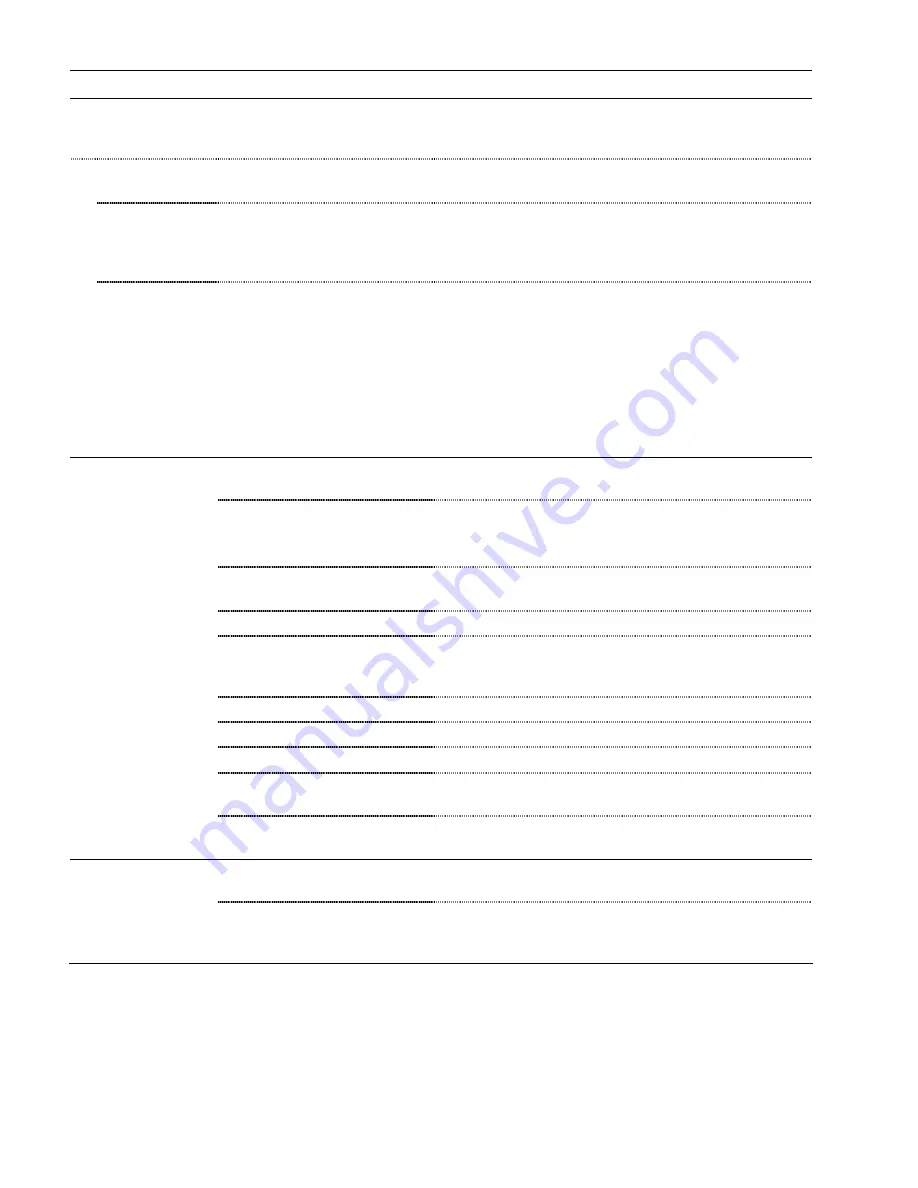
40
6K Hardware Installation Guide
Problem Cause
Solution
LEDs:
All other LED states indicate hardware
conditions; refer to your product's
Installation Guide for details.
“POWER” LED is
off.
1. No power.
1. Check 24 VDC power connection and restore power.
“POWER” LED is
red.
1. General fault.
2. ENABLE input not grounded.
1. Reset the controller by one of these methods:
•
Cycle
power
•
Issue
the
RESET
command
2. Ground the ENABLE input.
An “AXIS” LED is on
(red).
1. Drive was commanded to shut
down (
DRIVE0
). If Disable Drive on
Kill mode is enabled (
KDRIVE1
), a kill
command or kill input will also
disabled the drive.
2. Servo Axes: Maximum position
error (
SMPER
value) exceeded. Could
be caused by disconnected or mis-
mounted feedback device.
1. Re-enable the drive by sending a
DRIVE1
command to the
affected axis.
2. (verify position error by checking to see if
TAS
/
TASF
bit #23 is set)
Check feedback device connection and mounting and re-enable
drive by sending
DRIVE1
command to the affected axis.
Motion does not occur.
1. “AXIS” LED is red, or “POWER”
LED is off or red.
1. See LED troubleshooting as noted above.
2. End-of-travel limits are active.
2.a. Move load off of limits or disable limits by sending the
LHØ
command to the affected axis.
2.b. Software limits: Set
LSPOS
to a value greater than
LSNEG
.
3. Step pulse too narrow for drive to
recognize (stepper axes only).
3. Set pulse width to drive specifications using the
PULSE
command.
4. Drive fault level incorrect.
4. Set drive fault level using the
DRFLVL
command.
5. Improper wiring.
5. Check drive fault & limit connections.
Stepper Axes: check step and direction connections.
Servo Axes: check command and shutdown connections.
6. ENABLE input is not grounded.
6. Ground the ENABLE input connection.
7. Load is jammed.
7. Remove power and clear jam.
8. No torque from motor.
8. See problem:
Torque, loss of
.
9. Max. position error (
SMPER
value)
exceeded. (servo axes only)
9. Check to see if
TAS
/
TASF
bit #23 is set, and issue the
DRIVE1
command to the axis that exceeded the position error limit.
10. Drive has activated the drive fault
input.
10. Check to see if
TAS
/
TASF
bit #14 is set, and check the drive fault
level (
DRFLVL
).
Power-up Program does
not execute.
1. ENABLE input is not grounded.
1. Ground the ENABLE input to GND and reset the product.
(see page 9)
2.
STARTP
program is not defined.
2. Check the response to the
STARTP
command. If no program is
reported, define the
STARTP
program and reset (refer to the
STARTP
command description).
www.comoso.com