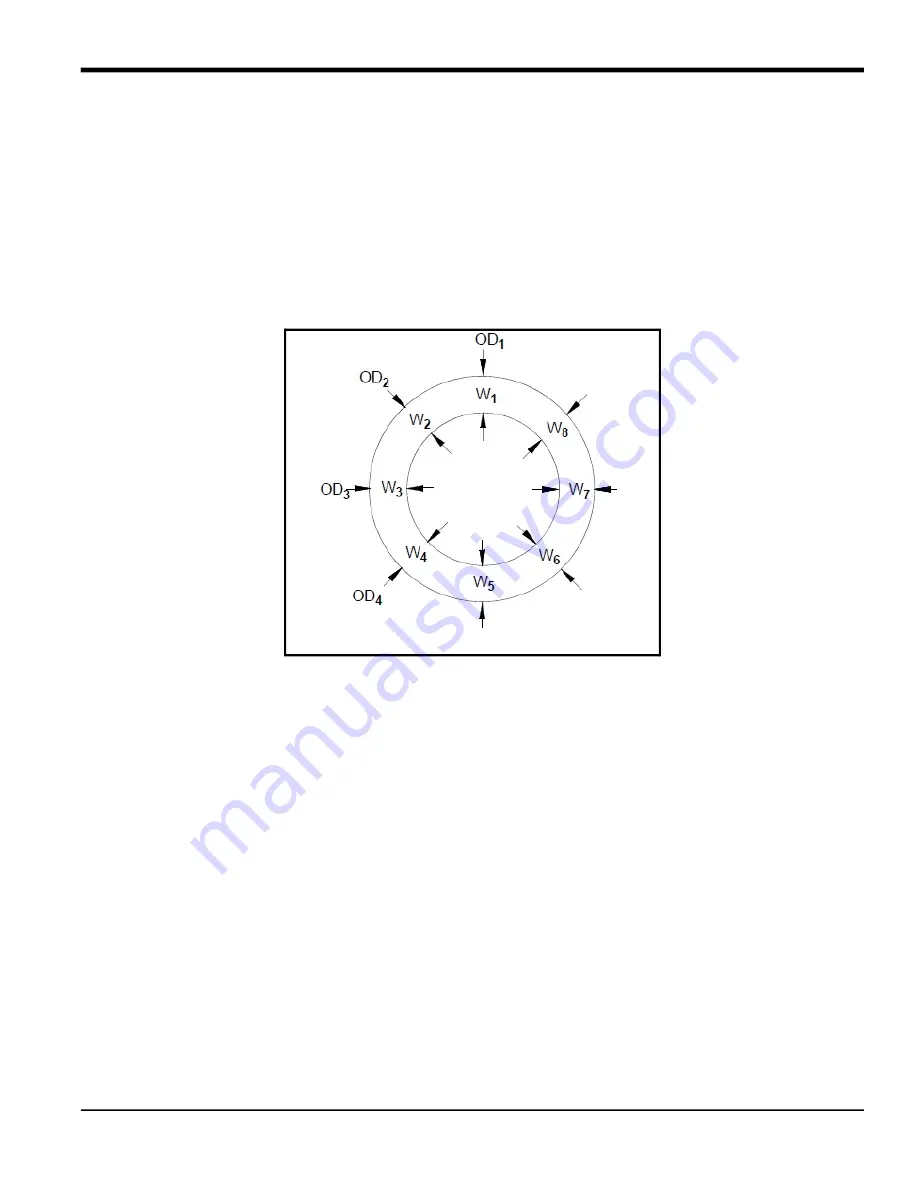
Model C-ET Installation Guide
13
1.3.2.2
Pipe Survey to Determine OD and Wall Thickness
Finding a location where the pipe is concentric is important for optimum accuracy and performance. If possible,
perform a pipe survey with an ultrasonic thickness gauge to find the best location.
Measure the outside diameter (OD) of the pipe using a tape measure or other suitable device. Mark a circumferential
line with the tape measure.
Note:
If you are using a PT878 thickness gauge at extreme high or low temperatures, it can be in contact with the
pipe for less than two seconds only and then must be removed. Allow it to cool for a minimum of 2 minutes
before taking another measurement.
Now measure the OD and the wall thickness at eight points along the pipe circumference at 45° intervals (shown in
Figure 8), three times per point, and record the mean values. Use the mean value for the wall thickness.
Figure 8: Measuring the Wall Thickness
To determine the meter's correction factor for non-concentric pipes, calculate the mean inside pipe diameter (ID)
and the pipe ID at the transducer locations. Then divide the square of the mean ID by the square of the ID at the
transducer location, as shown in the equations below, where ODX is the outside diameter at a given point, and WX is
the wall thickness at a given point (as shown in Figure 3-6 on the previous page).
mean ID = [((OD
1
– (W
1
+ W
2
)) + (OD
2
– (W
2
+W
6
)) + (OD
3
– (W
3
+ W
7
)) + (OD
4
– (W
4
+ W
8
))] / 4
K
for non-concentric pipe
Mean ID
2
ID at transducer location
2
--------------------------------------------------
=
Summary of Contents for C-ET
Page 2: ......
Page 4: ...ii no content intended for this page...
Page 6: ...Contents iv Model C ET Installation Guide...
Page 48: ...Warranty 40 Model C ET Installation Guide no content intended for this page...
Page 49: ......