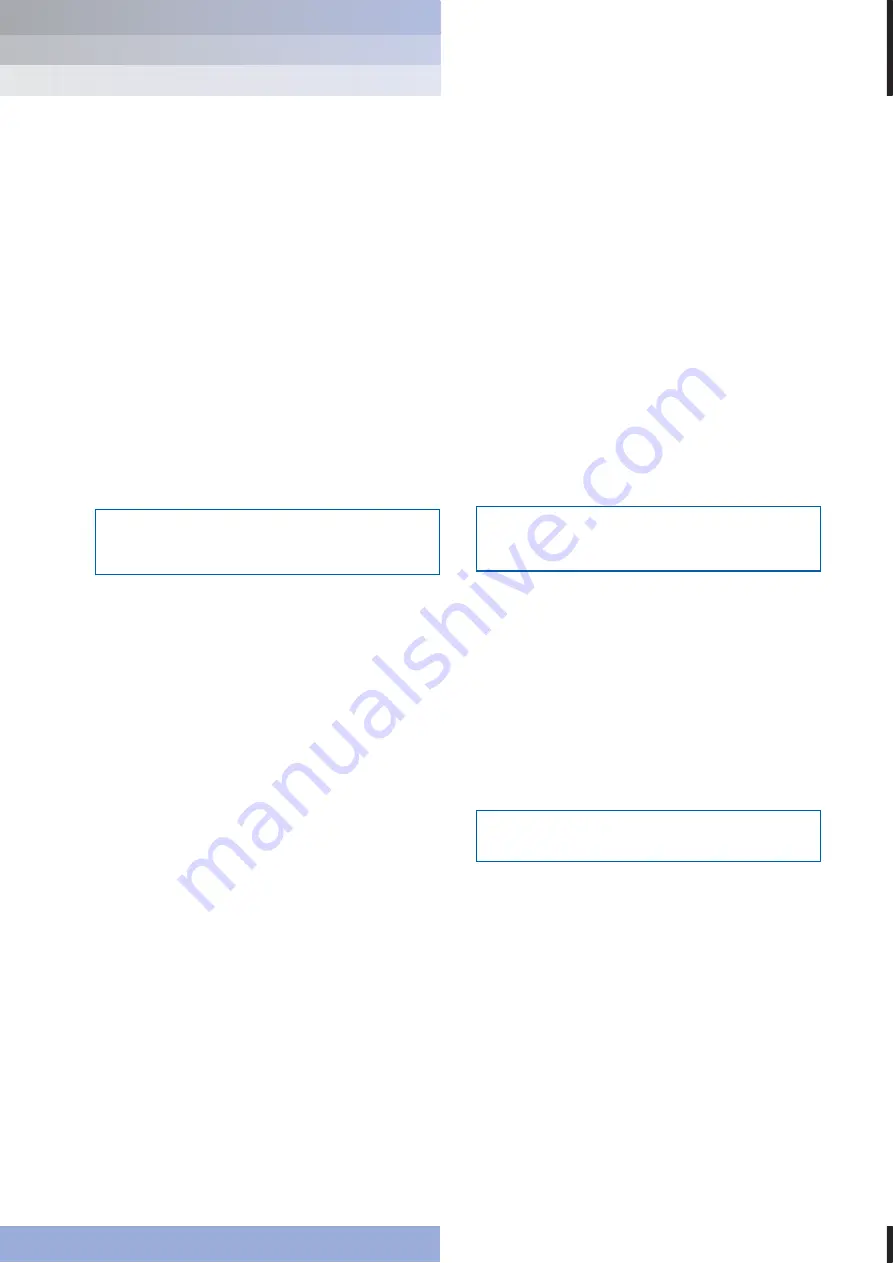
UR619/699
UR619/699 Series
R E T U R N L I N E F I LT E R S
s e r v i c e
i n s t r u c t i o n s
2
1
Specifications
Housing materials:
Head and Tube:
Cast/aluminium alloy
Cover:
Cast iron
Maximum operating pressure:
28 bar (400 psi)
Proof pressure:
42 bar (609 psi)
Minimum burst pressure:
164 bar (2380 psi)
Element burst pressure:
UE619 element 10 bar (150 psid) differential minimum
Operating temperature range:
-29°C to 120°C (-20°F to 250°F) with fluorocarbon seals for petroleum
based and specified synthetic fluids.
