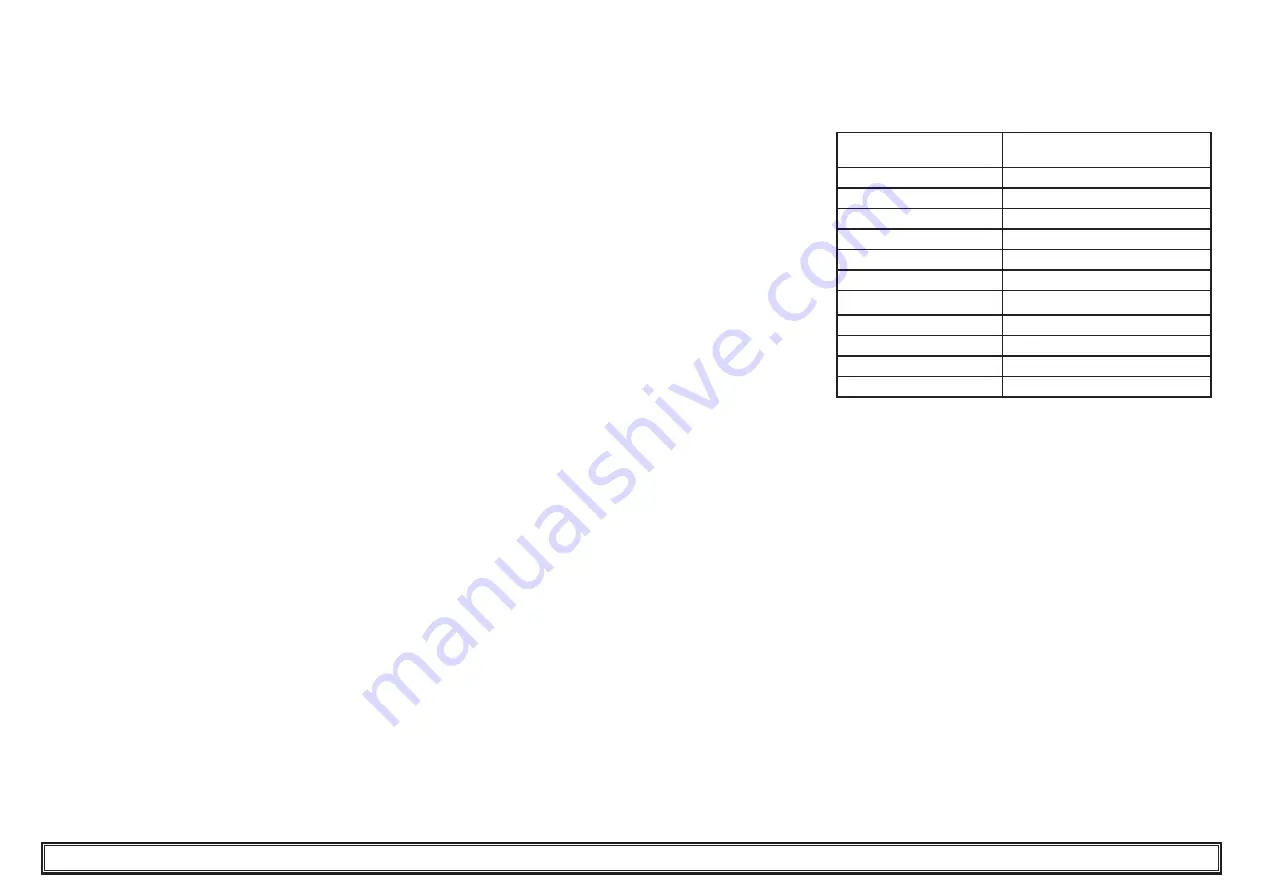
English
7/8
ICE310-360
5 Maintenance
a) The machine is designed and built to guarantee continuous opera-
tion; however, the life of its components depends on the mainte-
nance performed.
b) Z When requesting assistance or spare parts, identify the machine
(model and serial number) by reading the data plate located on the
unit.
c) Circuits containing 5t < xx < 50t of CO2 are checked to identify
leaks at least once a year.
