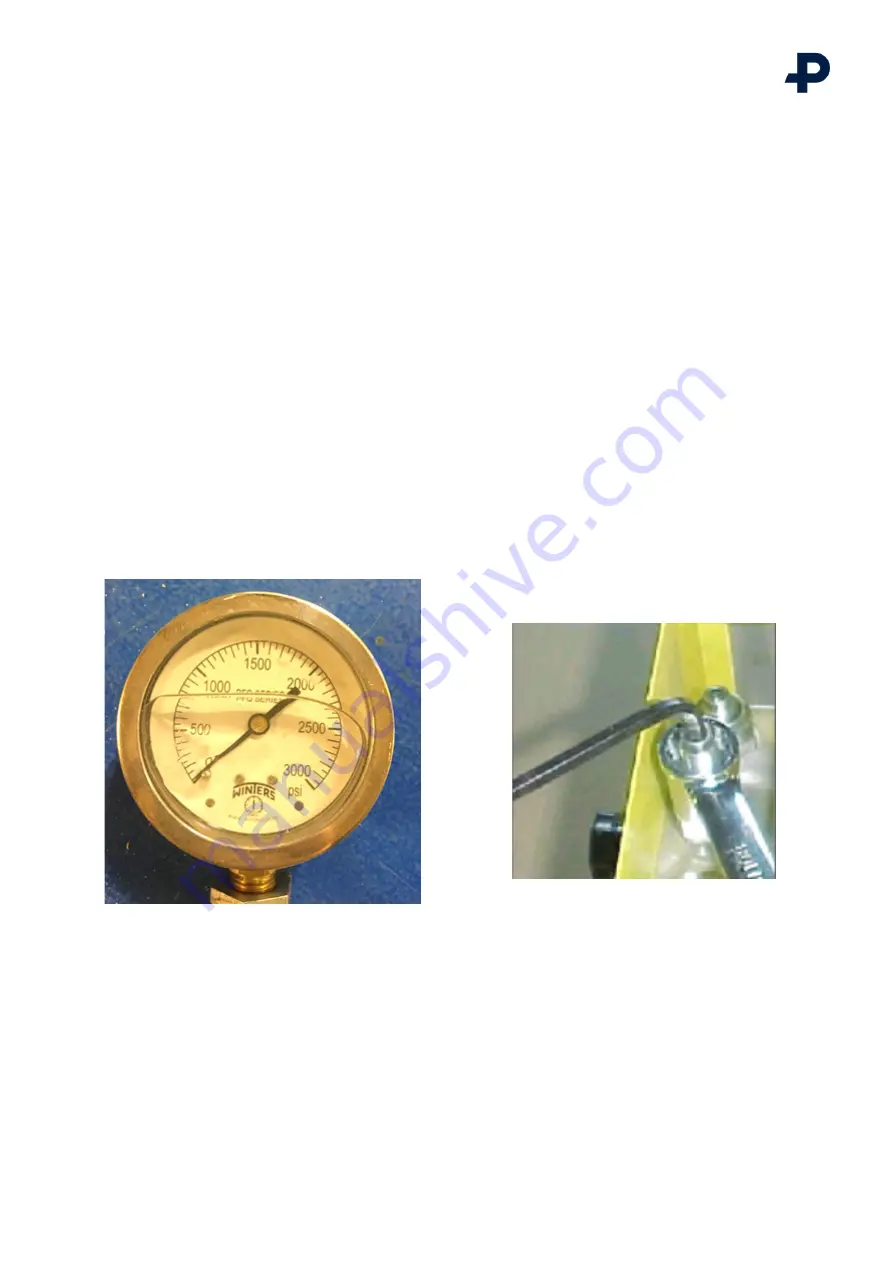
8. Relief pressure calibration
With flow and pressure test gauge connected to the 10 GPM port, close the needle valve, and turn on top control
valve noting the pressure shown on the gauge. Proper relief setting will be 2000-2100 PSI. (Turn valve off after
checking pressure)
If you need to adjust the 00139 pressure relief valve. Loosen the jam nut on the 00139 relief valve with a 3/4”
deep socket. (Or similar tool) turn the adjustment screw clockwise to increase relief setting. (A 1/4” hex key will be
needed for adjustment) turn top valve on noting the pressure on the gauge. After relief pressure has been reached,
tighten the jam nut on the 00139 relief valve being careful not to turn pressure adjustment screw. Turn the valve off
after setting pressure.
Fig 5.
Fig 6.
14 av 34
OPERATION AND MAINTENANCE MANUAL I ENG_OMM_ELECTRIC_POWER_UNIT_P01 I 30th November 2021
@Pandrol 2021