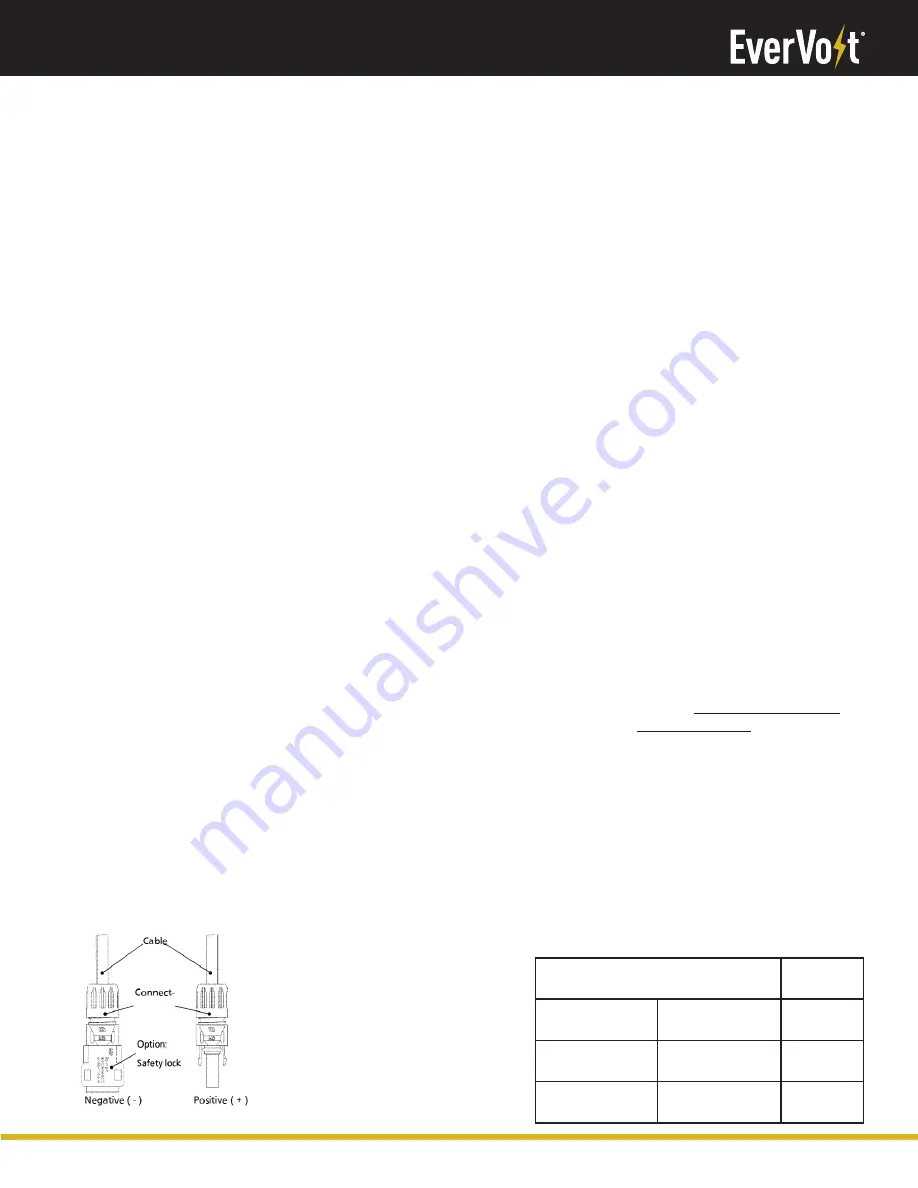
7
General Installation Manual
STANDARDS
EVPVxxx, EVPVxxxK, EVPVxxxH,
EVPVxxxHK and EVPVxxxPK series are
rated for use in Electrical Application
Class A, Protection Safety Class II; at
hazardous level of voltage (>35V), current
(>8A) and power (>240W) where general
contact access is anticipated (panels,
qualified for safety through UL 61730-1
and -2).
