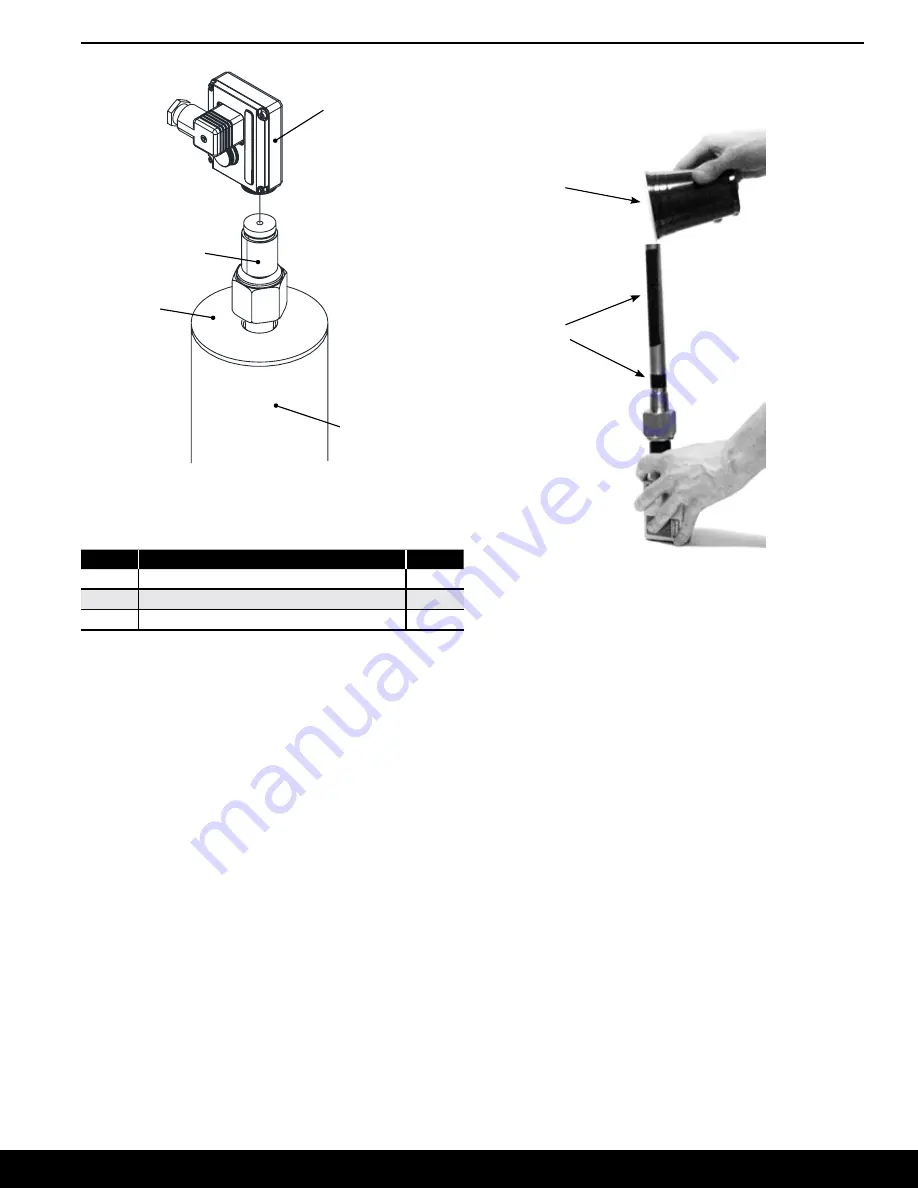
Bulletin 61-60
7
Explosion View:
Probe Replacement Kits
Item
Kit Description
Kit
1
Electronic Head, Assembly
209329
1
Electronic Head, Assembly with Bar Graph
209330
2
Column Cap, Pipe (3" or 4" Diameter Column)
205873
Calibrating On-Site
All replacement electronics, or probe assemblies reset to the
factory setting are pre-calibrated to ammonia with a sensor tube
length of 1500 mm/59” and a signal damping of 15 seconds. When
installed on all other lengths it has to be re-calibrated on site.
Calibrating for ammonia on site:
HBLT probes straight from the factory are pre-calibrated to the
manufactured probe length, so there is no need to re-calibrate.
Probe assembles that have been reset to the factory settings must
follow the
adjusting the minimum and maximum calibration
points
instructions described earlier in this document.
The benefit of ammonia is water can be used as a substitute.
Ammonia and water have the same properties with the respect to
capacitive measurements. This is very convenient as water is much
easier and safer than dealing with ammonia.
For the low level calibration, stick the bottom of the probe into a
small container. Fill the water level to the desired low level height
and follow calibration instruction for minimum level described
earlier in this document under the calibration section.
When it comes to calibrating the height level it is much more
difficult, because finding a container/tube long enough, especially
for length greater than 1397 mm (55"), is not quite so easy. A work
around to this problem can be solved by following these steps.
1. Turn the HBLT probe upside down.
1
Probe
2
3" or 4" Dia.
Column
Tape
Water
2. Tape all hole on the sleeve, otherwise known as reference pipe,
to prevent any water from leaking out. The 4-20 mA output
signal is not inverted despite the upside down position.
3. Fill the pipe with water according to your calibration needs.
With the sleeve full of water at the high level desired calibration
can be carried out by following the maximum calibration
instructions described earlier in this document under the
calibration section.
Calibrating a replacement probe head for ammonia on site :
Follow the procedures below to re-calibrate a replacement
electronic heads:
1. Install the HBLT electronic head to the existing probe and
connect power.
2. To calibrate the minimum level the column or vessel needs to
be free of liquid. Follow the minimum calibration instructions
described earlier in this document.
3. To calibrate the maximum level the column or vessel needs to
be fully submerged by ammonia liquid. Follow the maximum
calibration instructions described earlier in this document.
4. If methods 2 & 3 cannot be carried out use the on-site method,
but before proceeding with this method the column/standpipe
or vessel needs to be isolated and free of refrigerant.
Calibrating for refrigerants other than ammonia on-site:
When calibrating for refrigerants other than ammonia utilize the
on-site calibration instructions. Calibrate the probe for ammonia
and then change the refrigerant by following the
set of refrigerant
instructions described earlier in this document. If using the
upside down method for calibrating the HBLT probe; make sure to
remove all tape and clean/dry the probe prior to installation.