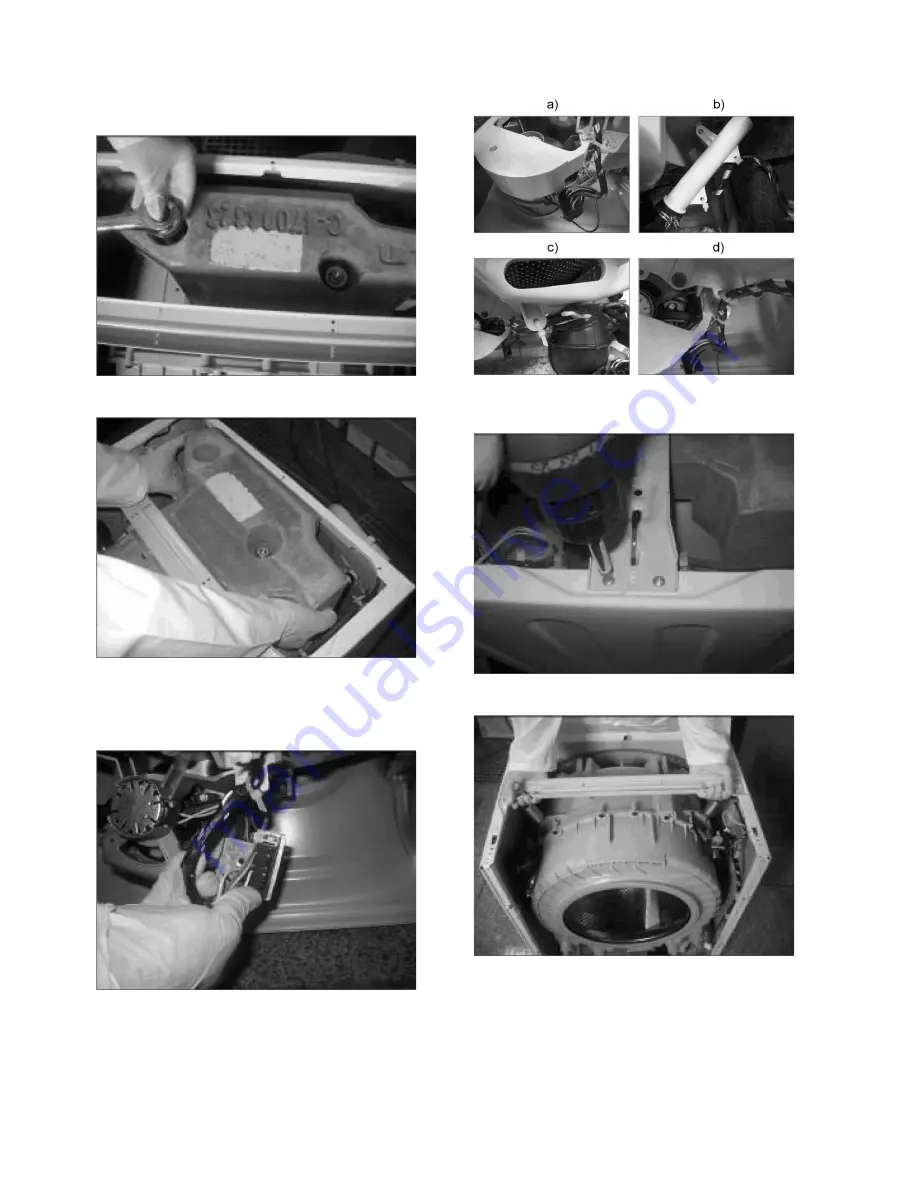
30
10.20. Upper Counterweight
1. Remove two screws fixing the upper counterweight by
using box wrench size 13 mm.
2. Remove the upper counterweight.
10.21. Washing Group
1. Remove the connector that is connected to the motor.
2. Cut the five lead wire holders as shown the pictures.
3. Remove the four screws fixing the spring hanger sheet
iron.
4. Remove the washing group as it is shown in the picture.
Summary of Contents for NA-127VB3
Page 3: ...3 1 Safety Precautions ...
Page 6: ...6 4 Location of Controls and Components ...
Page 13: ...13 ...
Page 43: ...43 12 Dimensions ...
Page 44: ...44 13 Wiring Connection Diagram 13 1 Wiring Diagram NA 127VB3 and NA 147VB3 ...
Page 45: ...45 ...
Page 46: ...46 13 2 Wiring Diagram NA 128VB3 and NA 148VB3 ...
Page 47: ...47 ...
Page 51: ...51 14 3 Washing Group Parts 14 3 1 Exploded View Washing Group Parts ...
Page 54: ...54 14 5 Detergent Drawer Group Parts 14 5 1 Exploded View Detergent Drawer Group Parts ...
Page 57: ...57 14 7 Body Group Parts 14 7 1 Exploded View Body Group Parts ...