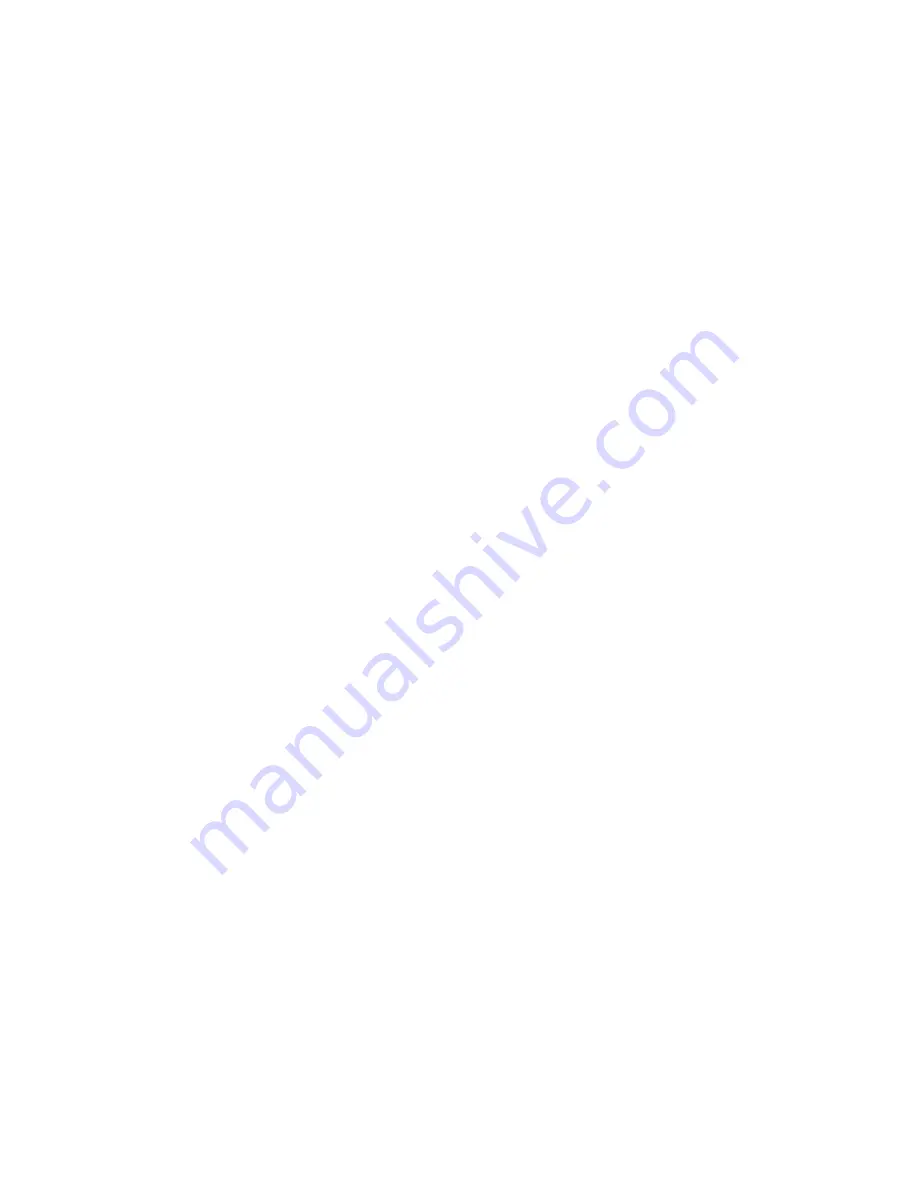
CHAPTER 6
CORRECTIVE MAINTENANCE
6-1 INTRODUCTION.
This chapter provides repair procedures for the
Pakhammer.
NOTE: WITHIN ONE YEAR OF THE
PURCHASE DATE, REPAIRS MUST BE MADE BY
THE MANUFACTURER OR WARRANTY (PAGE 7-4)
IS VOID.
If it is determined from table 5-1 that
repairs are required, proceed with the following:
6-2 ADJUSTMENTS.
The only adjustment of the Pakhammer is the
assembled distance, 5.120" (130 mm), between the
front of trigger link (11, figure 6-1) and the back of
trigger valve plunger (8). This adjustment is made only
if operation commences with either no "triggering" or
when the Pakhammer is "just barely triggered". Screw
the trigger link into the trigger valve plunger until the
5.120” (130 mm) dimension is achieved. A minimum
amount of trigger lever (4) play should be present
before operation commences.
6-3 ALIGNMENT.
No alignment is required on any part of the
Pakhammer.
6-4 PAKHAMMER REPAIR.
6-4.1 The following procedures describe one method
of complete disassembly of the Pakhammer. Work in
a clean area and place all disassembled parts on clean
shop wipes. All parts subjected to any air passage
should exhibit a film of lubricant. If clamping is
required, use pads to prevent
scratching/scoring/abrading the clamped parts.
When repairing the Pakhammer, remove only those
parts determined to be broken, cracked, deformed or
otherwise damaged. During inspection, parts
exhibiting any damage characteristics referenced
herein should be replaced with the exception of minor
thread damage repair, apply only the procedural
steps that are applicable to the work to be performed.
Prior to disassembly of the Pakhammer, unscrew the
oiler hose assembly from the Pakhammer. Refer to
figure 6-1 and proceed as follows:
6-4.2 DISASSEMBLY OF TOOL RETAINER
ASSEMBLY.
a. Install retainer service tool (15) into retainer body
(21) by pulling back release ring (17), inserting
the retainer service tool with the ball recesses
entering the retainer body, and then release the
release ring. Rotate the retainer service tool until
balls (18) engage the recesses locking the
retainer service tool in the retainer body.
NOTE
A thread sealant has been applied to retainer body (21)
and set screw (38) and significant force is required
for their removal. Heating the front of cylinder (47) with
a heat gun (do not use a torch) will soften the thread
sealant and facilitate removal of the retainer body
and set screw.
b. Remove set screw (38) and (43). Insert a tool
bit through the hole in retainer service tool and
unscrew retainer body (21) from cylinder (47). It
may be necessary to hit the tool bit/rod with a
hammer to turn the retainer body out of the
cylinder.
c. Remove release ring spring (16), release ring
(17) and six balls (18). Front bumper (20)
(Delrin) and front bumper washer (19) (steel)
may adhere to retainer body (21) or they may
remain in cylinder (47) recess. Remove them
and note that the D elrin front bumper must be
positioned between the retainer body and steel
front bumper washer for proper assembly. Also
note that the inside diameter chamfer on the
steel front bumper washer is oriented toward
the rear of the Pakhammer.
d. Inspect release ring (17) inside diameter that
engages balls (18) for an excessively worn
or peened over condition. This generally
indicates operation of the Pakhammer without
exerting any force on the tool bit. Inspect the
ball holes in retainer body (21) for enlargement
and distortion. Inspect balls (18) for evidence
of scoring, chipping, scratching or other similar
damage. Check release ring spring (16) for
distortion and a permanent set (loss of
compression).
6-4.3 REMOVAL AND DISASSEMBLY OF HANDLE
ASSEMBLY.
NOTE
A thread sealant has been applied to all fasteners
necessitating the use of hexagon socket keys that are
not worn and the application of significant force for their
removal.
a. Unscrew two hexagon socket screws (1)
securing the handle assembly to cylinder (47).
b. Drive out both spring pins (3 and 39) securing
trigger lever (4) with pin punch and remove from
handle (12).
6-1