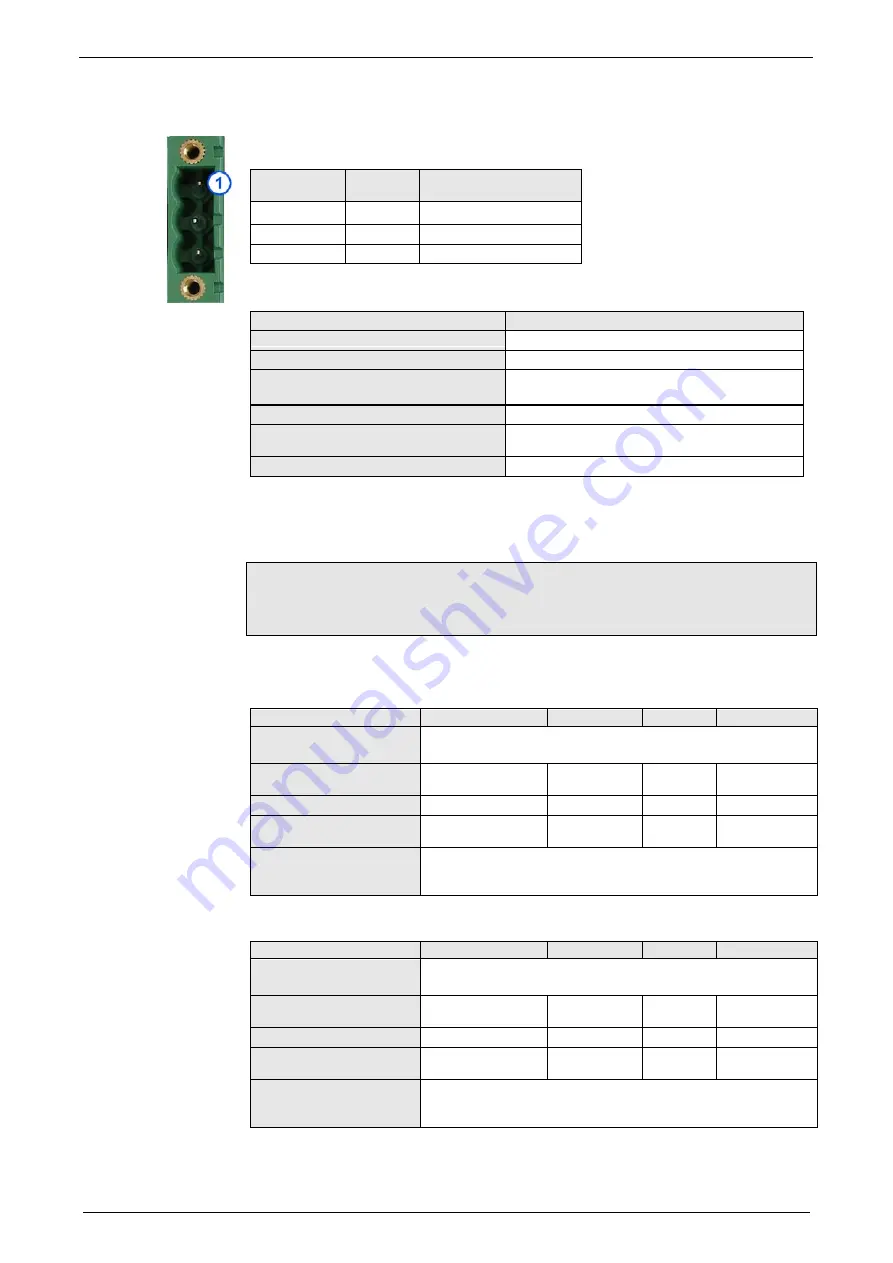
Parker EME
Connections of Compax3H
192-120149 N08 June 2014
27
3.4.6.
Control voltage 24 VDC C3H
Connection of control voltage 24VDC
figure
(see on page
Connector
X4 Pin
Descripti
on
1
NC
NC
2
GND24V
GND
3
+24 V
24 VDC (power supply)
Control voltage 24VDC Compax3S and Compax3H
Controller type
Compax3
Voltage range
21 - 27VDC
Current drain of the device
0.8 A
Total current drain
0.8 A + Total load of the digital o current
for the motor holding brake
Ripple
0.5Vpp
Requirement according to safe extra
low voltage (SELV)
yes
Short-circuit proof
conditional (internally protected with 3.15AT)
3.4.7.
Mains connection Compax3H
Avoid permanent switching on and off so that the charging connection is not
overloaded. Therefore wait at least 1 minute before switching on the device
again.
Connection of mains voltage
figure
(see on page
Mains connection Compax3HxxxV4 3*400VAC
Device type Compax3
H050V4
H090V4
H125V4
H155V4
Continuous working
voltage
Three-phase 3*400VAC
350-528VAC / 50-60Hz
Receiver current
consumption
66Arms
95Arms
143Arms
164Arms
Output current
50Arms
90Arms
125Arms
155Arms
Maximum input fuse
rating per device
80A
100A
160A
200A
Recommended line
protection in accordance
with UL
JDDZ Class K5 or H
JDRX Class H
Mains connection Compax3HxxxV4 3*480VAC
Device type Compax3
H050V4
H090V4
H125V4
H155V4
Continuous working
voltage
Three-phase 3*480VAC
350-528VAC / 50-60Hz
Receiver current
consumption
54Arms
82Arms
118Arms
140Arms
Output current
43Arms
85Arms
110Arms
132Arms
Maximum input fuse
rating per device
80A
100A
160A
200A
Recommended line
protection in accordance
with UL
JDDZ Class K5 or H
JDRX Class H
Device protection
This manual was downloaded on www.sdsdrives.com
+44 (0)117 938 1800 - [email protected]