FIRE CLASS OF PRODUCT
The EverVolt modules covered by this
manual have a Class C (referencing
UL790) and Type 2 fire classification
according to UL1703/UL61730.
The fire performance rating of the
modules is only valid when mounted in
the manner specified in this installation
manual.
The complete system fire class rating is to
be achieved by the combination of module
fire performance type and UL2703
certified mounting structure for a non-
BIPV module.
Please refer to mounting structure
UL2703 listing for System Fire
Classification. Any specific limitations on
the inclination or accessories required
to maintain a specific System Fire Class
Rating must be clearly specified in
the mounting system manufacturer’s
installation instructions
and UL2703 certification.
Utilize the following fire safety guidelines
when installing EverVolt modules:
• Check with all relevant local
authorities for fire safety
requirements for any building or
structure on to which the modules
will be installed.
• The system design must ensure that
it can be easily accessed in the event
of a building fire.
• Check with relevant authorities for
applicable regulations concerning
setbacks or other placement
restrictions that may apply for
roofmounted arrays.
• The use of DC ground fault
interrupters is recommended. This
may also be required by local and
national codes.
• All electrical appliances are a
fire risk. The module must be
mounted over a fire retardant roof
covering rated for the application
and a distance of at least 0.8 in
(20 mm) between the module and
the mounting surface, to allow the
free circulation of air beneath the
modules at all times.
JUNCTION BOX, TERMINALS,
AND CONNECTORS
• Modules equipped with three
junction box contain terminals for
both positive and negative polarity
individually, and bypass diodes.
• Each terminal is dedicated to one
polarity (with the polarity symbols
engraved onto the body of the
junction box) (see Figure 1).
• Each terminal is provided with
factory installed lead cables and a
latching connector for series and
string connections. Always use these
connectors and do not detach them
from cables.
• The PV module comes pre-wired.
Each module has two #12 AWG type
PV-wire stranded sunlight resistant
output cables each terminated
with connectors. The positive (+)
terminal has a male connector
while the negative (-) terminal has
a female connector. The module
wiring is solely for series connections
only, i.e. male (+) to female (-)
interconnections. When making
field wiring connections to the
pre-attached connectors use only
approved connectors from Table 2.
• All connectors and cables must
be secure and tight as well as
electrically and mechanically sound.
UVresistant cables and connectors
approved for outdoor use must be
used. Conductor gauge must be
chosen to ensure DC power losses
(voltage drop) are kept to a minimum
(<1%).
• Observe all local regulations when
selecting cables.
• For string connections, use minimum
12 AWG (4 mm2) or copper wires
insulated for a maximum operating
temperature of 194°F (90°C).
• Avoid exposing cables to direct
sunlight and permanent tension.
• To ensure connector compatibility
and reduce the potential for damage
to the modules and the wider
installation, the connectors used on
the EverVolt modules are detailed
in the Figure 2. Only permitted
the mating of factory-installed
connectors to connectors of the
same manufacturer, type, and system
rating as shown in the table below
(Table.2).
• Latching connectors are type IV and
made by
STAUBLI ELECTRICAL
CONNECTORS AG
. Supplied
connectors listed by UL.
• In order to comply with NEC 2008, a
locking sleeve needs to be used with
all connectors that are exposed.
• The locking sleeve (PV-SSH4) is made
by STAUBLI and can only be released
with a special tool also made by
STAUBLI (PV-MS). Locking sleeves
are not supplied with modules and
must be purchased separately.
Figure 4. Connectors
CONNECTORS
Stäubli MC4 PV-KBT4/KST4,
12AWG(4 mm²) in accordance
with IEC 62852 only when connected
Connector 1 + Connector 2
Permitted?
EverVolt Module
Factory-Installed
EverVolt Module
Factory-Installed
✓
EverVolt Module
Factory-Installed
Stäubli MC4
✓
EverVolt Module
Factory-Installed
Any other
connector
NG
Table 3. Approved connectors