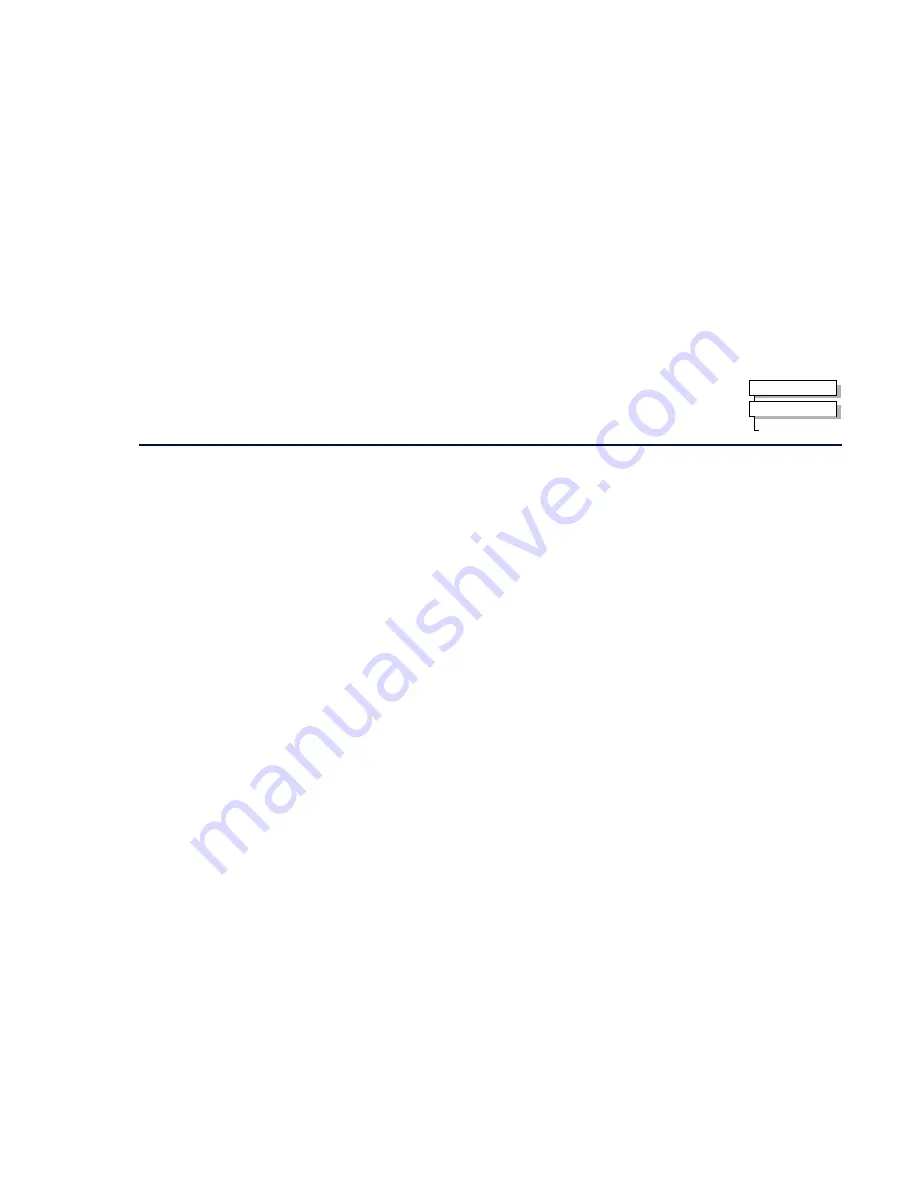
Control Loops
5-1
DC590+ DRV Series DC Digital Drive
Control Loops - Principle of Operation
NOTE
Selection between Current Control or Speed Control (default) is made by the I DMD ISOLATE (current demand
isolate) parameter using Digital I/P3 (Terminal C8). If ENABLED the Drive operates as a current controller, and if
DISABLED (the default) it operates as a speed controller.
