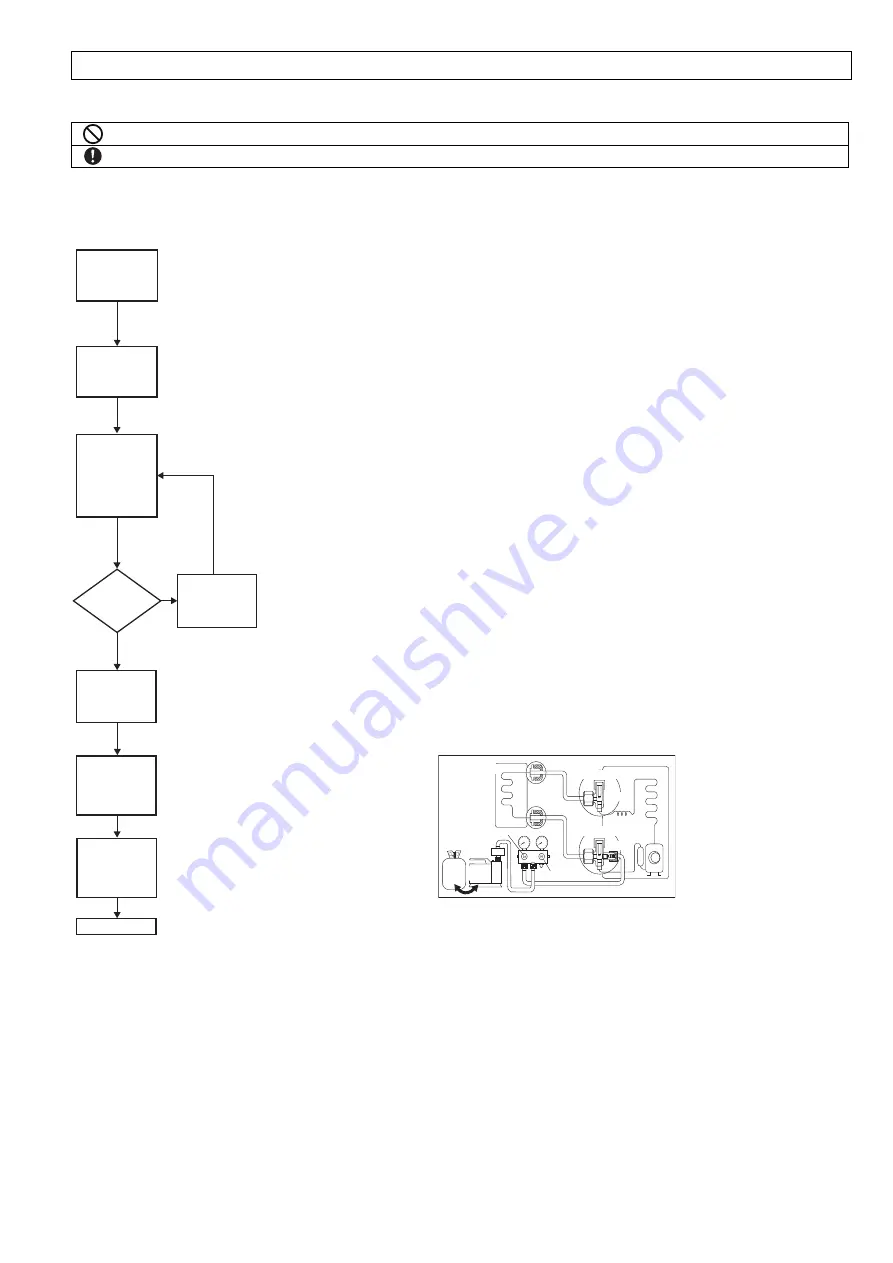
57
AIR PURGING METHOD IS PROHIBITED FOR R32 SYSTEM
12.4.3 Air Tightness Test on the Refrigerating System
Do not purge the air with refrigerants but use a vacuum pump to vacuum the installation.
There is no extra refrigerant in the outdoor unit for air purging.
Before system is charged with refrigerant and before the refrigerating system is put into operation, below site test
procedure and acceptance criteria shall be verified by the certified technicians, and/or the installer.
Be sure to check whole system for gas leakage.
1 Connect a charging hose with a push pin to the Low side of a charging set and
the service port of the 3-way valve.
2 Attach the gauge manifold set correctly and tightly. Make sure that both valves
of the manifold gauge (low pressure and high pressure) is in close position.
3 Connect the center hose of the manifold gauge to a vacuum pump.
4 Turn on the power switch of the vacuum pump, then turn open the low side
manifold gauge valve and make sure that the needle in the gauge moves from
0cmHg (0 MPa) to –76 cmHg (–0.1 MPa) or vacuum until 500 microns is
achieved. This process continues for approximately ten minutes. Then close
the low side manifold gauge valve.
5 Remove the vacuum pump from the centre hose and connect the center hose
to cylinder of any applicable inert gas as test gas.
6 Charge test gas into the system and wait until the pressure within the system to
reach min. 1.04MPa (10.4barg).
7 Wait and monitor the pressure reading on the gauges. Check if there is any
pressure drop.
Waiting time depends on the size of the system.
8 If there is any pressure drop, perform step 9-12. If there is no pressure drop,
perform step 13.
9 Use Gas Leak Detector to check for leaks. Must use the detection equipment
with a sensitivity of 5 grams per year of test gas or better.
10 Move the probe along the air conditioning system to check for leaks, and mark
for repair.
11 Any leak detected and marked shall be repaired.
12 After repair, repeat evacuation steps 3-4 and tightness test steps 5-7.
Check the pressure drop as in step 8.
13 If no leak, Recover the test gas. Perform evacuation of steps 3-4. Then
proceed to step 14.
14 Disconnect the charging hose from the service port of the 3-way valve.
15 Tighten the service port caps of the 3-way valve at a torque of 18 N•m with a
torque wrench.
16 Remove the valve caps of both of the 2-way valve and 3-way valve.
17 Open both of the valves, using a hexagonal wrench (4mm).
It is recommended to allow refrigerant slowly flow into the refrigerant system to
prevent refrigerant freezing. Slightly open 2-way valve for 5 seconds then close
the valve. Repeat this action for 3 cycles then fully open the valve.
18 Mount back the valve caps onto the 2-way valve and the 3-way valve to
complete this process.
Notes:
Recommended use of any of the following leak detector,
I) Universal Sniffer leak detector
II) Electronic halogen leak detector
III) Ultrasonic Leak Detector
Preparation
(Step 1-2)
Evacuation
(Step 3-4)
Tightness Test
with Inert Gas
(Step 5-7)
Pressure drop?
(Step 8)
YES
NO
Leak detection
and repair
(Step 9-12)
Recovery of Test
Gas
(Step 13)
Evacuation
(Step 3-4)
Open 2 and 3
valves
(Step 14-18)
Complete
Liquid side
Tank
Cylinder
Indoor unit
Inert
gas
Vacuum
pump
OPEN
CLOSE
Gas side
Two-way valve
Close
Close
Three-way valve
Outdoor unit