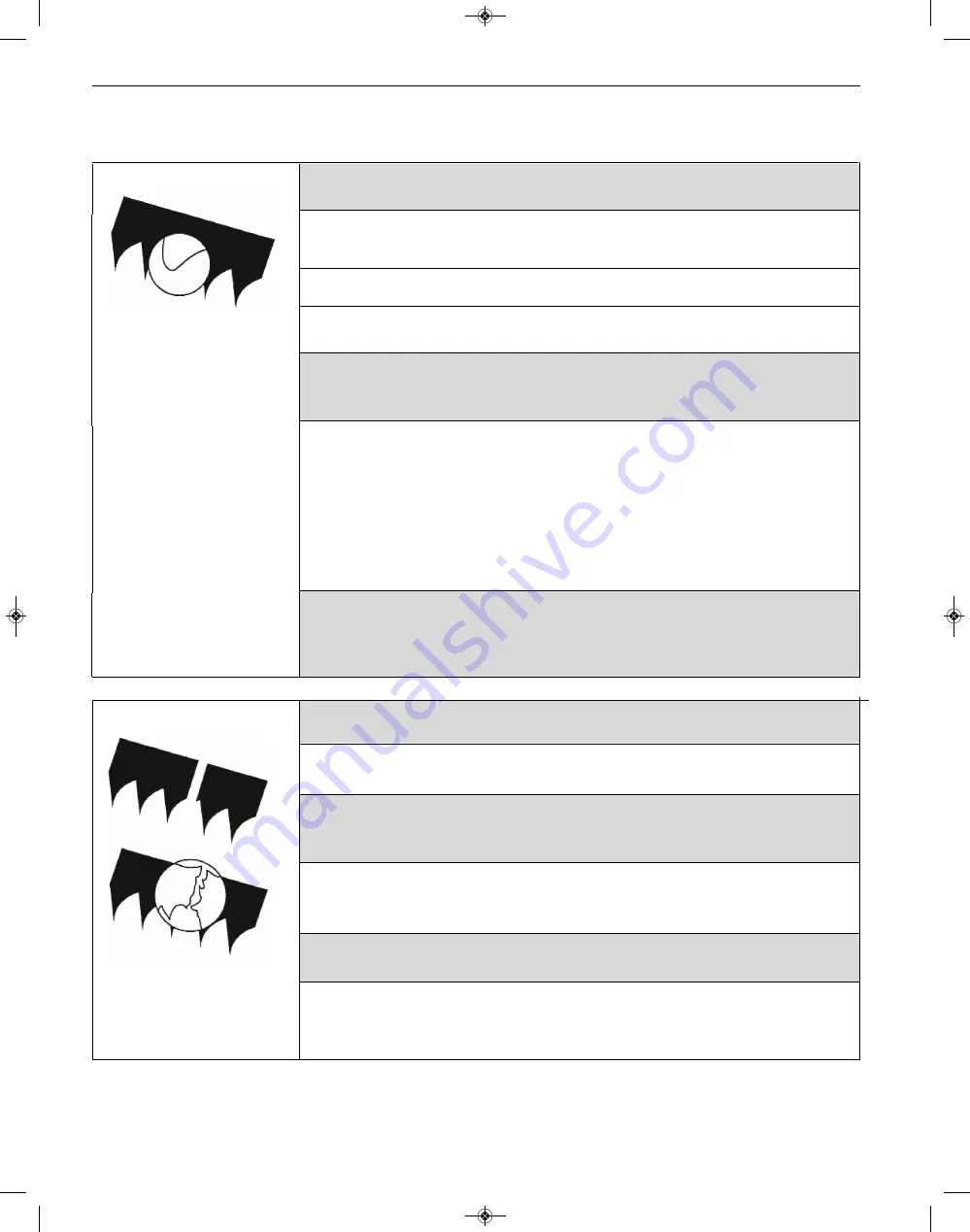
Poor quality blade
Switch to a superior quality blade.
Cut advancing too quickly
Decrease cutting advance, exerting less cutting
pressure. Adjust the braking device.
TROUBLESHOOTING (CONTINUED)
12
Palmgren Operating Manual & Parts List 9683295
SYMPTOM POSSIBLE CAUSE(S) CORRECTIVE ACTION
Premature blade wear
Faulty running-in of blade
See OPERATION - BLADE SELECTION
GUIDE LINES page 9.
Teeth positioned in the direction opposite
of the cutting direction
Remove the blade and reinstall it with the teeth
cutting in the proper direction.
Poor quality blade
Switch to a superior quality blade.
Cut advancing too quickly
Decrease cutting advance, exerting less cutting
pressure. Adjust the braking device.
Wrong cutting speed
Change speed and/or type of blade.
See OPERATION - BLADE SELECTION
GUIDE LINES page 9.
Defects on the material or material too
hard
Material surfaces can be oxidized or covered with
impurities making these areas harder than the
blade itself. Materials may have hardened areas
or inclusions inside the section due to production
materials such as castings and welding wastes,
etc. Avoid cutting these materials. In a situation
where a cut has to be made use extreme care,
cleaning and removing hard impurities as quickly
as possible.
Insufficient lubricating refrigerant or wrong
emulsion
Check level of liquid in the tank. Increase the
flow of lubricant. Check to ensure the blade
guide outlet hole and the liquid outlet pipe are not
blocked. Check the lubricant viscosity.
Blade breakage/damage
Faulty welding of blade
Switch to a superior quality blade.
Cut advancing too quickly
Decrease cutting advance, exerting less cutting
pressure. Adjust the braking device.
Wrong cutting speed
Change speed and/or type of blade.
See OPERATION - BLADE SELECTION
GUIDE LINES page 9.
Wrong tooth pitch
Replace blade choosing the proper tooth pitch.
See OPERATION - BLADE SELECTION
GUIDE LINES page 9.
Blade touching material at beginning of
cut
At the beginning of the cutting process, never
lower the saw bow into the material before
starting the machine.
Ineffective gripping of the part in the vice
Check the gripping of the part being cut. Tighten
the vise as needed.
9683295_oipm_En012_9645931.01-0620 __ 07-02-2020 . . . .