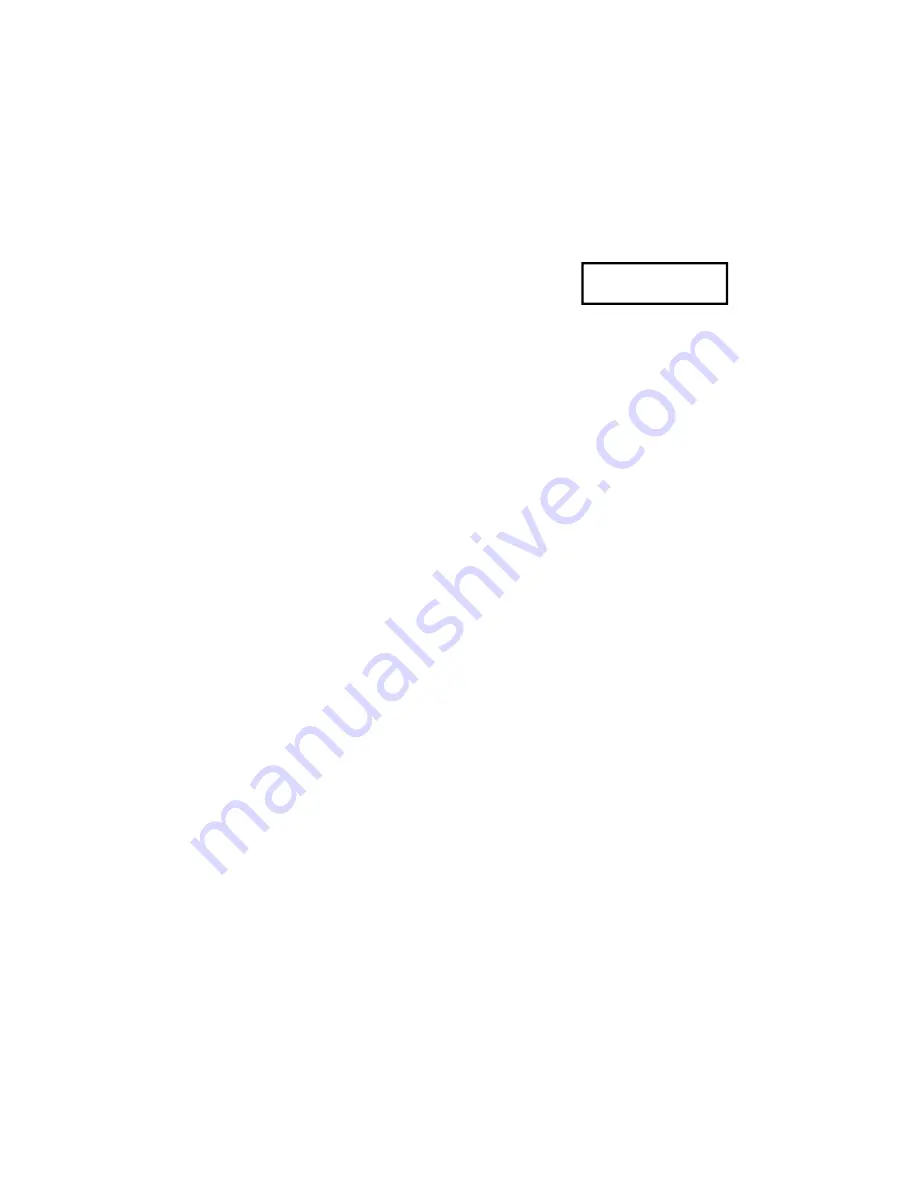
6
‐
46
‐
466 6666 6666
6-4.5
REMOVAL AND DISASSEMBLY OF PISTON
ASSEMBLY.
a. Pull the piston assembly (33 through 36) out of
cylinder (47). Inspect the [piston rod (33) for
scoring along its length and distortion,
fracturing and other similar damage at its tip.
b. Note
the
location of wear ring (34), U-cup seal
(35), and urethane piston bumper (36) relative
to each other and the orientation of the U-cup
seal to facilitate proper reassembly. Discard
the seal only if a replacement is available. If
a replacement is not available and the old
seal is worn, cut or otherwise damaged, it
may result in air leakage and diminished
operation but must be reused until a
replacement becomes available. If the seal
is sufficiently damaged, it may result in
excessive leakage around the piston rod and
a complete lack of operation. Inspect the
urethane piston bumper for crazing,
excessive wear, fracturing and other similar
damage.
6-4.6 DISASSEMBLY
OF
CYLINDER.
a. Pull
pilot
tube
(43)
and
o-ring
seal
(44)
out
of
cylinder (47). Check that the pilot tube is not
internally obstructed. Discard the seal only if
a replacement is available. If a replacement
is not available and the old seal is worn, cut
or otherwise damaged, it may result in air
leakage from between valve body (31) and
cylinder (47) but must be reused until a
replacement becomes available. Handle
dowel pin (14) need not be removed unless
visually damaged. Setscrew (48) should not
be removed from the cylinder unless air
leakage
is noted from around
the
setscrew. Inspect internal threads in the
cylinder for damage such as battered,
stripped or cross threads. Minor thread
damage can be corrected with a
threading tap. Inspect the cylinder bore
for scoring along its length.
b. Pull springs (40) and spring guide bushing (41)
out of the cylinder. Do not remove piston rod
bushing (42) unless it is damaged. If removed,
note orientation of the piston rod bushing to
facilitate its proper reassembly. Inspect the
springs for distortion and a loss of
compression. If both are not the same length
and at least 7-1/8” (181 mm) long, replace both
springs and the spring guide bushing as a set.
Inspect the spring guide bushing for excessive
wear, flare out, fracturing or other similar
damage.
6-4
c. Do not remove labels (45, 45A, 46, or 50) from
cylinder (47) unless their replacement is
required. If required, the labels may be peeled
off the cylinder. Be sure to clean off all
adhesive residue.
6-4.7 CLEANING.
Dry
cleaning solvent (P-D-680 Safety or
Stoddard's Solvent) is potentially dangerous.
Avoid repeated or prolonged breathing of vapors and
skin contact with the liquid. Do not use near an open
flame, arcing equipment or other ignition sources.
Always use eye protection and protective clothing.
Serious injury could occur if compressed air is
directed against the skin. Do not use compressed air
unless the pressure is/has been reduced to 30 psi
(2.07 bar) or less. When working with compressed
air, always use chip guards, eye protection and other
protective equipment.
a. No
special
cleaning
procedures
are
required
to clean the disassembled parts of the
Pakhammer. Cleaning may be accomplished
by washing in a hot soap and water solution.
Rinse the parts thoroughly with hot clean
water and dry immediately with a clean cloth,
shop wipes or compressed air. Exercise care
not to scratch any polished surface.
b. Stubborn
deposits
may
be
removed
with
a
dry
cleaning solvent (specification P-D-680,
safety or Stoddard’s Solvent) or equal and a
soft bristle of wire brush. Clean thread sealant
off part(s) by heating the part(s) with a heat
gun (not a torch), applying solvent and
scrubbing with a soft bristle of wire brush.
c. After cleaning, apply a thin coating of Marvel
®, Air Tool Oil, Turtle Wax, P.O. Box 247,
Westmont, IL 60559 (Paratech PN 550291) to
all internal surfaces and internal parts except
seals (2, 6, 7, 10, 27, 29, and 44), balls (18),
and piston springs (40). Grease all seals and
balls with Chemplex 710 Silicone Grease,
FUCHS Lubricants Company, Harvey IL.
60426.
WARNING