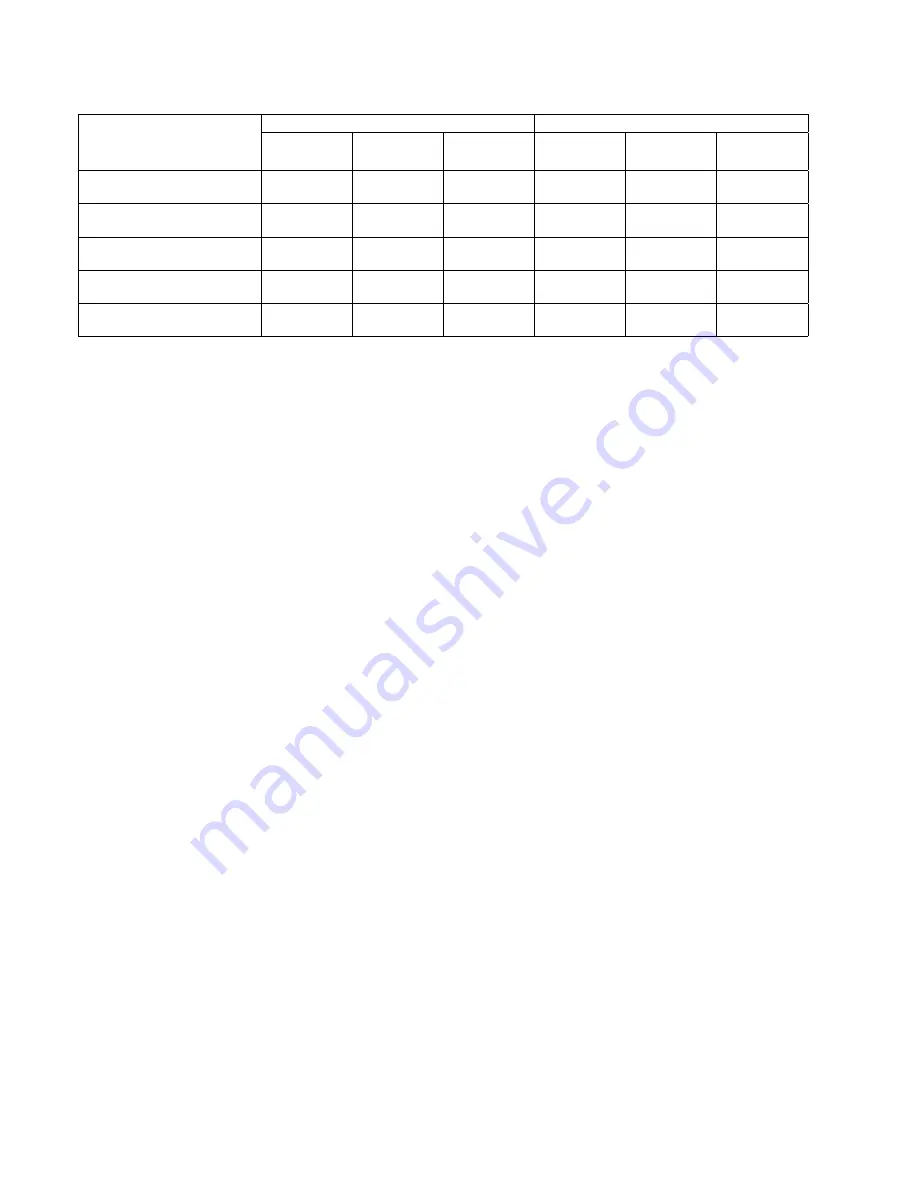
52
14.2 Relationship Between The Condition Of The Air Conditioner And
Pressure And Electric Current
Condition of the
air conditioner
Cooling Mode
Heating Mode
Low Pressure
High Pressure
Electric current
during operation
Low Pressure
High Pressure
Electric current
during operation
Insufficient refrigerant
(gas leakage)
Ô
Ô
Ô
Ô
Ô
Ô
Clogged capillary tube
or Strainer
Ô
Ô
Ô
Ò
Ò
Ò
Short circuit in the indoor unit
Ô
Ô
Ô
Ò
Ò
Ò
Heat radiation deficiency
of the outdoor unit
Ò
Ò
Ò
Ô
Ô
Ô
Inefficient compression
Ò
Ô
Ô
Ò
Ô
Ô
• Carry out the measurement of pressure, electric current, and temperature fifteen minutes after an operation is started.
Summary of Contents for CS-ME9PB4EA
Page 28: ...28 4 Location of Controls and Components 4 1 Indoor Unit 4 2 Outdoor Unit 4 3 Remote Control...
Page 29: ...29 5 Dimensions 5 1 Indoor Unit...
Page 30: ...30 6 Refrigeration Cycle Diagram...
Page 31: ...31 7 Block Diagram...
Page 32: ...32 8 Wiring Connection Diagram 8 1 Indoor Unit...
Page 33: ...33 9 Electronic Circuit Diagram 9 1 Indoor Unit...
Page 34: ...34 10 Printed Circuit Board 10 1 Indoor Unit 10 1 1 Main Printed Circuit Board...
Page 81: ...81 16 Exploded View and Replacement Parts List 16 1 Indoor Unit...