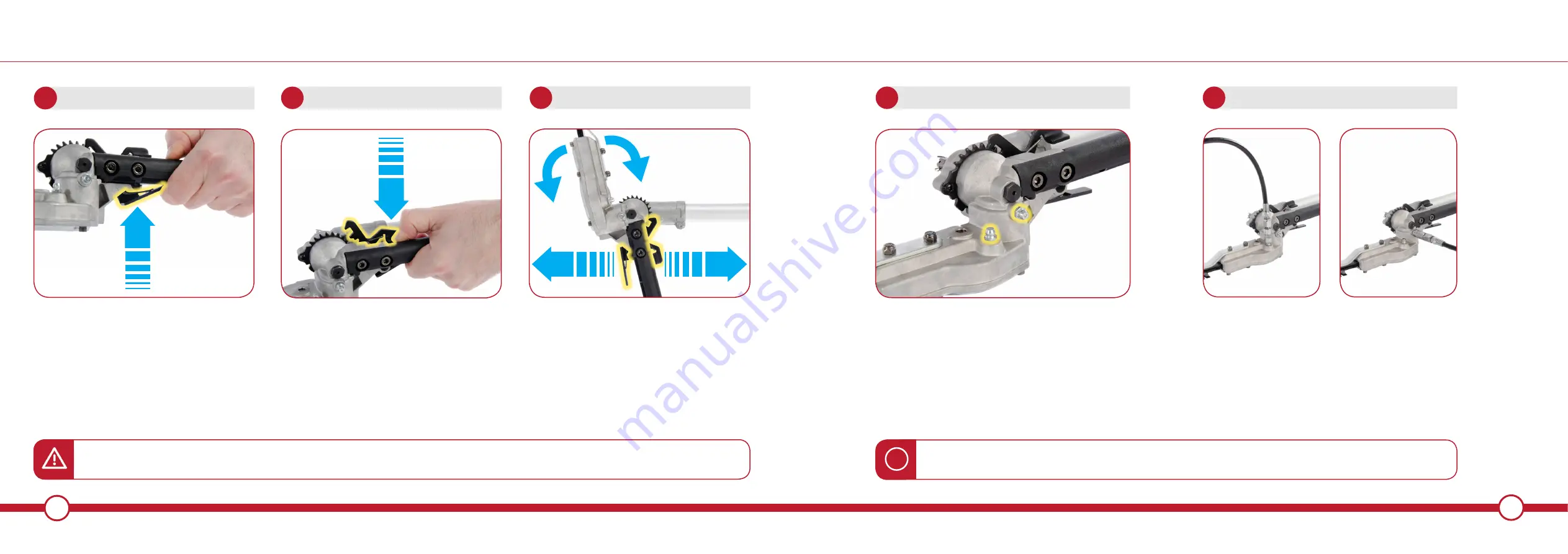
34
35
HEDGE TRIMMER GEARBOX LUBRICATION
ADJUSTING HEDGE TRIMMER ANGLE
With the engine stopped, grip the
adjustment handle
Lift the angle adjustment locking lever with
your index finger and hold
1
LOCKING LEVER
1
2
ANGLE ADJUSTMENT LEVER
Whilst still holding the angle adjustment
locking lever, press down with your thumb
on the angle adjustment lever and adjust
the cutting head to a suitable angle.
WARNING!
The Hedge Trimmer adjustment handle contains moving parts which could cause injury if used incorrectly.
NOTE:
Always wear safety gloves when operating moving parts to help prevent the risk of injury.
Once the cutting head is adjusted to the
required angle, release the levers to lock
the cutting head into position.
2
ADJUSTMENT & LOCK
The components within the Hedge Trimmer
gearbox have to work very hard and as a result
MUST remain well lubricated at all times. Before or
after each use.
There are two grease nipples on the Hedge
Trimmer gearbox housing. Be sure to add grease
to both.
Connect a compatible grease gun to the gearbox
assembly's grease nipples.
Pump gearbox grease into the grease nipples.
Use a general purpose gearbox grease.
1
HEDGE TRIMMER GREASE NIPPLES
2
ADD GREASE TO HEDGE TRIMMER
WARNING!
Use an appropriate gearbox grease. Failure to do so can result in unit failure.
NOTE:
Always keep gearbox lubricated either before or after use. Lack of lubrication can cause unit failure
i