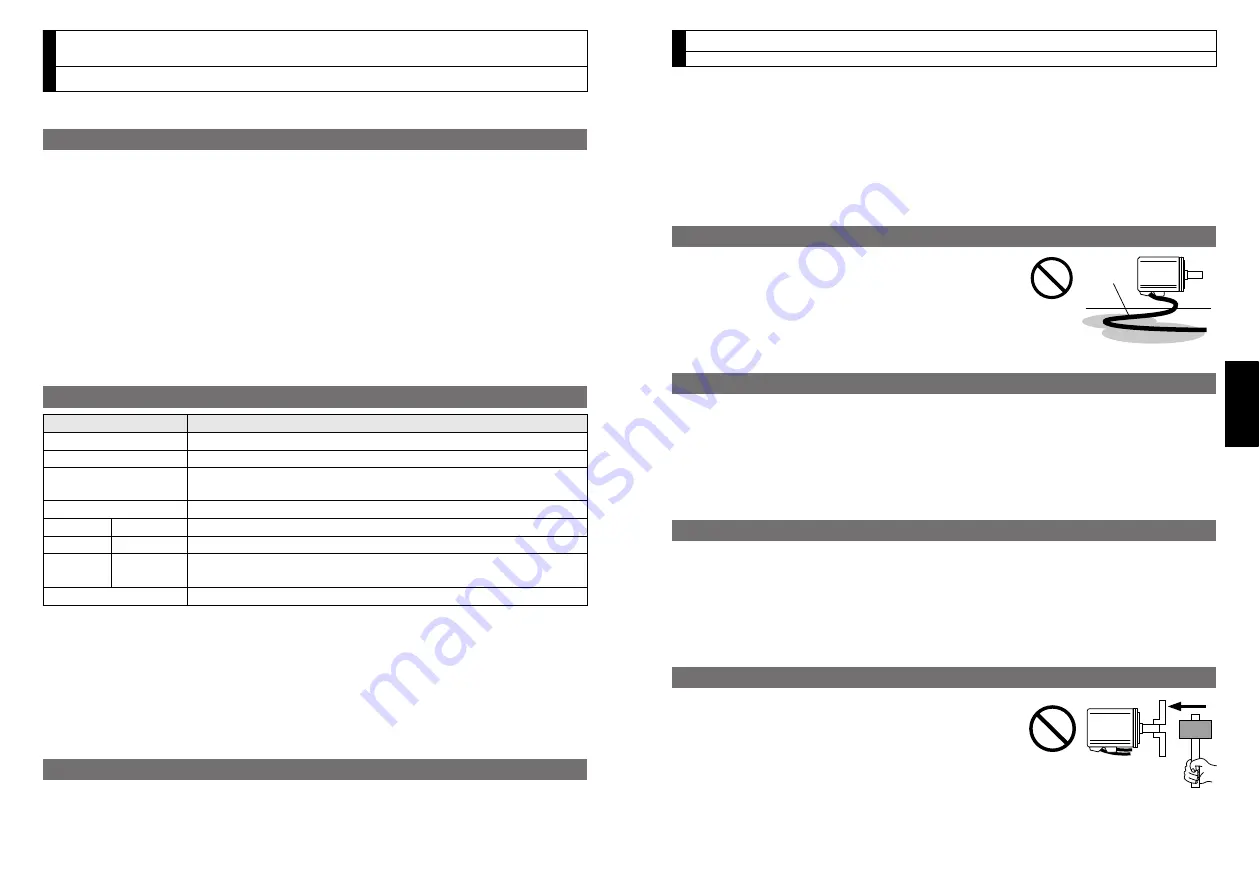
−
B7
−
−
B6
−
English
2) Vertical mounting
• Use the motor with oil seal (make-to-order in case of motor 750 W or less) when
mounting the motor with gear reducer to prevent the reducer oil/grease from enter-
ing to the motor.
3) For the dimensions and mass of the product, which are necessary design data of
the mounting section, refer to the dimensional outline drawing on the Operating In-
structions (Overall) or the Delivery Specification.
Oil/Water Protection
1) Don't submerge the motor cable to water or oil.