60°C (140°F) maximum in HWCF, water-oil emulsion or water glycol
Bypass valve setting options:
1.7 ± 0.3 bar (25 ± 5 psid) cracking pressure
3.4 ± 0.3 bar (50 ± 5 psid) cracking pressure
Non bypass
Seals:
Fluorocarbon
The actual operating conditions should be checked by the user to
ensure that the element, housing and all seals are compatible with
the fluid and application, and are within local safety codes.
Please contact Pall or an approved distributor if further information
is required.
2
Receipt of equipment
The filter housing, and any optional equipment, are packed
individually for assembly by the customer. Unpack carefully and
ensure optional items are not mislaid in packaging to be discarded.
3
General sources of information
3.1
For dimensions, operating parameters, assembly/element part
number, ordering information, notes, performance data and
specifications refer to datasheet PMEUR619 or PMEUR699.
3.2
This equipment has been assessed in accordance with the
guidelines laid down in the European Pressure Directive
97/23/EC and has been classified within sound engineering
practice S.E.P. We hereby declare the equipment meets the
requirements of article 3, section 3, thus meeting the directive
requirements. Under the provisions of this directive the filter
assembly is suitable for use with group 2 fluids only.
3.3
Where under reasonably foreseeable conditions, including
external fires, the allowable limits could be exceeded, suitable
protective devices must be installed by the customer within
the connecting fluid system.
4
Installation of housing
4.1
The filter can be installed in any attitude, but for ease of
servicing, it is recommended that it be installed vertically with
the filter tube and cover pointing upwards.
4.2
The minimum clearance required for element removal is
as follows:
4.2.1 443mm or 17.5" for length 20 and 951mm or 37.5" for
length 40 assemblies.
4.2.2 The UR619/UR699 Housing is supplied without a filter
element. For element installation and servicing
procedures, refer to Section 7.
4.3
Threaded differential pressure devices, when fitted, must be
torque tightened to 30-33 ft/lb or 40-45 Nm. All visual
indicators must be clearly visible
NOTE: The UR619/UR699 housing is supplied with two
machined differential pressure warning device ports, one fitted
with a blanking plug, the other with a plastic shipping plug. If no
differential pressure warning device is ordered, the shipping plug
must be removed and replaced with a 'B' type blanking plug
(P/N HA9000-P8-Kit Z) and torque tightened to 40 ft/lb /54 Nm.
NEVER: Never place the port plug in this port without first
installing uniform size -014 O-ring in lower O-ring groove,
otherwise a small bypass flow will result, allowing contaminant
downstream of the filter element.
4.4
Mount the filter assembly in position using the mounting
bracket kit (13) (if provided). Brackets require four .375"
(10mm) bolts each.
4.4.1 UR619 - Four additional mounting holes with 1/2-
13UNC threads are provided at the inlet port for
mounting the assembly, using the appropriate gasket,
to the top of a reservoir or manifold.
4.4.2 UR699 - Mount the filter assembly using the four
Ø.531" (13.5 mm) mounting holes.
4.4.3 Torque bolts to: 16 lb/ft (22 Nm) minimum for .375"
(10mm) size bolts, and 39 lb/ft (53 Nm) minimum for
.500" (12mm) size bolts.
4.5
Use a check valve downstream of the filter if there is a
possibility of reverse flow.
4.6
Install the filter housing using additional piping/valving to allow
complete filter assembly bypass if filter maintenance is
required without system shutdown.
NOTE: Piping supports should be provided as close as is
practicable to the port connections in order to minimize external
loads. This filter assembly must not be electronically isolated
from the users earthing system. This filter assembly must be
earthed by connecting the users earthing system to one of the
inlet/outlet connections.
4.7
Connect lines or hoses to housing inlet and outlet ports.
CAUTION:
Maximum surge flow should not exceed 1.3 times
normal flow.
CAUTION:
Never operate the filter unless both warning device
ports are sealed.
CAUTION:
Reverse flow through filter element will cause damage.