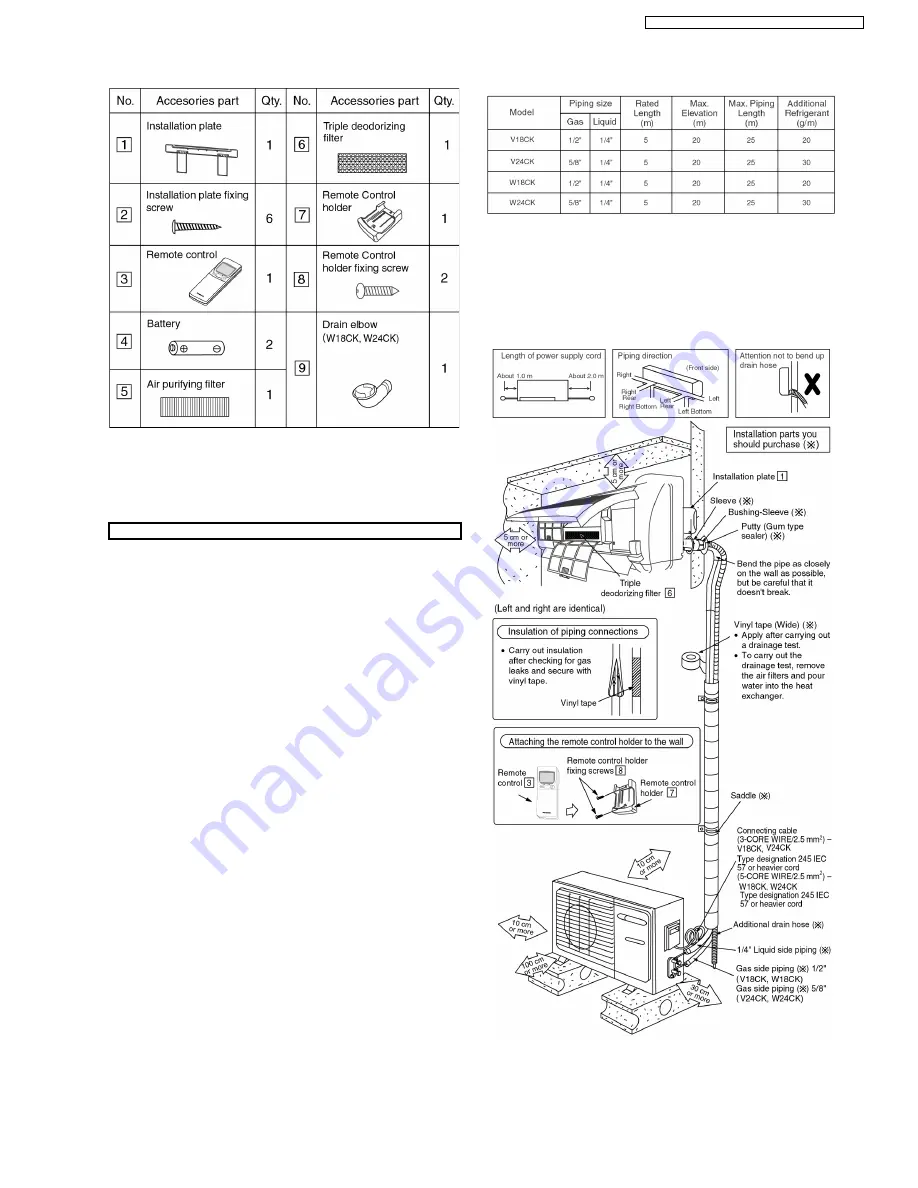
Applicable piping kit
CZ-4F5, 7, 10AN (V18CK, W18CK)
CZ-52F5, 7, 10AN (V24CK, W24CK)
SELECT THE BEST LOCATION
INDOOR UNIT
•
•
•
•
There should not be any heat source or steam near the
unit.
•
•
•
•
There should not be any obstacles blocking the air
circulation.
•
•
•
•
A place where air circulation in the room is good.
•
•
•
•
A place where drainage can be easily done.
•
•
•
•
A
place
where
noise
prevention
is
taken
into
consideration.
•
•
•
•
Do not install the unit near the door way.
•
•
•
•
Ensure the spaces indicated by arrows from the wall,
ceiling, fence or other obstacles.
•
•
•
•
Recommended installation height for indoor unit shall be
at least 2.3 m.
OUTDOOR UNIT
•
•
•
•
If an awning is built over the unit to prevent direct
sunlight or rain, be careful that heat radiation from the
condenser is not obstructed.
•
•
•
•
There should not be any animal or plant which could be
affected by hot air discharged.
•
•
•
•
Keep the spaces indicated by arrows from wall, ceiling,
fence or other obstacles.
•
•
•
•
Do not place any obstacles which may cause a short
circuit of the discharged air.
•
•
•
•
If piping length is over 7.5m, additional refrigerant
should be added as shown in the table.
Example: For W24CK
If the unit is installed at a 10m distance, the quantity of
additional refrigerant should be 75g...(10 - 7.5)m × 30g/m =
75g
Indoor/Outdoor Unit Installation Diagram
•
•
•
•
This illustration is for explanation purposes only.
The indoor unit will actually face a different way.
Attached accessories
45
CS-W18CKE CU-W18CKE / CS-W24CKE CU-W24CKE
Summary of Contents for CS-W18CKE
Page 10: ...4 Dimensions 10 CS W18CKE CU W18CKE CS W24CKE CU W24CKE ...
Page 11: ...11 CS W18CKE CU W18CKE CS W24CKE CU W24CKE ...
Page 12: ...5 Refrigeration Cycle Diagram 12 CS W18CKE CU W18CKE CS W24CKE CU W24CKE ...
Page 13: ...6 Block Diagram 13 CS W18CKE CU W18CKE CS W24CKE CU W24CKE ...
Page 14: ...7 Wiring Diagram CS W18CKE CU W18CKE CS W24CKE CU W24CKE 14 ...
Page 34: ...34 CS W18CKE CU W18CKE CS W24CKE CU W24CKE ...
Page 36: ...39 40 41 38 36 CS W18CKE CU W18CKE CS W24CKE CU W24CKE ...
Page 37: ...39 37 CS W18CKE CU W18CKE CS W24CKE CU W24CKE ...
Page 38: ...35 37 38 CS W18CKE CU W18CKE CS W24CKE CU W24CKE ...
Page 39: ...38 39 CS W18CKE CU W18CKE CS W24CKE CU W24CKE ...
Page 40: ...39 40 CS W18CKE CU W18CKE CS W24CKE CU W24CKE ...
Page 41: ...41 CS W18CKE CU W18CKE CS W24CKE CU W24CKE ...
Page 70: ...14 Technical Data 70 CS W18CKE CU W18CKE CS W24CKE CU W24CKE ...
Page 72: ...72 CS W18CKE CU W18CKE CS W24CKE CU W24CKE ...
Page 73: ...73 CS W18CKE CU W18CKE CS W24CKE CU W24CKE ...
Page 82: ...SCHEMATIC DIAGRAM 5 5 82 CS W18CKE CU W18CKE CS W24CKE CU W24CKE ...
Page 84: ...19 1 REMOTE CONTROL 84 CS W18CKE CU W18CKE CS W24CKE CU W24CKE ...