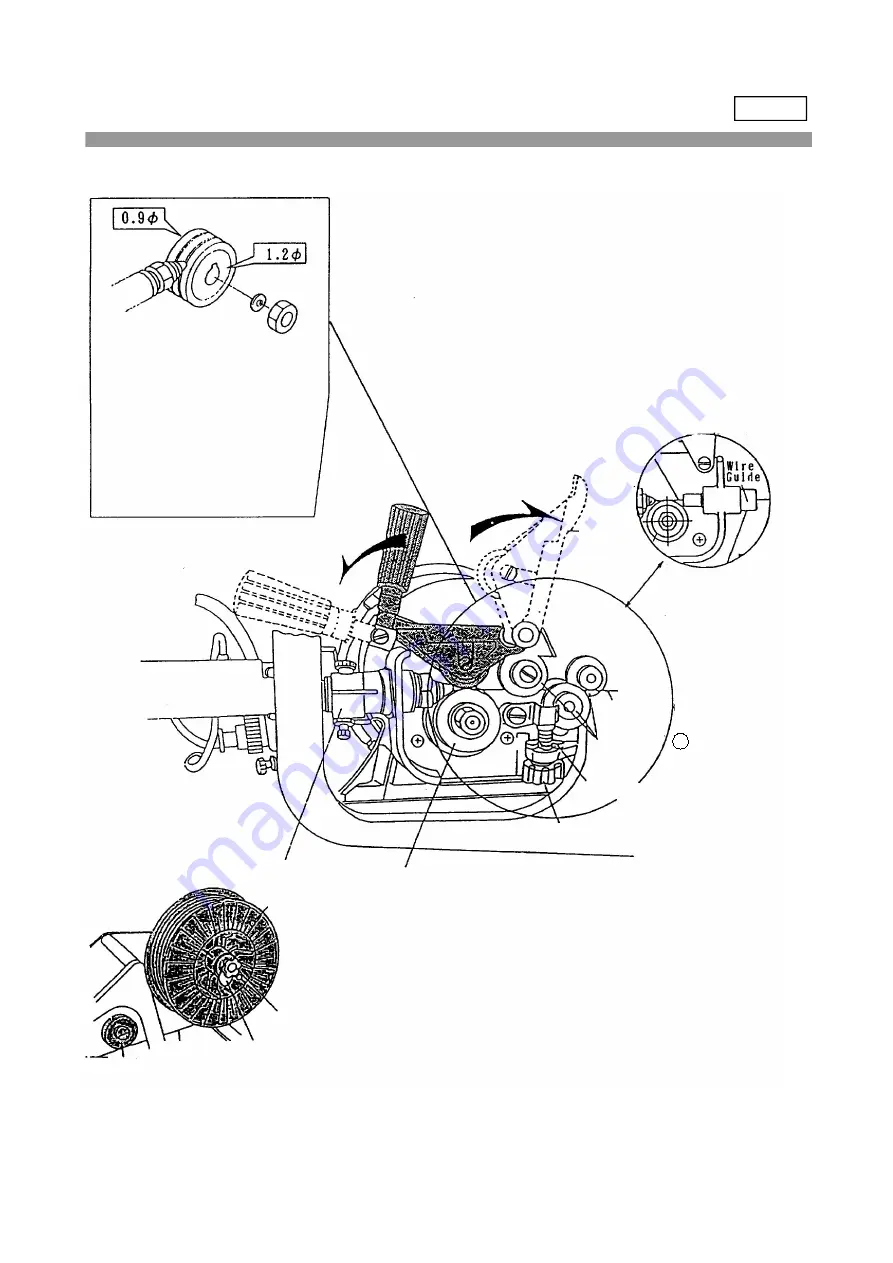
13
CHECKS AND PREFARATIONS PRIOR TO OPERATION
Attaching the welding wire
Attach a feed roller in
the
direction
which
allows you to see the
same numeral as the wire
diameter
used.
(The
figure above shows an
example
of
attaching
“
l.2
”
of the
0.9/1.2
feed roller)
⑩Put back a pressure arm and pressure nut in
that order.
Pressure
Nut
②Shaft
down
③Lift up.
Pressure
Arm
④Loosen a lock nut
a n d c o r r e c t i o n
adjusting bolt in
tha t or de r
.
(Not required for
the 200KR2/350KR2)
1
Make sure that the
m o u n t e d
f e e d
roller conforms to
a diameter of the
w e l d i n g w i r e .
Wire
Correction
Roller
Lock nut
Correction Adjusting Bolt
CC Fixture
Wire Stopper
Hole
Feed Roller
Knob Screw
Spool Clamping Washer
Wire
Correction Roller
⑤ Loosen a knob screw to remove a spool clamping
washer.
⑥Attach the welding wire to the spool fitting. (In the
clockwise direction of the wire spool)
⑦Put back the spool clamping washer and tighten the
knob screw.
⑧Remove a wire stopper from the outer edge of the wire
spool.
(Be careful of the wire jumping up of getting loose)
(11)Turn the pressure nut to make a pressurization
force
commensurate with a diameter of the welding wire.
⑨Pull out the welding wire. Insert it
into the CC fixture, putting it
through the correction rollers
(Wire guide for the 200KR2/350KR2)
BASICS