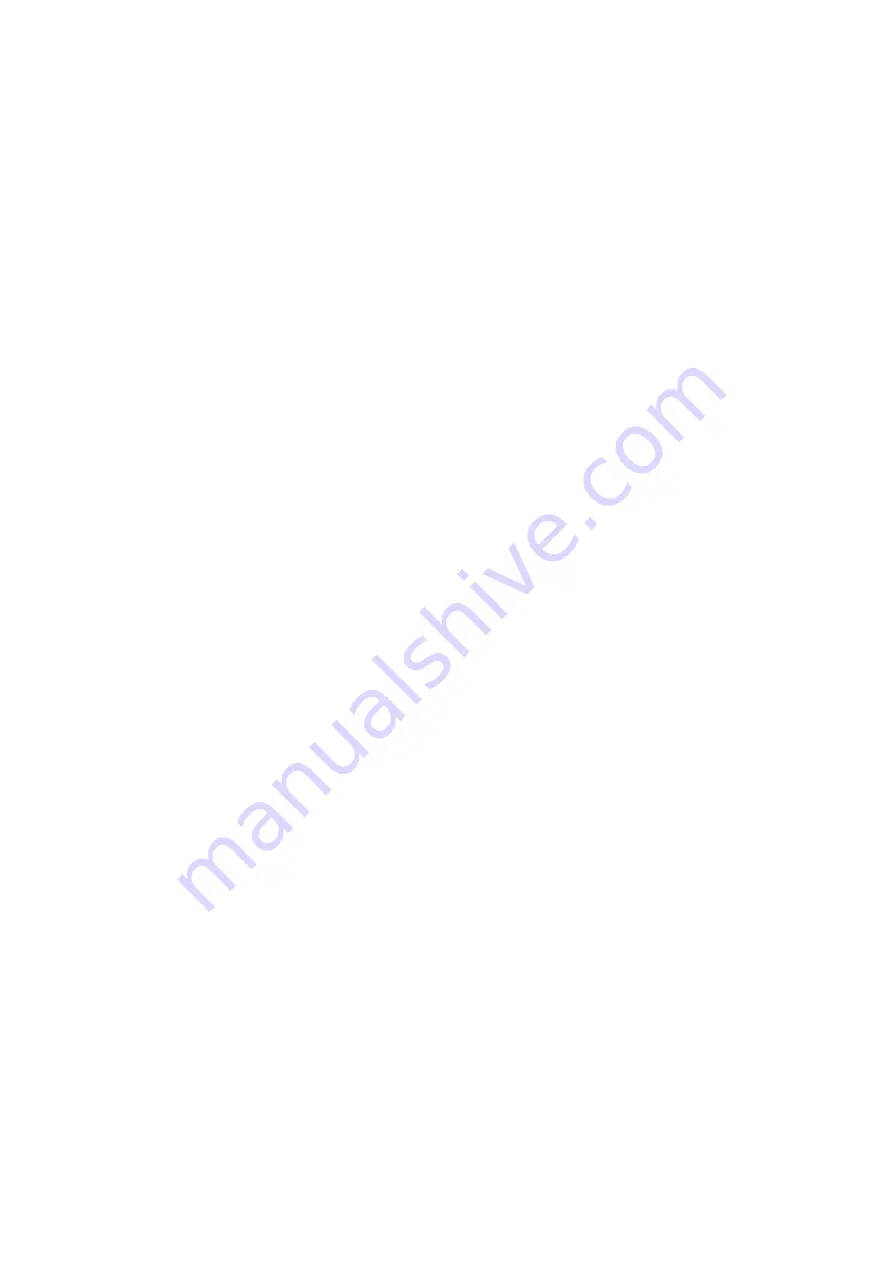
Some semiconductor (solid state) devices can be damaged easily by static electricity. Such
components commonly are called Electrostatically Sensitive (ES) Devices. Examples of typical
ES devices are integrated circuits and some field-effect transistors and semiconductor "chip"
components. The following techniques should be used to help reduce the incidence of
component damage caused by electro static discharge (ESD).
1. Immediately before handling any semiconductor component or
semiconductor-equipped assembly, drain off any ESD on your
body by touching a known earth ground. Alternatively, obtain and
wear a commercially available discharging ESD wrist strap, which
should be removed for potential shock reasons prior to applying
power to the unit under test.
2. After removing an electrical assembly equipped with ES devices,
place the assembly on a conductive surface such as aluminum
foil, to prevent electrostatic charge buildup or exposure of the
assembly.
3. Use only a grounded-tip soldering iron to solder or unsolder ES
devices.
4. Use only an antistatic solder removal device. Some solder
removal devices not classified as "antistatic (ESD protected)" can
generate electrical charge sufficient to damage ES devices.
5. Do not use freon-propelled chemicals. These can generate
electrical charges sufficient to damage ES devices.
6. Do not remove a replacement ES device from its protective
package until immediately before you are ready to install it. (Most
replacement ES devices are packaged with leads electrically
shorted together by conductive foam, aluminum foil or
comparable conductive material).
7. Immediately before removing the protective material from the
leads of a replacement ES device, touch the protective material to
the chassis or circuit assembly into which the device will be
installed.
CAUTION :
Be sure no power is applied to the chassis or circuit, and observe
all other safety precautions.
8. Minimize bodily motions when handling unpackaged replacement
ES devices. (Otherwise harmless motion such as the brushing
4
Summary of Contents for PalmSight PV-L750
Page 7: ...5 1 2 INTERCONNECTION OF EXTENSION CABLES Fig 1 2 7 ...