Current Loop
The current loop accepts a demand from either the speed loop, or directly from the plant, and forms an error signal which is the difference between
demand and average value of feedback. The error signal is fed into a Propor Integral compensator which produces the output of the current
loop, i.e. the firing angle signal.
In the Drive, the error signal is created in two different forms:
1.
The
average
error is computed as the difference between demand and average value of feedback and fed into the Integral part of the P + I
algorithm.
2.
The
instantaneous
error is computed as the difference between demand and instantaneous value of feedback and is fed into the Proportional part of
the P + I algorithm. This gives higher transient performance since it does not contain any time lag, unlike the average which has a built-in lag of 1/6
of mains cycle. However, the average is the true measurement of torque which is the objective of the current control and this is not affected by the
small time lag in achieving zero steady-state error.
The firing angle signal is translated into a certain time delay from the mains zero cross point (obtained via a Phase-Lock-Loop) and this results in a
firing command being issued to the thyristor stack every 1/6 of a mains cycle in steady-state.
Some special features of the current controller are discussed separately below.
Adaptive Current Control
The gain of a thyristor 6-pulse converter (voltage-time area over firing angle) drops dramatically at discontinuous values of armature current.
Therefore a gain boost is required in the current controller to compensate for that.
In the Drive, this is handled by an adaptive algorithm which allows the current to follow the demand in one step (firing) within the discontinuous
region of operation.
Back EMF (BEMF) Estimate
With the motor at standstill, the firing angle for zero current is 120 degrees. When the motor is rotating at different speeds the firing angle for zero
current follows a cosine locus.
It is of paramount importance to track this locus as close as possible throughout the speed range if the current loop bandwidth is to be maintained at its
highest possible level during current reversals from master to slave bridge and visa-versa.
There are two reasons for the loss of bandwidth at current reversals:
MMI Menu Map
1
SETUP PARAMETERS
2
CURRENT LOOP
I
DMD
ISOLATE
Summary of Contents for 590+ DRV
Page 1: ...590 DRV Frame 1 2 3 4 5 6 7 HA470388U003 Issue 2 Product Manual...
Page 2: ......
Page 14: ......
Page 16: ...DC590 DRV DC Digital Drive...
Page 20: ...DC590 DRV Series DC Digital Drive...
Page 38: ...DC590 DRV Series DC Digital Drive...
Page 126: ...3 88 Installing the Drive DC590 DRV Series DC Digital Drive...
Page 128: ...DC590 DRV Series DC Digital Drive...
Page 158: ...DC590 DRV Series DC Digital Drive...
Page 166: ...5 8 Control Loops DC590 DRV Series DC Digital Drive...
Page 168: ...DC590 DRV Series DC Digital Drive...
Page 194: ...DC590 DRV Series DC Digital Drive...
Page 226: ...DC590 DRV Series DC Digital Drive...
Page 244: ...DC590 DRV Series DC Digital Drive...
Page 274: ...A 30 Serial Communications DC590 DRV Series DC Digital Drive...
Page 276: ...DC590 DRV Series DC Digital Drive...
Page 292: ...B 16 Certification DC590 DRV Series DC Digital Drive...
Page 294: ...DC590 DRV Series DC Digital Drive...
Page 330: ...C 36 Parameter Specification Tables DC590 DRV Series DC Digital Drive...
Page 348: ......
Page 368: ...D 20 Programming DC590 DRV Series DC Digital Drive Functional Description...
Page 496: ...D 148 Programming DC590 DRV Series DC Digital Drive Programming Block Diagram Sheet 1...
Page 497: ...Programming D 149 DC590 DRV Series DC Digital Drive Programming Block Diagram Sheet 2...
Page 498: ...D 150 Programming DC590 DRV Series DC Digital Drive Programming Block Diagram Sheet 3...
Page 499: ...Programming D 151 DC590 DRV Series DC Digital Drive Programming Block Diagram Sheet 4...
Page 504: ...D 156 Programming DC590 DRV Series DC Digital Drive...
Page 506: ...DC590 DRV Series DC Digital Drive...
Page 543: ......