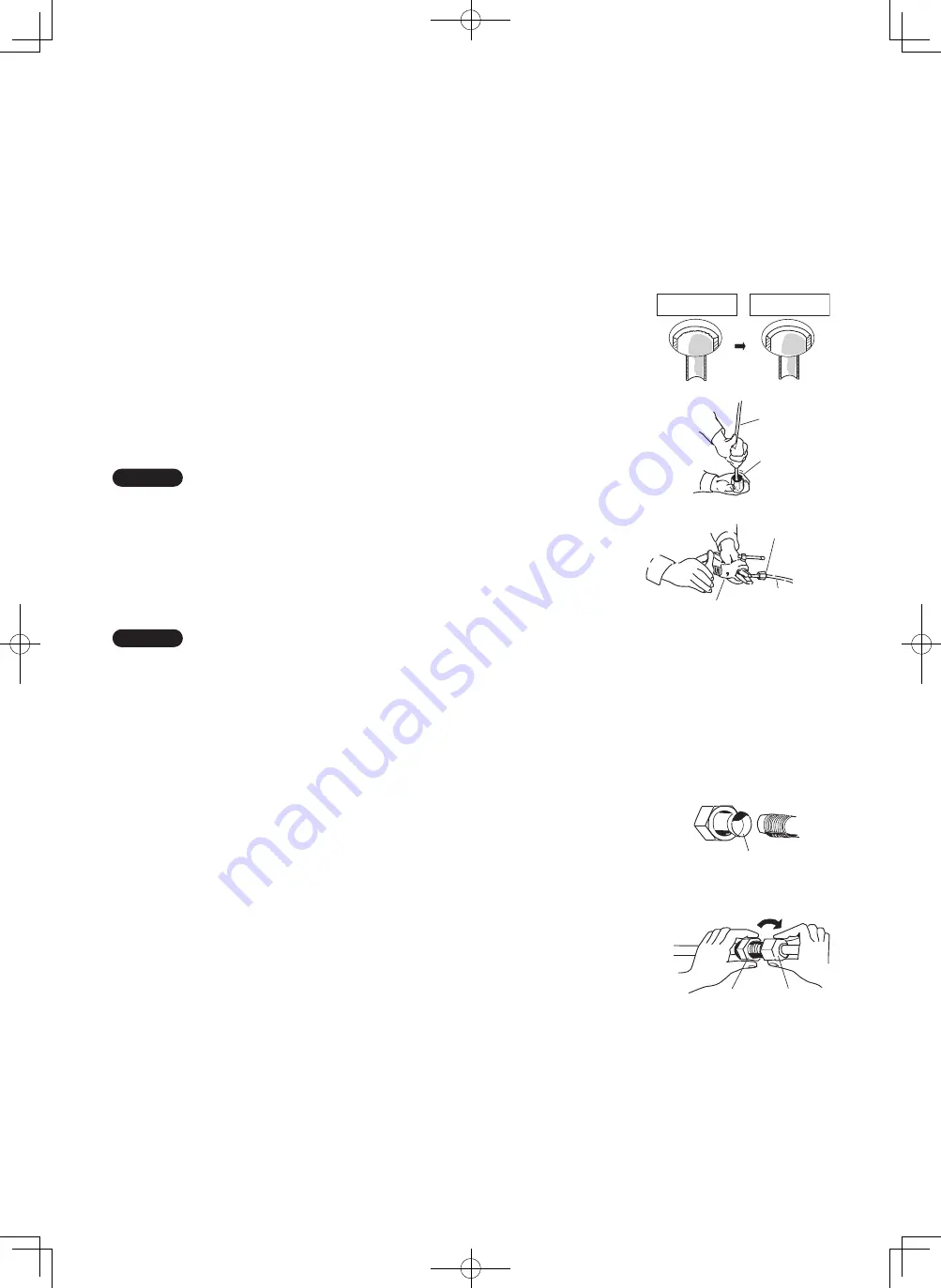
35
5. HOW TO PROCESS TUBING
5-1. Connecting the Refrigerant Tubing
Use of the Flaring Method
Many of conventional split system air conditioners employ the flaring method to connect
refrigerant tubes that run between indoor and outdoor units. In this method, the copper tubes
are flared at each end and connected with flare nuts.
Flaring Procedure with a Flare Tool
(1) Cut the copper tube to the required length with a tube cutter.
It is recommended to cut approx. 30 – 50 cm longer than the
tubing length you estimate.
(2) Remove burrs at each end of the copper tubing with a tube
reamer or a similar tool. This process is important and should
be done carefully to make a good flare. Be sure to keep any
contaminants (moisture, dirt, metal filings, etc.) from entering
the tubing.
N OT E
When reaming, hold the tube end downward and be sure that
no copper scraps fall into the tube.
(3) Remove the flare nut from the unit and be sure to mount it
on the copper tube.
(4) Make a flare at the end of the copper tube with a flare tool.
N OT E
A good flare should have the following characteristics:
●
inside surface is glossy and smooth
●
edge is smooth
●
tapered sides are of uniform length
Caution Before Connecting Tubes Tightly
(1) Apply a sealing cap or water-proof tape to prevent dust or
water from entering the tubes before they are used.
(2) Use a small amount of ether oil (PVE only) to apply
refrigerant lubricant to the inside of the flare nut when
making a flare connection. Pay careful attention to prevent
the ether oil (PVE only) from directly attaching the screw
and resin parts. This is effective for reducing gas leaks.
(3) For proper connection, align the union tube and flare tube
straight with each other, then screw on the flare nut lightly
at first to obtain a smooth match.
●
Adjust the shape of the liquid tube using a tube bender at the
installation site and connect it to the liquid tubing side valve using a
flare.
Flare nut
Copper
tubing
Flare tool
Apply a small amount of
ether oil (PVE only) to the
inside of the flare nut.
Flare nut
Union
Copper
tubing
Reamer
After
Before
Deburring
01_350221_Eng.indb 35
2023/3/17 10:01:14