Circuits containing 50t < xx < 500t di CO2 are checked to identify
leaks at least once every six months. ((EU) No. 517/2014 art. 4.3.a,
4.3.b).
d) For machines containing 5t CO2 ore more, the operator must keep a
record stating the quantity and type of refrigerant used, an quantities
added and that recovered during maintenance operations, repairs
and fi nal disposal ((EU) No. 517/2014 art. 6). .An example of this
record sheet can be downloaded from the site: www.polewr.com.
5.1 General instructions
!
Before performing any maintenance, make sure the power to the
refrigerator is disconnected.
Y
Always use the Manufacturer’s original spare parts: otherwise the
Manufacturer is relieved of all liability regarding machine malfunction-
ing.
Y
In case of refrigerant leakage, contact qualifi ed and authorized
personnel.
Y
The Schrader valve must only be used in case of machine mal-
function: otherwise any damage caused by incorrect refrigerant charg-
ing will not be covered by the warranty.
5.2 Preventive maintenance
To guarantee lasting maximum chiller effi ciency and reliability, carry out:
Z
every 6 months -
clean the condenser fi ns and make sure com-
pressor electrical absorption is within the dataplate values;
Z
Maintenance
(par.7.7)
a) kit for maintenance;
b) service kit;
c) individual spare parts.
5.3 Refrigerant
Z
Charging: any damage caused by incorrect charging carried out
by unauthorized personnel will not be covered by the warranty.
Y
The equipment contains fl uorinated greenhouse gases.
At normal temperature and pressure, the R407C refrigerant is a colour-
less gas classifi ed in SAFETY GROUP A1 - EN378 (group 2 fl uid ac-
cording to Directive PED 2014/68/EU);
GWP (Global Warming Potential) = 1774.
!
In case of refrigerant leakage, air the room.
5.4 Dismantling
The refrigerant and the lubricating oil contained in the circuit must be
recovered in conformity with current local environmental regulations.
The refrigerant fl uid is recovered before fi nal scrapping of the equip-
ment ((EU) No. 517/2014 art.8).
%
Recycling
Disposal
frame and panels
steel/epoxy resin polyester
tank
aluminium/copper/steel
pipes/collectors
copper/aluminium/carbon steel
pipe insulation
NBR rubber
compressor
steel/copper/aluminium/oil
condensator
steel/copper/aluminium
pump
steel/cast iron/brass
fan
aluminium
refrigerant
R407C (HFC)
valve
brass/copper
electrical cable
copper/PVC
Summary of Contents for Hyperchill ICE310
Page 2: ......
Page 58: ...Suomi 8 8 ICE310 360 ...
Page 98: ...Česky 8 8 ICE310 360 ...
Page 140: ...7 8 Circuit diagram ICE310 360 16 ICE310 360 P Tank A1 ...
Page 141: ...7 9 Wiring diagram ICE310 360 17 ICE310 360 Sheet 1 of 11 ...
Page 142: ...7 9 Wiring diagram ICE310 360 18 ICE310 360 Sheet 2 of 11 ...
Page 143: ...7 9 Wiring diagram ICE310 360 19 ICE310 360 Sheet 3 of 11 ...
Page 144: ...7 9 Wiring diagram ICE310 360 20 ICE310 360 Sheet 4 of 11 ...
Page 145: ...7 9 Wiring diagram ICE310 360 21 ICE310 360 Sheet 5 of 11 ...
Page 146: ...7 9 Wiring diagram ICE310 360 22 ICE310 360 Sheet 6 of 11 ...
Page 147: ...7 9 Wiring diagram ICE310 360 23 ICE310 360 Sheet 7 of 11 ...
Page 148: ...7 9 Wiring diagram ICE310 360 24 ICE310 360 Sheet 8 of 11 ...
Page 149: ...7 9 Wiring diagram ICE310 360 25 ICE310 360 Sheet 9 of 11 ...
Page 150: ...7 9 Wiring diagram ICE310 360 26 ICE310 360 Sheet 10 of 11 ...
Page 151: ...7 9 Wiring diagram ICE310 360 27 ICE310 360 Sheet 11 of 11 ...
Page 152: ......
Page 153: ......