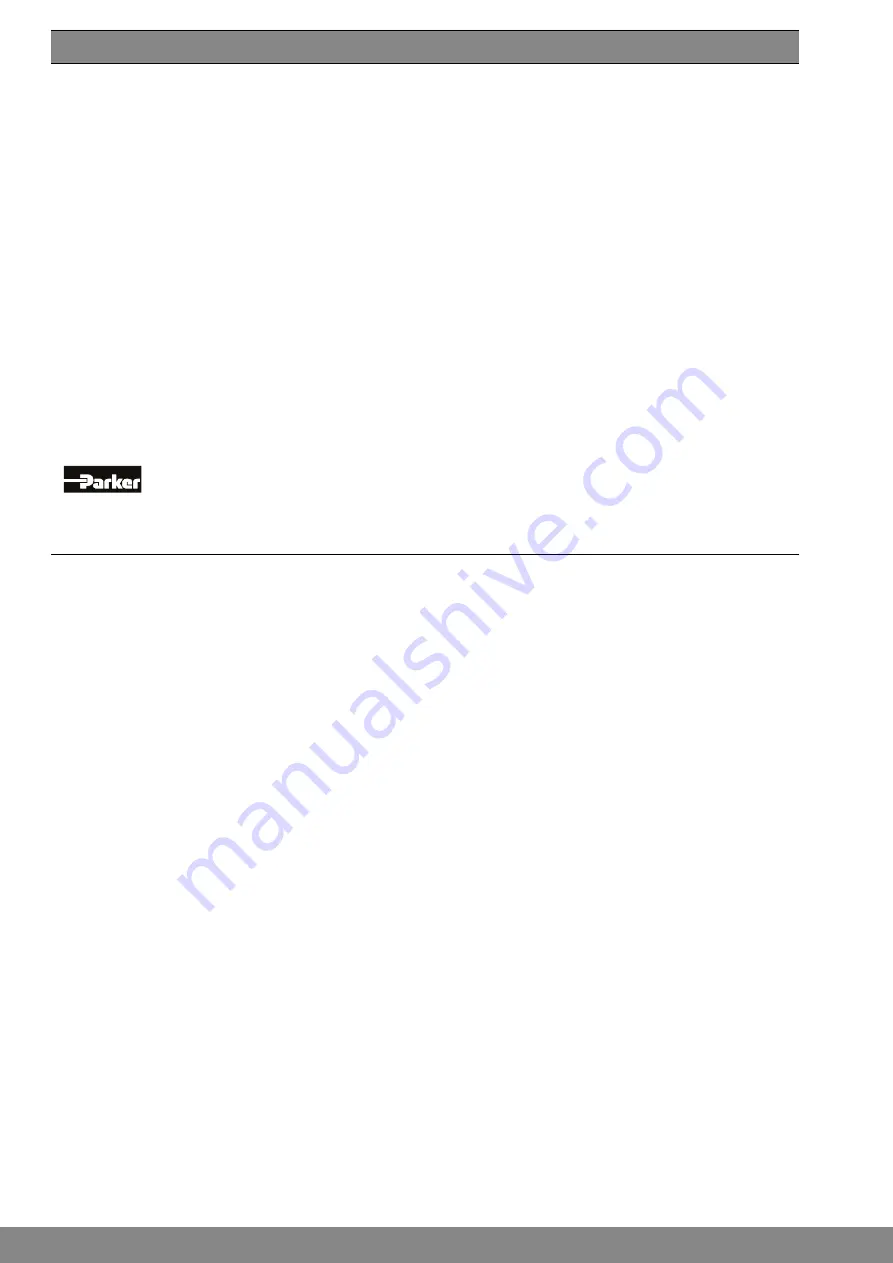
6
Pneumatic Linear Drive OSPP-Classic / KF
Conversions and alterations
The linear drives shall not be modified in its construction and safety aspects, without the prior written ap-
proval of
Parker Hannifin GmbH
. Any such modifications carried out without approval will rule out all liability
on the part of
Parker Hannifin GmbH.
In principle, no safety and protection devices/equipment shall be dismantled or put out of operation.
When installing special attachments, the assembly regulations of
Parker Hannifin GmbH
shall be observed as
required.
The following regulatory instruments must be observed as a matter of course:
• Relevant rules and regulations for accident prevention.
• Generally recognised safety regulations.
• EU Directives.
• Country-specific provisions.
Dangers after shutting down the OSPP-Classic / OSPP-Classic-KF or the whole plant
Even after venting the whole plant there can still be pressure in the cylinder. This can cause uncontrolled
movements of the piston. Observe the Operating Instructions for the whole plant.
Reversal of Movement in an Emergency
See the operating instructions for the whole plant.
Replacement Parts
In the interest of safety, only original replacement parts and accessories approved by
Parker Hannifin GmbH
should be used. The use of other parts can change the characteristics of the Linear Drive.
We take no responsibility for consequences arising from this.
3
Guarantee
We reserve the right to modify these Operating Instructions and the technical details of the data and dia-
grams in the Operating Instructions.
The
Parker Hannifin GmbH
gives no quality or service life guarantees and no guarantees of suitability for spe-
cific purposes. These must be agreed explicitly in writing.
Statements in sales literature, advertisements or other promotional media do not constitute guarantees.
The rights of the user under guarantee are on condition that the user informs us of the problem without
delay and describes it accurately in his complaint. The
Parker Hannifin GmbH
cannot be held responsible for
damage to the product itself or for consequential damage caused by the product where this has been caused
by improper use of the product. Insofar as the
Parker Hannifin GmbH
accepts responsiblity, the
Parker Hannifin
GmbH
may either repair or replace the product at its sole discretion.
Within the framework of ISO 9000, all Linear Drives bear a type label. This type label must not under any
circumstances be removed or destroyed.
Any liability of
Parker Hannifin GmbH
– regardless of its basis in law – exists only if there has been intent or
gross negligence, or culpable injury to life, body or health, or product defects which have been fraudulently
concealed or whose absence has been explicitly guaranteed in writing. Furthermore liability can exist insofar
as there is liability for personal injury and damage to privately used property under the Product Liability law.
All other claims are excluded.
Any guarantee is voided by non-compliance with these Operating Instructions, with relevant legal regulations
or with other notes or instructions from the supplier.
In particular
Parker Hannifin GmbH
is not responsible for problems caused by modifications made by the cus-
tomer or by a third party. In such cases normal repair costs will be charged. There will also be a charge for
inspecting the product if no defect could be found in the product. This rule also applies during the guaran-
tee period.
No rights exist in respect of continued availability of previous versions of a product or in respect of upgrad-
ing products already supplied to current technical status.