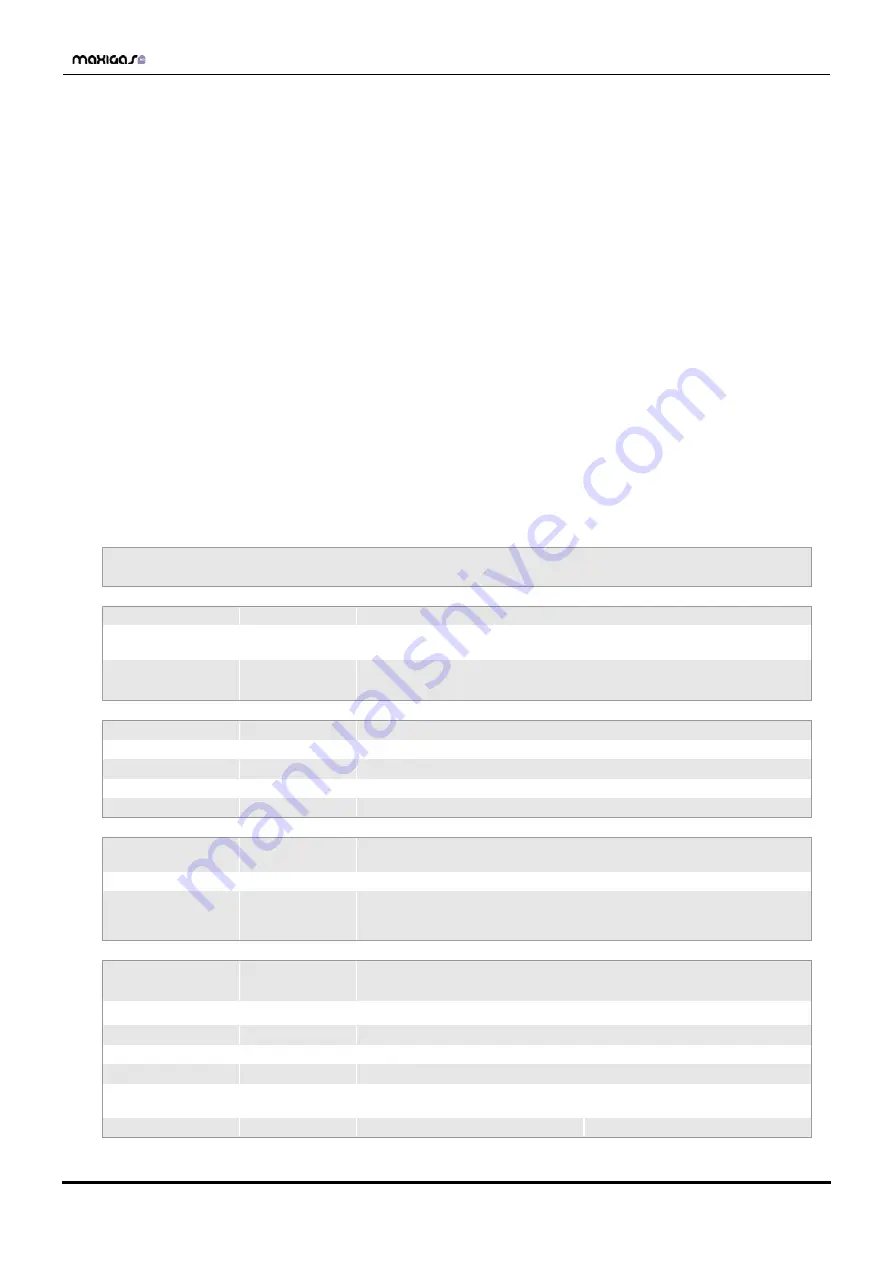
6
2 Description
The MAXIGAS range of nitrogen generators operates on the Pressure Swing Adsorption (PSA) principle to produce a continuous stream of
nitrogen gas from clean dry compressed air.
Pairs of dual chamber extruded aluminium columns, filled with Carbon Molecular Sieve (CMS), are joined via an upper and lower manifold to
produce a two bed system. Compressed air enters the bottom of the ‘online’ bed and flows up through the CMS. Oxygen and other trace gases
are preferentially adsorbed by the CMS, allowing nitrogen to pass through.
After a pre-set time the control system automatically switches the bed to regenerative mode. All of the contaminants are vented from the CMS
and a small portion of the outlet nitrogen gas is expanded into the bed to accelerate the regeneration. At the same instant the second bed
comes on-line and takes over the separation process.
The lower purity (%) generators use an equalisation phase designed to reduce energy consumption and enhance the overall performance of the
generator. Immediately after the adsorption phase the inlet, outlet and exhaust valves close on both beds. The upper and lower equalisation
valves open, allowing the pressure to equalise between the beds.
Once equalised the bed entering regeneration is depressurised. The oxygen adsorbed during the adsorption phase is vented to atmosphere via
an exhaust valve and silencer. The bed entering the adsorption phase is pressurised using a controlled flow of nitrogen gas from the nitrogen
buffer vessel (Back Fill) and a controlled flow of clean, dry, particulate free compressed air (Front Fill).
The CMS beds alternate between separation and regeneration modes to ensure continuous and uninterrupted nitrogen production.
The oxygen concentration in the nitrogen stream is analysed continuously. If the concentration exceeds the required production level, the
nitrogen outlet is closed and the gas is vented to atmosphere. Normal operation will resume when the purity recovers.
2.1 Technical Specification
Parameter
Units
MAXIGAS
104
106
108
110
112
116
120
Inlet Air Quality
ISO 8573.1: 2001
Class 3.2.2
Inlet Pressure
barg
(psig)
6 – 10 and 10 - 18
(88 – 145) and (145 - 261)
Inlet Temperature
o
C
(
o
F)
5 – 50
(41 – 122)
Port Connections
Air Inlet
G1”
N2 Outlet to Buffer
G1”
N2 Inlet from Buffer
G1/2”
N2 Outlet
G1/2”
Supply Voltage
V ac
(50/60Hz)
115 / 230 ± 10%
Power
W
38
Fuse
A
3.15
(Anti Surge (T), 250v, 5 x 20mm HBC,
Breaking Capacity 1500A @ 250v, UL Listed)
Ambient Temperature
o
C
(
o
F)
5 – 50
41 – 122
Humidity
50% @ 40
o
C (80%
MAX
d
31
o
C)
IP Rating
IP20 / NEMA 1
Pollution Degree
2
Installation Category
II
Altitude
m
(ft)
< 2000
(6562)
Noise
dB(A)
<75
<80
Summary of Contents for MAXIGAS MX104
Page 2: ......