Page 12: ...12 ...
Page 13: ...13 ...
Page 14: ...14 ...
Page 15: ...15 ...
Page 16: ...5 1 5 DESCRIPTION OF EMERGENCY INDICATIONS 16 ...
Page 27: ...5 2 IC TRANSISTOR AND CHIP PART INFORMATION 6 DISASSEMBLY ASSEMBLY PROCEDURES 27 ...
Page 28: ...6 1 CABINET SECTION 6 1 1 Disassembly Flowchart 6 1 2 Main Parts Portion 28 ...
Page 30: ...6 1 2 2 EVR Cover Side Case L Unit Fig D3 30 ...
Page 31: ...6 1 2 3 Sensor Shield Case Lens Unit Fig D4 31 ...
Page 32: ...6 1 2 4 Main C B A Fig D5 6 1 2 5 VCR Mechanism Chassis Ass y Side Case R Unit Fig D6 32 ...
Page 33: ...6 1 3 LCD PORTION 6 1 3 1 Cassette Cover Unit Fig D7 1 33 ...
Page 34: ...6 1 3 2 Relay C B A Cassette Frame Fig D7 2 34 ...
Page 36: ...6 1 3 6 LCD Lamp Unit Fig D7 6 36 ...
Page 37: ...6 1 4 SIDE CASE L PORTION 6 1 4 1 EVF Unit Color EVF Unit Fig D8 1 37 ...
Page 38: ...6 1 4 2 Side L FPC Unit Fig D8 2 38 ...
Page 39: ...6 1 4 3 PC Jack C B A TV Tuner Jack C B A Model D Fig D8 3 6 1 5 EVF PORTION Model A C D 39 ...
Page 41: ...6 1 6 COLOR EVF PORTION Model B 41 ...
Page 44: ...6 1 7 1 CCD C B A Filter Rubber Optical Filter Fig D11 1 Fig D11 2 44 ...
Page 45: ...6 1 8 LENS PORTION B 6 1 8 1 Lens Piece Unit MF VR Unit Fig D12 1 45 ...
Page 46: ...6 1 8 2 Focus Motor Unit Zoom Motor Unit Fig D12 2 6 1 9 SIDE CASE R PORTION 46 ...
Page 50: ...6 2 2 Inner Parts Location 6 2 2 1 TOP VIEW Fig DM1 1 50 ...
Page 53: ...Fig DM3 2 53 ...
Page 54: ...6 2 5 Cylinder Ass y Fig DM4 1 1 54 ...
Page 55: ...Fig DM4 1 2 55 ...
Page 56: ...6 2 6 Upper Cylinder Unit Cylinder Head Amp F P C Bugle Chip Fig DM4 2 Fig DM4 3 56 ...
Page 57: ...6 2 7 P C B Angle Fig DM5 57 ...
Page 58: ...6 2 8 Mechanism F P C Unit Fig DM6 1 58 ...
Page 59: ...Fig DM6 2 59 ...
Page 60: ...6 2 9 Tension Unit Reel Table Unit Fig DM7 1 60 ...
Page 61: ...Fig DM7 2 61 ...
Page 62: ...6 2 10 Rev Clutch Fig DM8 62 ...
Page 63: ...6 2 11 Take Gear Rev Brake Arm Unit Fig DM9 1 Fig DM9 2 63 ...
Page 64: ...6 2 12 A C Head Unit Fig DM10 64 ...
Page 65: ...6 2 13 Capstan Belt Fig DM11 65 ...
Page 66: ...6 2 14 Capstan Unit Fig DM12 66 ...
Page 67: ...6 2 15 Idle Arm Unit Fig DM13 67 ...
Page 68: ...6 2 16 Mechanism Support Angle Fig DM14 68 ...
Page 69: ...6 2 17 Reduction Gear B Fig DM15 6 2 18 Reduction Gear A Reduction Gear Unit Fig DM16 69 ...
Page 70: ...6 2 19 Pinch Arm Unit Opener P5 Arm Unit Fig DM17 1 Fig DM17 2 70 ...
Page 71: ...6 2 20 Takeup Post Unit Supply Post Unit Fig DM18 1 71 ...
Page 72: ...Fig DM18 2 72 ...
Page 73: ...6 2 21 Impedance Roller Unit Loading Base Unit Fig DM19 1 73 ...
Page 74: ...Fig DM19 2 74 ...
Page 75: ...6 2 22 Takeup Loading Arm Unit Fig DM20 75 ...
Page 76: ...6 2 23 Supply Loading Arm Unit Fig DM21 1 76 ...
Page 77: ...Fig DM21 2 77 ...
Page 78: ...Fig DM21 3 78 ...
Page 79: ...6 2 24 Loading Motor Unit Main Cam Unit Pinch Toggle Fig DM22 79 ...
Page 80: ...7 ADJUSTMENT PROCEDURES 7 1 SERVICE FIXTURES TOOLS 80 ...
Page 89: ...7 3 2 INITIAL GUIDELINE 89 ...
Page 103: ...11 2 CAMERA AND FRAME SECTION 103 ...
Page 104: ...104 ...
Page 105: ...105 ...
Page 106: ...11 3 FRAME AND LCD SECTION 106 ...
Page 107: ...107 ...
Page 108: ...108 ...
Page 109: ...11 4 EVF SECTION A C D 109 ...
Page 110: ...11 5 COLOR EVF SECTION B 110 ...
Page 111: ...11 6 PACKING PARTS AND ACCESSORIES SECTION 111 ...
Page 136: ... C D 136 ...