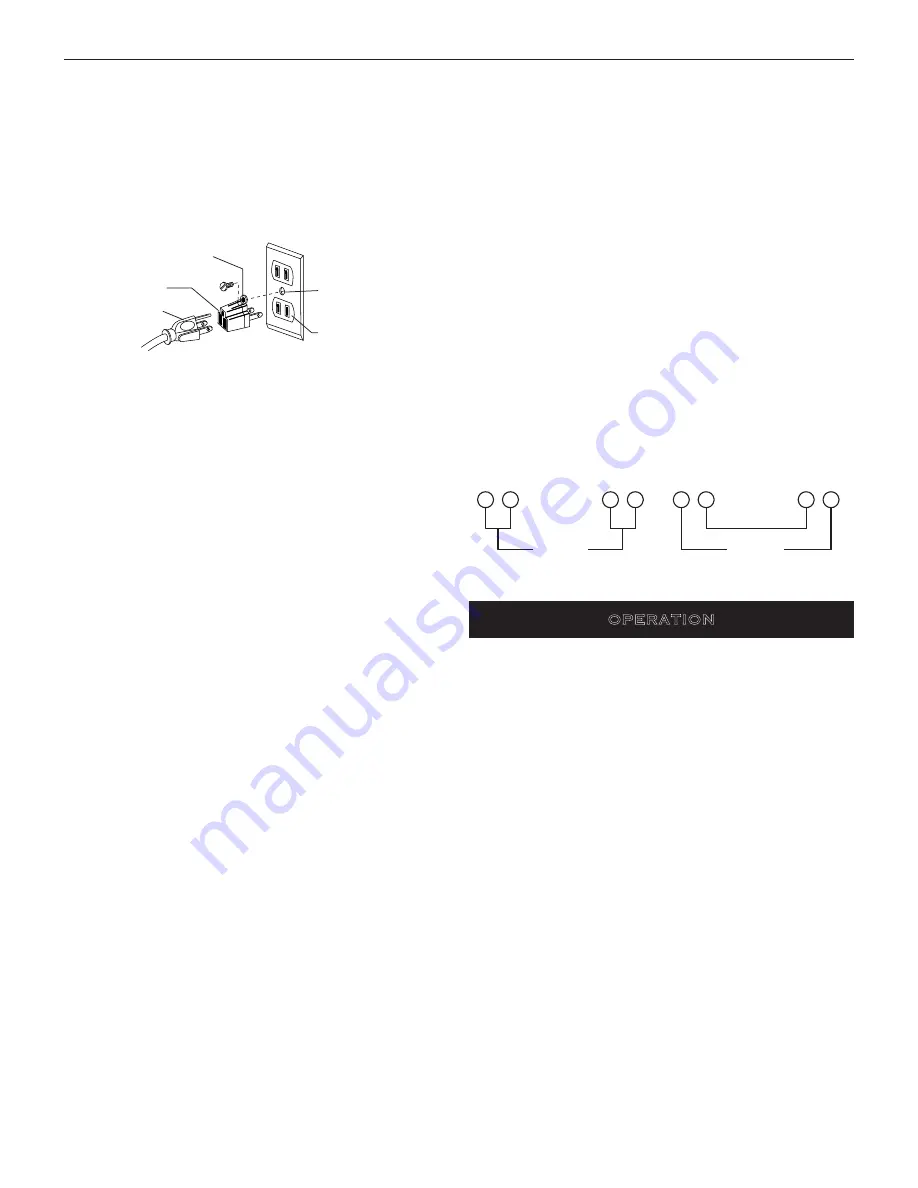
5
Palmgren Operating Manual & Parts List
80177
Green (or green and yellow) conductor in cord is the grounding wire.
If repair or replacement of the electric cord or plug is necessary, do
not connect the green (or green and yellow) wire to a live terminal.
Where a 2-prong wall receptacle is encountered, it must be replaced
with a properly grounded 3-prong receptacle installed in accordance
with National Electric Code and local codes and ordinances.
WARNING:
This work should be performed by a qualified electrician.
A temporary 3-prong to 2-prong grounding adapter (See Figure 3)
is available for connecting plugs to a two pole outlet if it is properly
grounded.
Do not use a 3-prong to 2-prong grounding adapter unless
permitted by local and national codes and ordinances.
(A 3-prong to 2-prong grounding adapter is not permitted in
Canada.) Where permitted, the rigid green tab or terminal on the
side of the adapter must be securely connected to a permanent
electrical ground such as a properly grounded water pipe, a properly
grounded outlet box or a properly grounded wire system.
