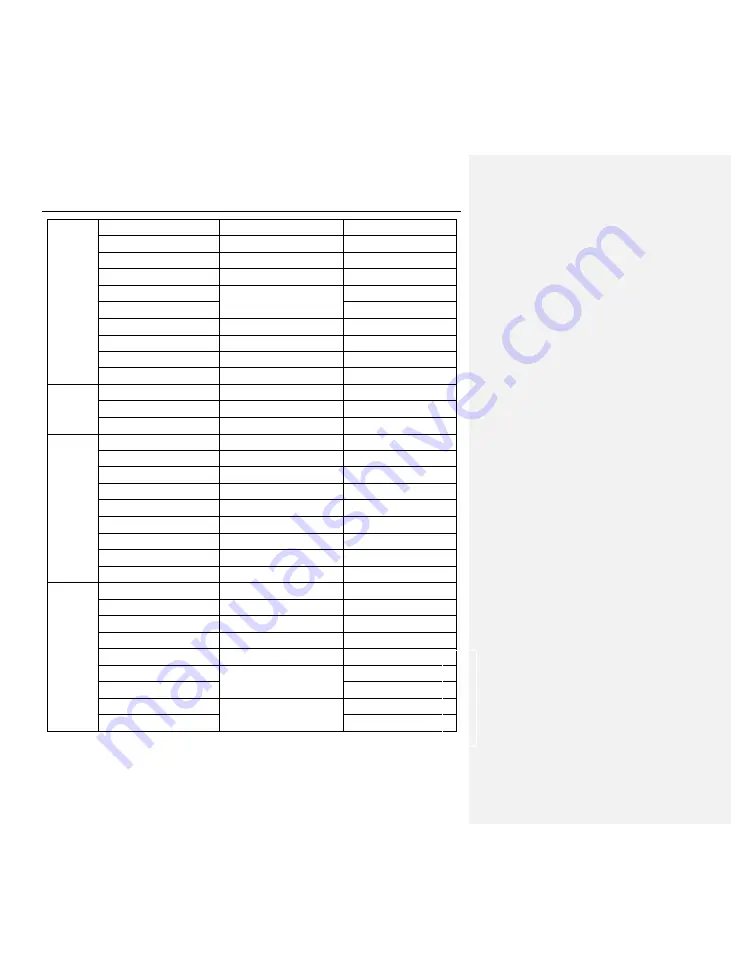
320
FMMB-752*6A**
FL20-CA752T3MM4
HK4B-4PO-*M-4.0
FM15-0082*6EE*FL
FL20-CA752T3MM4
ZL4-4PO-*M-4.0
FM15-0100*6EE*FL
FL20-CA113T3MM4
ZL4-4PO-*M-6.0
FM15-0124*6EE*FL
FL20-CA153T3M4
ZL4-4PO-*M-6.0
FM15-0160*6EE*FL
FL20-CA183T3M5
ZL4-4PO-*M-10.0
FM15-0180*6EE*FL
ZL4-4PO-*M-10.0
FM15-0210*6FE*FL
FL20-CA223T3M5
ZL4-4PO-*M-10.0
FM15-0240*6EE*FL
FL20-CA303T3M6
ZL4-4PO-*M-16.0
FM15-0290*6FE*FL
FL20-CA303T3M6
ZL4-4PO-*M-16.0
FM15-0350*6FE*FL
FL20-CA373T3M6
ZL4-4PO-*M-25.0
FML
series
1000r/min
FMLA-372*6A**
FL20-CA452T3M3
HK4B-4PO-*M-2.5
FMLA-102*67**
FL20-CA152T3M2
HK4B-4PO-*M-0.75-B
FMLA-292*6A**
FL20-CA302T3M3
HK4B-4PO-*M-1.5
FMM
series
1700r/min
i
n
FM17-0075*6EE*FL
FL20-CA752T3MM4
ZL4-4PO-*M-4.0
FM17-0092*6EE*FL
FL20-CA113T3MM4
ZL4-4PO-*M-6.0
FM17-0110*6EE*FL
FL20-CA113T3MM4
ZL4-4PO-*M-6.0
FM17-0140*6EE*FL
FL20-CA153T3M4
ZL4-4PO-*M-6.0
FM17-0180*6EE*FL
FL20-CA183T3M5
ZL4-4PO-*M-10.0
FM17-0210*6FE*FL
FL20-CA223T3M5
ZL4-4PO-*M-10.0
FM17-0240*6EE*FL
FL20-CA303T3M6
ZL4-4PO-*M-16.0
FM17-0270*6EE*FL
FL20-CA303T3M6
ZL4-4PO-*M-16.0
FM17-0330*6FE*FL
FL20-CA373T3M6
ZL4-4PO-*M-25.0
FMM
series
2000r/min
FM20-0070*6EE*FL
FL20-CA752T3MM4
ZL4-4PO-*M-4.0
FM20-0100*6EE*FL
FL20-CA113T3MM4
ZL4-4PO-*M-6.0
FM20-0140*6EE*FL
FL20-CA153T3M4
ZL4-4PO-*M-6.0
FM20-0180*6EE*FL
FL20-CA183T3M5
ZL4-4PO-*M-10.0
FM20-0220*6EE*FL
FL20-CA223T3M5
ZL4-4PO-*M-10.0
FM20-0250*6EE*FL
FL20-CA303T3M6
ZL4-4PO-*M-16.0
FM20-0280*6EE*FL
ZL4-4PO-*M-16.0
FM20-0300*6EE*FL
FL20-CA373T3M6
ZL4-4PO-*M-16.0
FM20-0360*6FE*FL
ZL4-4PO-*M-25.0
N
2
01
806
190
3