2) Install the motor with the cable outlet facing down-
ward.
3) Avoid a place where the motor is always subject-
ed to oil or water.
4) Use the motor with an oil seal when used with the
gear reducer, so that the oil may not enter to the motor through shaft.
Stress to Cables
1) Avoid a stress application to the cable outlet and connecting portion by bending or
self-weight.
2) Especially in an application where the motor itself travels, fix the attached cable and
contain the extension junction cable into the bearer so that the stress by bending
can be minimized.
3) Take the cable bending radius as large as possible. (When you use our optional
cable, Minimum R20 mm)
Permissible Load to Output Shaft
1) Design the mechanical system so that the applied radial load and/or thrust load to
the motor shaft at installation and at normal operation can meet the permissible
value specified to each model.
2) Pay an extra attention when you use a rigid coupling. (Excess bending load may
damage the shaft or deteriorate the bearing life.)
3) Use a flexible coupling with high stiffness designed exclusively for servo application in order
to make a radial thrust caused by micro misalignment smaller than the permissible value.
Notes on Installation
1) Do not apply direct impact to the shaft by hammer
while attaching/detaching a coupling to and from
the motor shaft.
(Or it may damage the encoder mounted on the
other side of the shaft.)
2) Make a full alignment. (incomplete alignment may
cause vibration and damage the bearing.)
3) If the motor shaft is not electrically grounded, it may cause electrolytic corrosion to
the bearing depending on the condition of the machine and its mounting environment,
and may result in the bearing noise. Check and verification by customer is required.
2. Installation
Motor
2. Installation
Motor
Install the motor properly to avoid a breakdown or an accident.
Installation Place
Since the conditions of location affect a lot to the motor life, select a place
which meets the conditions below.
1) Indoors, where the products are not subjected to rain or direct sun beam. The prod-
ucts are not waterproof.
2) Where the products are not subjected to corrosive atmospheres such as hydrogen
sulfide, sulfurous acid, chlorine, ammonia, sulfur, chloric gas, sulfuric gas, acid, al-
kaline and salt and so on, and are free from splash of inflammable gas.
3) Where the motor is free from grinding oil, oil mist, iron powder or chips.
4) Well-ventilated and humid and dust-free place, far apart from the heat source such
as a furnace.
5) Easy-to-access place for inspection and cleaning
6) Vibration-free place.
7) Avoid enclosed place. Motor may gets hot in those enclosure and shorten the motor life.
Environmental Conditions
Item
Conditions
Ambient temperature
*
1
0 ˚C to 40 ˚C (free from freezing)
Ambient humidity
20 % to 85 % RH (free from condensation)
Storage temperature
*
2
–20 ˚C to 65 ˚C (Max.temperature guarantee: 80 ˚C for 72 hours
free from condensation
*
5
)
Storage humidity
20 % to 85 % RH (free from condensation
*
5
)
Vibration Motor only Lower than 49 m/s
2
(5 G) at running, 24.5 m/s
2
(2.5 G) at stall
Impact
Motor only Lower than 98 m/s
2
(10 G)
Enclosure
rating
Motor only
(Connector type)
IP67 (except rotating portion of output shaft and connecting pin
part of the motor connector and the encoder connector)
*
3
*
4
Altitude
Lower than 1000 m
*
1 Ambient temperature to be measured at 5 cm away from the motor.
*
2 Permissible temperature for short duration such as transportation.
*
3 These motors conform to the test conditions specified in EN standards (EN60529, EN60034-
5). Do not use these motors in application where water proof performance is required such as
continuous wash-down operation.
*
4 This condition is applied when the connector mounting screw in case of motor 750 W or less
are tightened to the recommended tightening torque (Refer to P.B21, 25). Be sure to use
mounting screw supplied with the connector.
*
5 Air containing water vapor will become saturated with water vapor as the temperature falls,
causing dew.
How to Install
You can mount the motor either horizontally or vertically as long as you observe the
followings.
1) Horizontal mounting
• Mount the motor with cable outlet facing downward for water/oil countermeasure.
Cable Motor
Oil / Water
Motor