Many cover plate screws, water pipes and outlet boxes are not
properly grounded. To ensure proper ground, grounding means
must be tested by a qualified electrician.
EXTENSION CORDS
●
The use of any extension cord will cause some drop in voltage
and loss of power.
●
Wires of the extension cord must be of sufficient size to carry the
current and maintain adequate voltage.
●
Use the table to determine the minimum wire size (A.W.G.)
extension cord.
●
Use only 3-wire extension cords having 3-prong grounding type
plugs and 3-pole receptacles which accept the tool plug.
●
If the extension cord is worn, cut, or damaged in any way, replace
it immediately.
EXTENSION CORD LENGTH (120 VOLTS)
Wire Size A.W.G.
Up to 25 ft. . . . . . . . . . . . . . . . . . . . . . . . . . . . . . . . . . . . . . . . . . . . . . . . . . . . . . .14
25-50 ft. . . . . . . . . . . . . . . . . . . . . . . . . . . . . . . . . . . . . . . . . . . . . . . . . . . . . . . . . .12
NOTE:
Using extension cords over 50 ft. long is not recommended.
EXTENSION CORD LENGTH (240 VOLTS)
Wire Size A.W.G.
Up to 50 ft. . . . . . . . . . . . . . . . . . . . . . . . . . . . . . . . . . . . . . . . . . . . . . . . . . . . . . . 18
50-100 ft. . . . . . . . . . . . . . . . . . . . . . . . . . . . . . . . . . . . . . . . . . . . . . . . . . . . . . . . .16
100-200 ft. . . . . . . . . . . . . . . . . . . . . . . . . . . . . . . . . . . . . . . . . . . . . . . . . . . . . . . .14
200-300 ft. . . . . . . . . . . . . . . . . . . . . . . . . . . . . . . . . . . . . . . . . . . . . . . . . . . . . . . .12
NOTE:
Using extension cords over 300 ft. long is not recommended.
POWER SOURCE
For single phase:
Drill press requires a 120/240 volt, 60 Hz power
source. To use the drill press with a 240 V power supply, have a
qualified electrician attach a 240 volt, 20/30 A three-prong plug onto
drill press line cord.
For three phase:
Drill press requires a 120 volt, 60 Hz power source.
ELECTRICAL CONNECTIONS
Refer to Figure 4
WARNING:
All electrical connections must be performed by a
qualified electrician. Make sure unit is off and disconnected from
power source while motor is mounted, connected, reconnected or
anytime wiring is inspected.
●
The motor should be wired for 120 volts and clockwise rotation
as viewed from shaft end of motor.
●
A label on the motor describes the possible wiring
configurations. There are many different possible combinations,
so only the diagram provided with the motor should be used.
●
The power supply to motor is controlled by a push button
switch. Power lines are connected to the quick connect terminals
of the switch.
●
The green ground line must remain securely fastened to the
motor ground terminal to provide proper grounding.
●
To operate drill press at 240 volts, rewire motor as shown in
Figure 4 and replace line cord plug with a 240 volt, 15 A, 3-prong
plug. If motor label has a different wiring configuration, use the
motor label diagram to rewire motor.
NOTE:
Only for the drill press with single phase use.
WARNING:
Read and understand operating instructions and parts
manual before operating this machine.
CAUTION:
The operation of any power tool can result in foreign
objects being thrown into the eyes, which can result in severe
eye damage. Always wear safety glasses complying with United
States ANSI Z87.1 (shown on package) before commencing power
tool operation.
START AND STOP THE DRILL PRESS
Refer to Figure 9/10.
WARNING:
Be sure drill bit is not in contact with workpiece when
motor is started. Start motor and allow bit to come up to full speed
before drilling.
●
The ON/OFF siwtch (Ref. No. 47/48) is located on the front of the
head casting.
●
To turn the drill press on, push START button. Always allow drill
bit to come up to speed before drilling.
●
To turn the drill press off, press the large red OFF paddle or lift
the paddle and press directly on the red OFF button. Do not
leave drill press until the bit has come to a complete stop.
Figure 3 – 2-Prong Receptacle with adapter
3-Prong Plug
Adapter
Grounding Lug
Make sure this is
Connected to a
known Grounded
Receptacle
2-Prong Receptacle
120 Volts
1
3
1
3
4
2
4
2
240 Volts
Figure 4 – Wiring Schematic for Motor
OPERATION