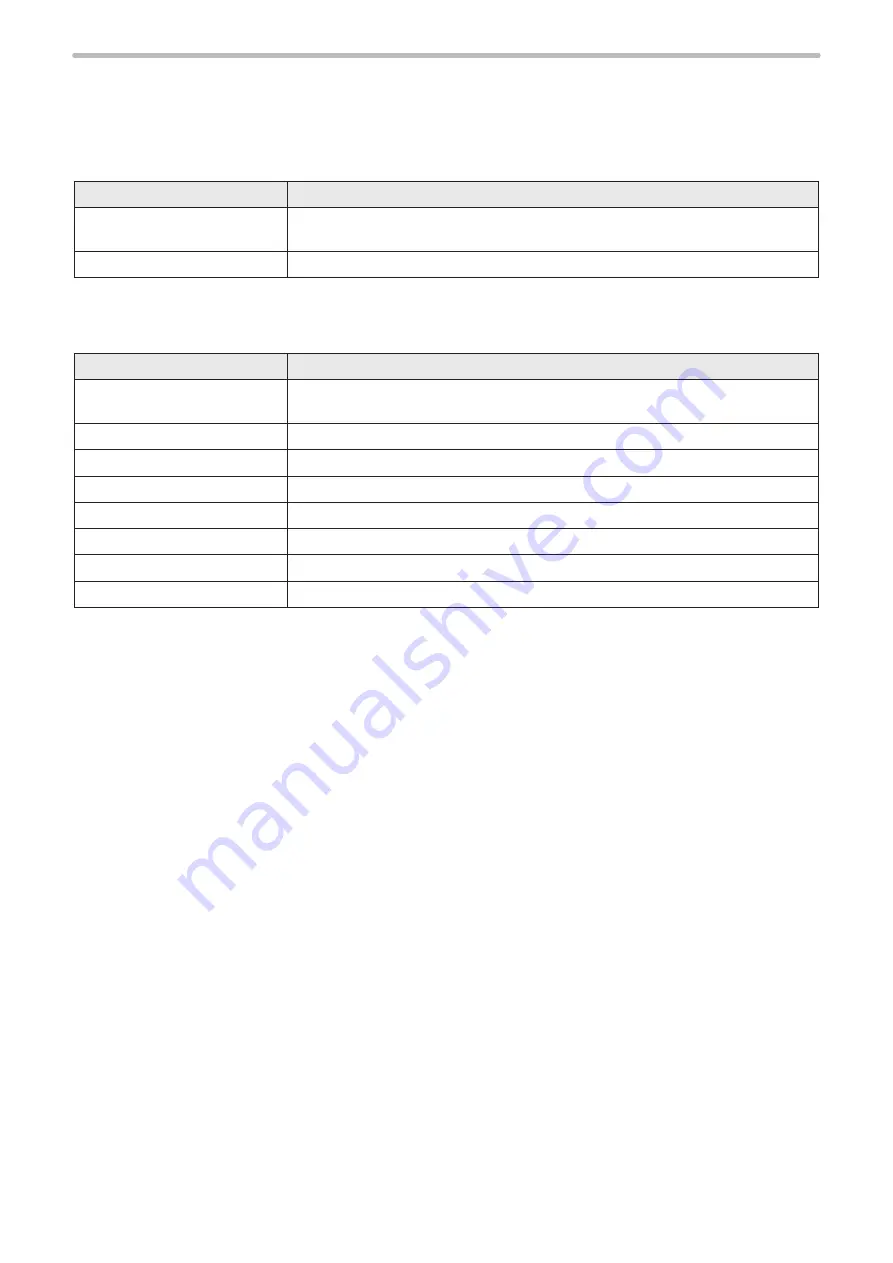
61
2-5-4 Installation of attached software
The following software is stored in the attached CD-ROM “Laser Processing Utility_VL-W1”.
To use these software, install the data in the CD-ROM to the commercially available PC.
Stored data in the CD-ROM
Name of software
Description
Logo Data Conversion Software
Converts the drawing data in DXF/JPEG/BMP/HPGL formats to the laser welding
machine dedicated format “VEC”.
Logo Data Editing Software
Creates and edits the drawing data in VEC format.
Operating environment
Install the attached CD-ROM “Laser Processing Utility_VL-W1” in the following environment.
Item
Installation requirements
OS *1
Microsoft
®
Windows
®
11 Pro 32bit, 64bit
Microsoft
®
Windows
®
10 Pro 32bit, 64bit
Free area on hard disk
100MB or more
CD-ROM drive *2
1 set or more
USB port *3
USB1.1 or later
Memory capacity
1GB or more
CPU
1GHz or more
Display resolution
1024 x 768 pixels or above
Others
Pointing device such as a mouse and character input device such as a keyboard
*1 : OS versions of which Microsoft has ended support are excluded. The CPU type, memory capacity, hard-disk space,
and display function required to operate each OS should be provided in accordance with the recommendation of
Microsoft.
*2 : To install the software on a PC without a CD-ROM drive, copy all CD-ROM data to the PC using external storage
media such as a USB flash drive before installation.
*3 : We do not guarantee the connection of all PC and laser welding machine.
Installation procedures
Set the CD-ROM “Laser Processing Utility_VL-W1” to the PC and the installation will start automatically.
Install “Laser Processing Utility_VL-W1-N” by following the instructions shown on the screen.
If the installation screen does not appear, double-click on following file to start installation.
[CD-ROM]\Setup\setup.exe
ME-VLW1N-SM-1
Summary of Contents for VL-W1-N Series
Page 18: ...1 Product Overview ME VLW1N SM 1...
Page 40: ...2 Laser Welding Machine Installation ME VLW1N SM 1...
Page 64: ...3 Operation Method ME VLW1N SM 1...
Page 82: ...4 External Control Using I O ME VLW1N SM 1...
Page 122: ...5 External Control by Communication Commands ME VLW1N SM 1...
Page 126: ...6 Laser Power Monitoring Function ME VLW1N SM 1...
Page 139: ...7 Maintenance ME VLW1N SM 1...
Page 156: ...Troubleshooting ME VLW1N SM 1...
Page 171: ...Index ME VLW1N SM 1...
Page 174: ...174 MEMO ME VLW1N SM 1...
Page 175: ......