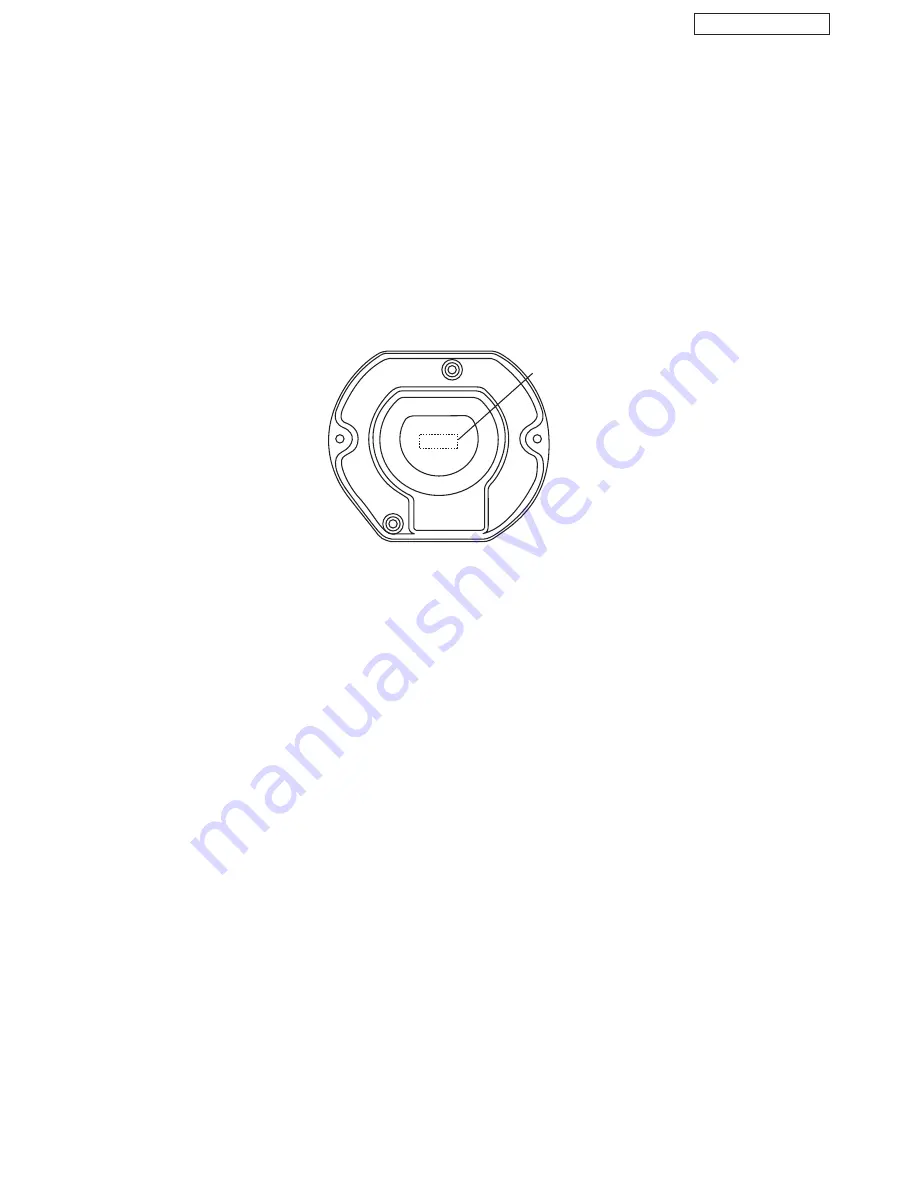
- 17 -
NC-TWS30
2.25. Recheck
After assembly please recheck water leak, insulation resistance and operation, those are usual or unusual.
INSULATION RESISTER
: Measure by 500VDC insulation meter, the result should be more than 2 MΩ.
(Measure between 2 pins of plug and screw).
INSULATION RESISTANCE : Should stand at 1000VAC in 1min. (Measure Location is same as INSULATION
RESISTER).
CURRENT CHECK
: Thermo pot performance test mode (P.2) and operation is usual or unusual.
3 . Production No. Position
Production No. is located at Bottom Plate.
Production Date
4. Body Efficiency Check
Caution
For this test, please careful hot water.
Amount of Pouring-Out Water
Checking
1. Pour water into the Container and change to boiling state.
Waitting to keep warm mode.
2. Measure amount of pouring-out water after change to keep warm immediately.
3. Push on Supporting Plate to pump water for once and measure amount of poring-out water.
Allowance : Amount of water should be 160±30 ml.