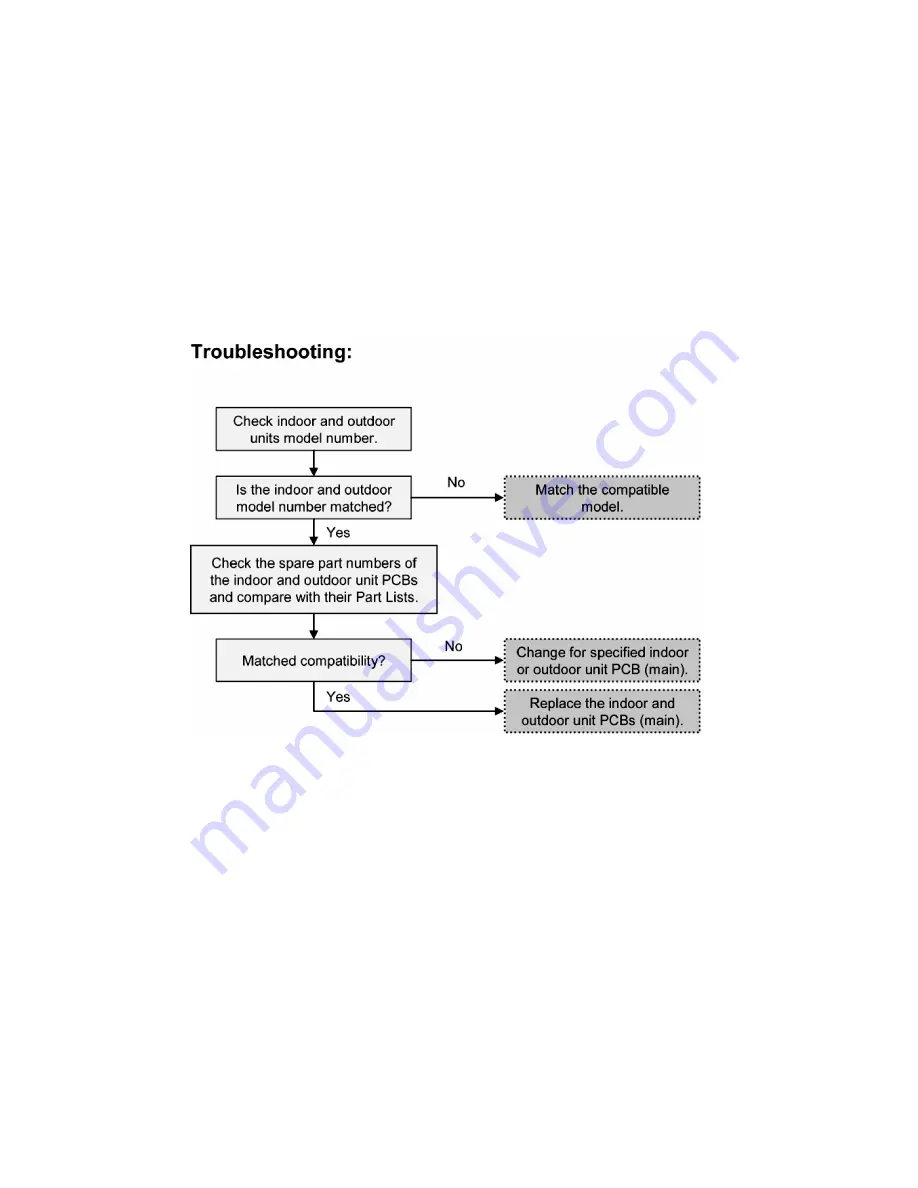
86
17.5. Self-diagnosis Method
17.5.1. Connection Capability Rank Abnormality (H12)
Malfunction Decision Conditions:
During startup operation of cooling and heating, the capability rank of indoor checked by the outdoor is used to determine
connection capability rank abnormality.
Malfunction Caused:
1. Wrong model interconnected.
2. Wrong indoor unit or outdoor unit PCB (main) used.
3. Faulty indoor unit or outdoor unit PCB (main).
Abnormality Judgment:
Continue for 90 seconds.
Summary of Contents for WH-SDF07C3E5
Page 16: ...16 4 Location of Controls and Components 4 1 Indoor Unit 4 1 1 Location of Control ...
Page 17: ...17 ...
Page 18: ...18 ...
Page 19: ...19 4 1 2 Weekly Timer Setting ...
Page 20: ...20 4 1 3 Setting Up The Special Functions ...
Page 21: ...21 4 1 4 Main Components 4 2 Outdoor Unit ...
Page 22: ...22 5 Dimensions 5 1 Indoor Unit ...
Page 23: ...23 5 2 Outdoor Unit 5 2 1 WH UD07CE5 A WH UD09CE5 A ...
Page 24: ...24 5 2 2 WH UD12CE5 A WH UD14CE5 A WH UD16CE5 A ...
Page 26: ...26 ...
Page 27: ...27 7 Block Diagram 7 1 WH UD07CE5 A WH UD09CE5 A ...
Page 28: ...28 7 2 WH UD12CE5 A WH UD14CE5 A WH UD16CE5 A ...
Page 29: ...29 8 Wiring Connection Diagram 8 1 Indoor Unit 8 1 1 WH SDF07C3E5 WH SDF09C3E5 ...
Page 30: ...30 8 1 2 WH SDF12C6E5 WH SDF14C6E5 WH SDF16C6E5 ...
Page 31: ...31 8 2 Outdoor Unit 8 2 1 WH UD07CE5 A WH UD09CE5 A ...
Page 32: ...32 8 2 2 WH UD12CE5 A WH UD14CE5 A WH UD16CE5 A ...
Page 33: ...33 9 Electronic Circuit Diagram 9 1 Indoor Unit 9 1 1 WH SDF07C3E5 WH SDF09C3E5 ...
Page 34: ...34 9 1 2 WH SDF12C6E5 WH SDF14C6E5 WH SDF16C6E5 ...
Page 35: ...35 9 2 Outdoor Unit 9 2 1 WH UD07CE5 A WH UD09CE5 A ...
Page 36: ...36 9 2 2 WH UD12CE5 A WH UD14CE5 A WH UD16CE5 A ...
Page 37: ...37 10 Printed Circuit Board 10 1 Indoor Unit 10 1 1 Main Printed Circuit Board ...
Page 38: ...38 10 1 2 Solar Printed Circuit Board Optional ...
Page 39: ...39 10 2 Outdoor Unit 10 2 1 WH UD07CE5 A WH UD09CE5 A 10 2 1 1 Main Printed Circuit Board ...
Page 40: ...40 10 2 1 2 Capacitor Printed Circuit Board 10 2 1 3 Noise Filter Printed Circuit Board ...
Page 41: ...41 10 2 2 WH UD12CE5 A WH UD14CE5 A WH UD16CE5 A 10 2 2 1 Main Printed Circuit Board ...
Page 42: ...42 10 2 2 2 Capacitor Printed Circuit Board 10 2 2 3 Noise Filter Printed Circuit Board ...
Page 73: ...73 ...
Page 74: ...74 ...
Page 120: ...120 18 3 To Remove Pressure Gauge 18 4 To Remove Control Panel ...
Page 121: ...121 18 5 To Remove RCCB 18 6 To Remove Transformer and Electronic Controller Board ...
Page 138: ...138 20 2 WH UD07CE5 A WH UD09CE5 A ...
Page 139: ...139 ...
Page 142: ...142 20 3 WH UD12CE5 A WH UD14CE5 A WH UD16CE5 A ...
Page 143: ...143 ...