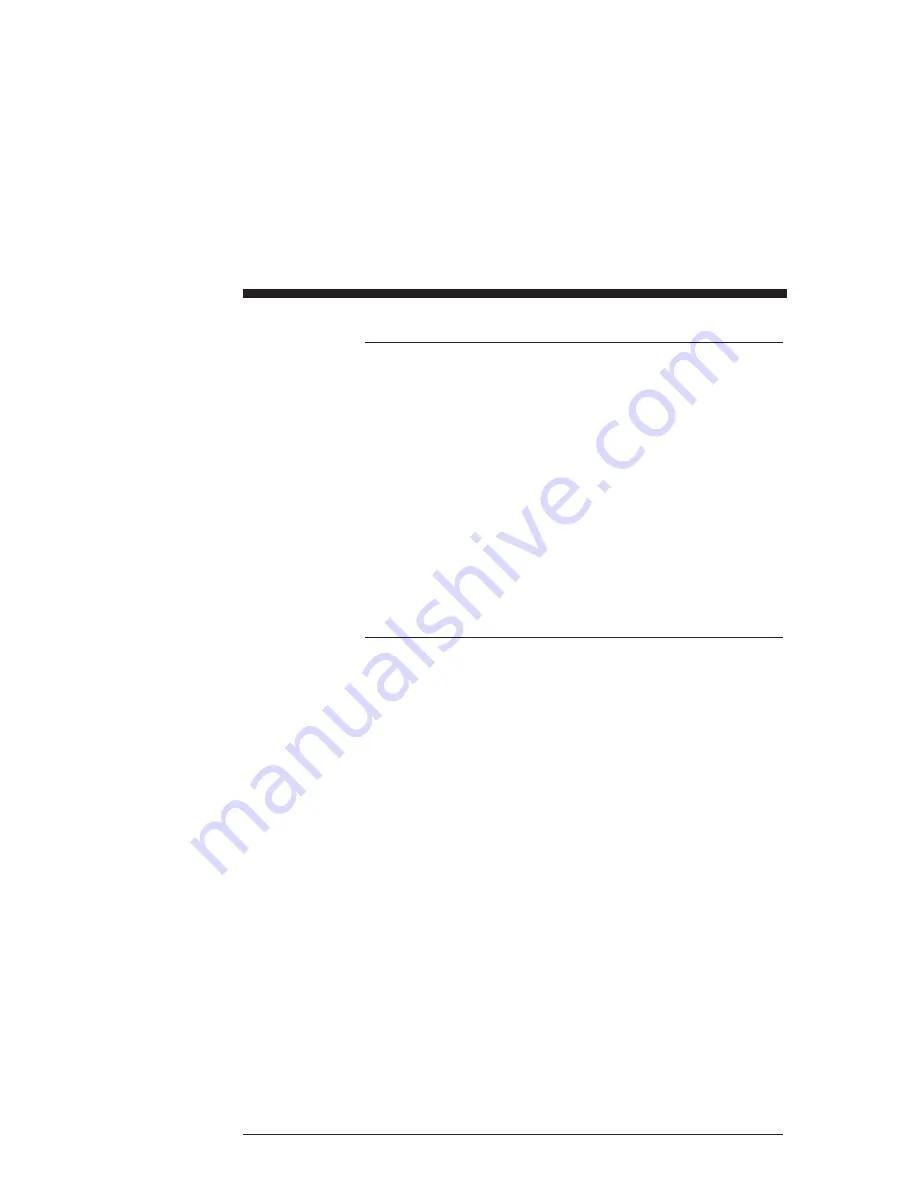
950IDE can also be used to make the calculation. Simply enter
the inertia ratio and 950IDE will calculate the appropriate value
for
KVP
to achieve 25, 75 or 180 Hz bandwidth depending upon
the choice made for system response.
There is no specific answer to the general question “What should
the bandwidth be?” In general, the higher the velocity loop
bandwidth, the faster the settling time will be and the better the
rejection of torque disturbances (increased stiffness). Typically,
velocity loop bandwidths range from 30 to 100 Hz. However, too
high a bandwidth can lower the damping of resonance in
mechanical linkages, causing excessive ringing and/or wear in
coupled mechanics. Remember, it is the resulting motion at the
end of any mechanical linkages that typically matters, not the
response at the motor shaft.
Problems with
high load inertia
It would seem from the above that setting
KVP
is simply a matter
of increasing its value to compensate for load inertia.
Unfortunately, the following problems often interfere, particularly
when the load inertia is large compared with the motor’s inertia:
1. Mechanical resonance between motor and load cause high
frequency oscillation.
2. Backlash between motor and load effectively unload the
motor over a small angle. Within this small angle the
increased bandwidth results in oscillations.
3. Ripple in the velocity feedback signal results in large motor
ripple current if
KVP
is large.
As a general rule, any system with
KVP
set higher than 5 times
the medium bandwidth setting will require adjustment to the
default
ARF0
and
ARF1
settings.
4 - 4
MA950