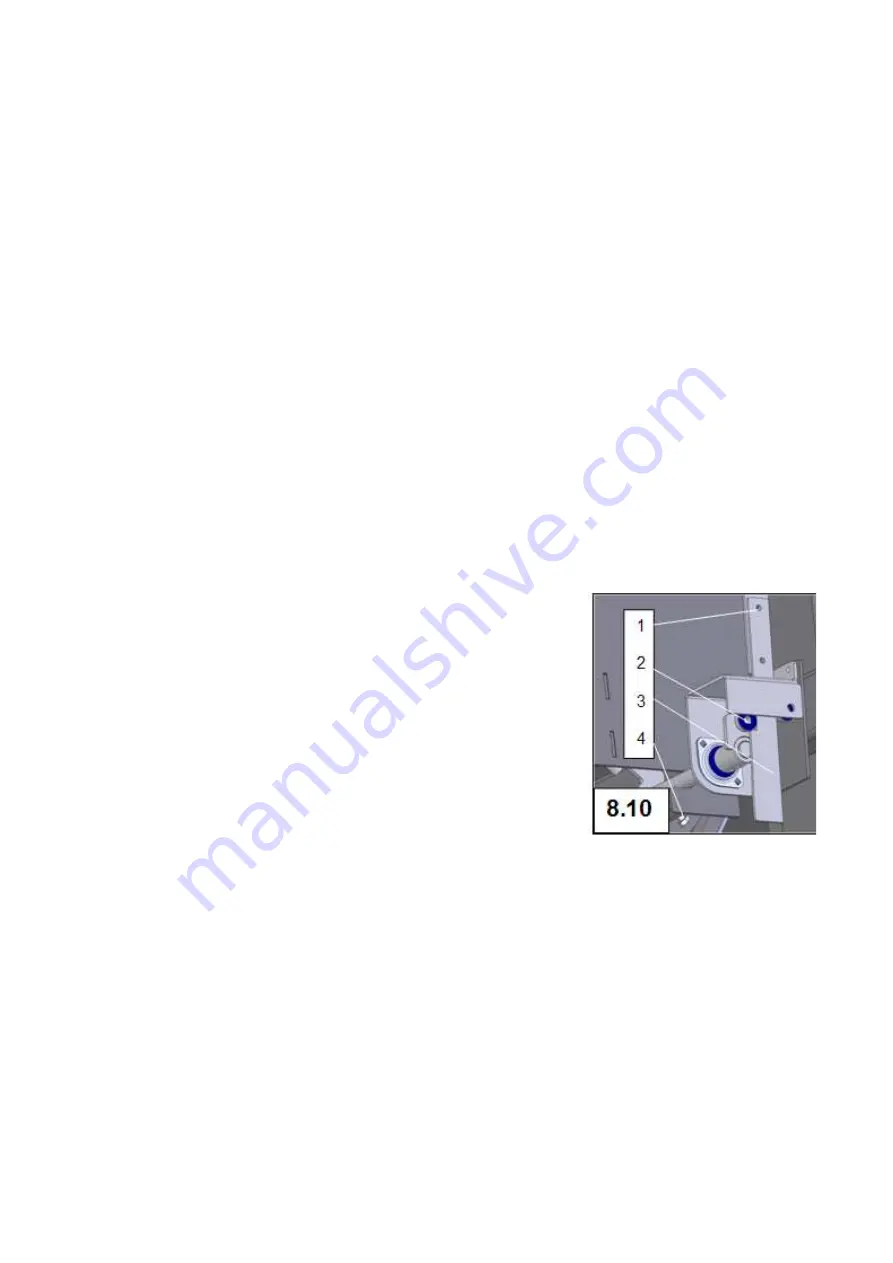
Palax KS50s
Translation
1-2012
31
4. Lift the crosscut saw-bar slowly up and note the moment when the launch
linkage turns the splitting valve to the splitting position.
5. To adjust the starting moment, disconnect the intermediate rod from the
lever arm attached to the end of the saw-shaft.
6. To extend or shorten the intermediate rod, turn the joint at the end of it.
Extending the rod makes the splitting start earlier and shortening it makes
the splitting start later.
8.14 Adjusting the safety devices
If any safety devices, or parts related to them have been dismantled, these
must be adjusted in connection with the re-assembly so that they will
operate properly.
1. Remove the saw-shaft cover and the control panel cover for the
adjustment.
2. Make sure that the saw-shaft is in its upper position, the pusher is in its
rear position, and the splitting valve is in the centre position.
8.14.1 Adjusting the safety wedge and the safety shaft
1. Close the cover for the splitting area.
2. Loosen the adjustment bolts for the safety
wedge (1), and check that the bearing (2)
for the turning device of the safety shaft
makes contact with the narrower part of
the safety wedge (3). As required, lower
the safety wedge.
3. Lift up the safety wedge (3) so, that the
corner of the wedge’s broader part comes
in contact with the bearing (2) of the safety
shaft.
4. Tighten the bolts (1) of the wedge.
5. Adjust the support bolt (4) of the safety
shaft so that its distance to the safety shaft
is 0–2 mm.
8.14.2 Adjusting the safety rod for the saw-shaft
1. Check that the safety wedge and the
safety shaft are correctly adjusted, point
8.14.1.
2. Open the cover for the splitting area.
3. Adjust the distance between the support
roller (2) for the safety rod and the sector-
plate of the safety shaft to 1–4 mm.
Observe that the sector-plate runs in the
support roller’s groove.
4. Loosen the lock nut (4) for the saw-shaft’s
safety rod (3).