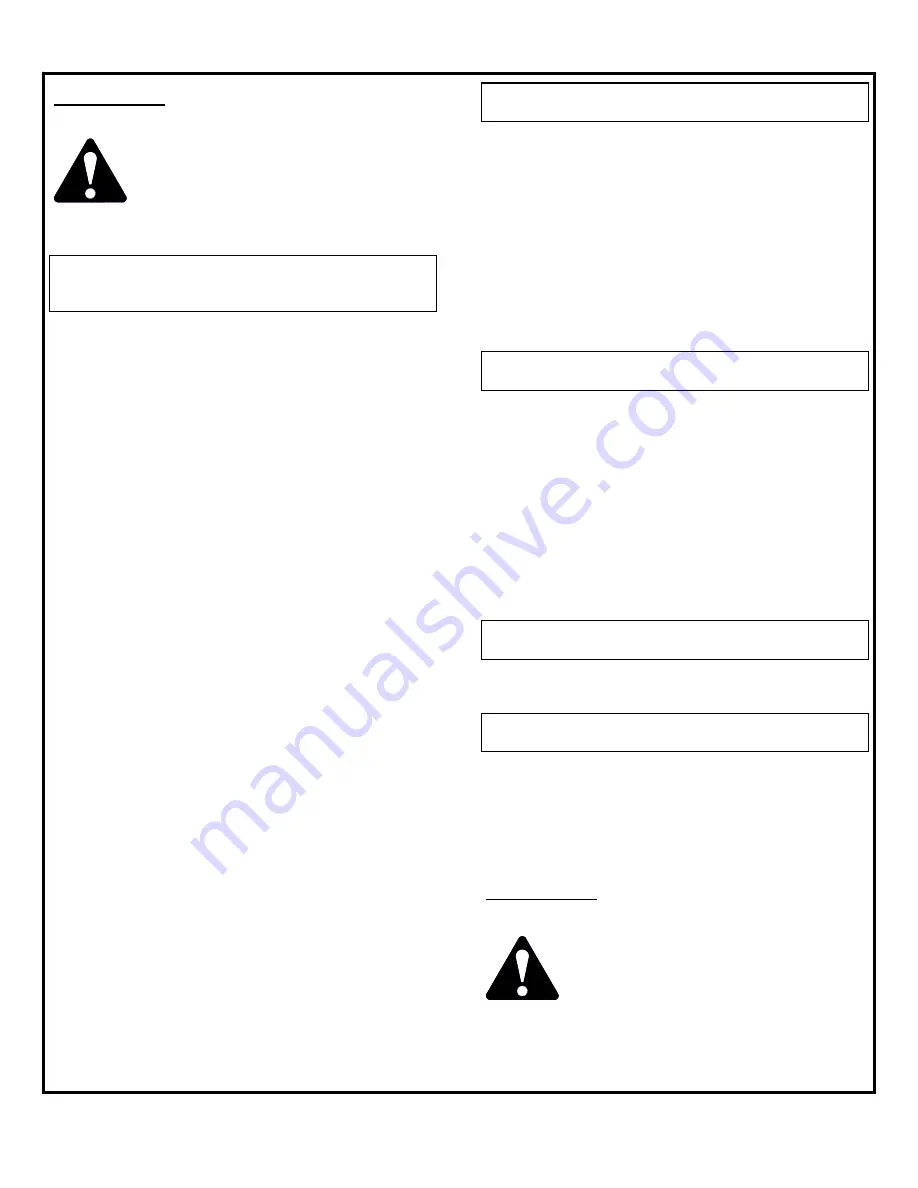
4
SAFETY INSTRUCTIONS
WORK SAFELY - A CAREFUL OPERATOR IS THE BEST INSURANCE AGAINST ACCIDENTS !!
SECTION 1 (CONTINUED)
WARNING
Obey all the safety instructions listed in
this section and throughout this manual.
Failure to obey instructions in this
section could result in death or serious
injury.
WHEN DEALING WITH HYDRAULICS DURING ANY
TYPE OF ASSEMBLY, OPERATION, MAINTENANCE,
OR OTHER WORK ON OR NEAR THIS PRODUCT:
•
Hydraulic fluid under pressure can penetrate the
skin and cause serious injury or death. Hydraulic
leaks under pressure may not be visible!
•
If any fluid penetrates the skin, GET IMMEDIATE
MEDICAL ATTENTION!!
•
Wear safety glasses, protective clothing, and use a
sound piece of cardboard or wood when searching
for hydraulic leaks. DO NOT USE YOUR HANDS!
•
Before connecting or disconnecting hydraulic hoses,
read your power unit’s operator’s manual for detailed
instructions on connecting and disconnecting
hydraulic attachments.
•
Make certain that all parts meet the specifications for
this product when installing or replacing hydraulic
hoses or fittings.
•
After connecting hydraulic lines:
•
Slowly and carefully raise the loader and cycle
the rollback / dump cylinders to check hose
clearances and to check for any interference.
•
Operate the hydraulics on this product to check
hose clearances and to check for any
interference.
•
Make certain that the hoses cannot interfere
with or actuate the quick-attach mechanism.
•
Make certain that hoses will not be pinched, or
get tangled, in any equipment.
•
Do not lock the auxiliary hydraulics of your power
unit in the “ON” position.
•
Refer to your power unit’s operator’s manual and
this manual for procedures and intervals, then
inspect and maintain the entire hydraulic system to
insure that the fluid remains clean, that all devices
function properly, and that there are no fluid leaks.
WHEN MOUNTING THIS PRODUCT TO YOUR
POWER UNIT:
•
Refer to the operator’s manuals of your power unit,
your loader, and your quick-attach for special or
detailed mounting instructions.
•
This product should fit onto the quick-attach or
loader arms of your power unit the same as the
original products that were designed by your loader /
quick-attach manufacturer.
•
If this product does not fit properly, contact FFC
Attachments before operating.
•
Never place your finger into the mounting plate or
loader holes. A slight movement of the power unit or
this product could cause serious injury.
BEFORE EACH USE, THOROUGHLY INSPECT THIS
PRODUCT AND:
•
Make certain that all safety signs are in place and
legible. Refer to the safety sign page in this manual
for the placement of safety signs for this product.
•
Replace all damaged or excessively worn parts and
hardware only with genuine FFC Attachments parts
or with properly rated fasteners, hydraulic hoses, or
fittings.
•
Make certain that all locking pins, latches, and
connection devices are properly installed and
secured.
•
Make certain that all protective guards, canopies,
doors, etc. are in place and secure.
WHEN OPERATING THIS PRODUCT IN
ACCORDANCE WITH DESIGN INTENTIONS:
•
Keep everyone at least nine feet away from the unit
when operating.
WHEN ADJUSTING, SERVICING OR REPAIRING
THIS PRODUCT:
•
Make no modifications to your Preparator
®
.
•
When making repairs, use only genuine FFC
Attachments parts or, for fasteners, hydraulic hoses,
or hydraulic fittings, use only properly rated parts.
•
Replacement parts, for parts with safety signs
attached, must also have safety signs attached.
SECTION 2
CAUTION
Obey all the safety instructions listed in
this section and throughout this manual.
Failure to obey instructions in this
section may result in personal injury.
•
Do not use the top of this product as a step. Under
certain conditions, this area can be slippery.
Summary of Contents for FFC LAF3554
Page 2: ......
Page 17: ...15 PARTS ILLUSTRATION...