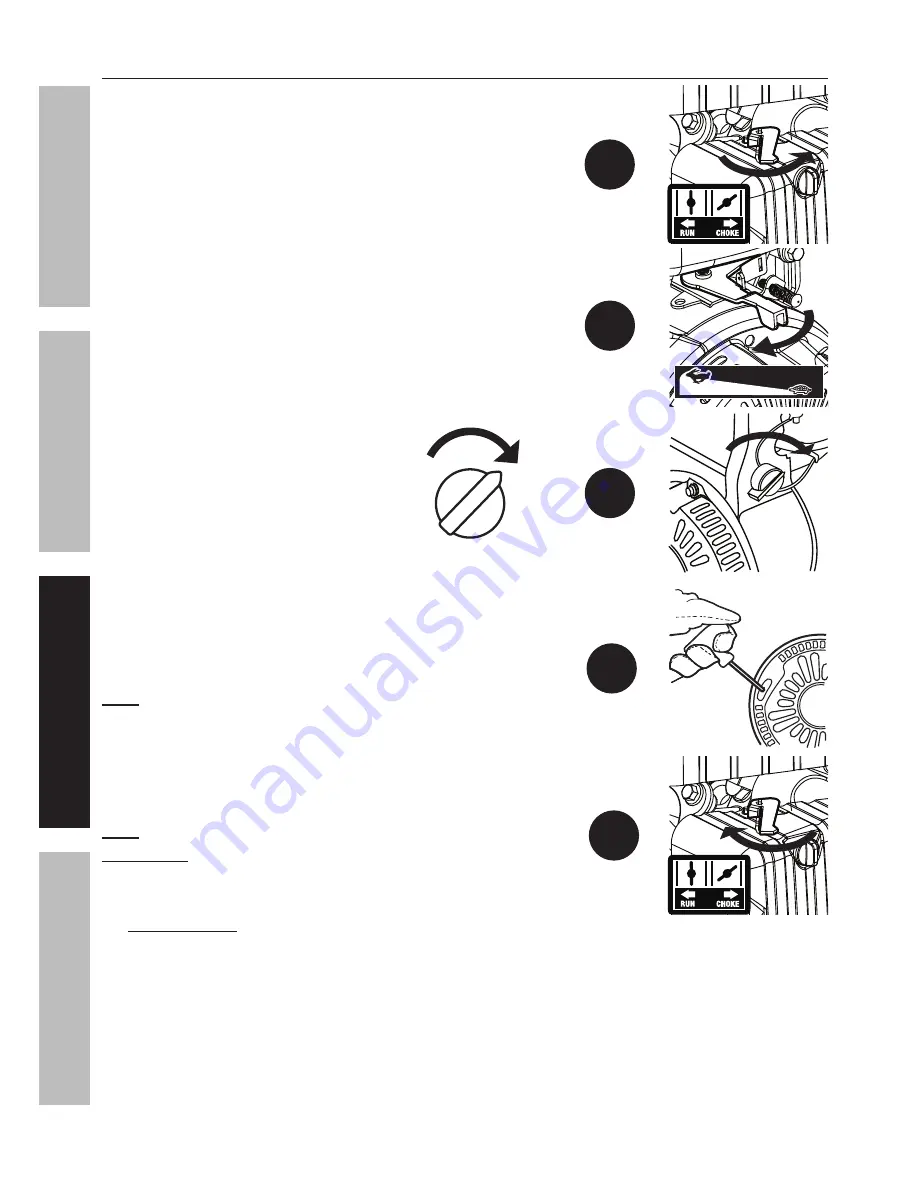
Page 12
For Pump technical questions, please call 1-888-866-5797.
For Engine technical questions, please call 1-800-520-0882.
ITEM 69747
SAFETY
O
PERA
TION
M
AINTENANCE
SETUP
Manual Start
1. To start a cold engine, move the Choke to the
CHOKE position.
To restart a warm engine, leave the
Choke in the RUN position.
2. Slide the Throttle or Speed Control Lever to 1/3 away
from the SLOW position (the “turtle”).
3. Turn the Engine Switch on.
4. Grip the Starter Handle of the Engine loosely and pull
it slowly several times to allow the gasoline to flow into
the Engine’s carburetor. Then pull the Starter Handle
gently until resistance is felt. Allow Cable to retract fully
and then pull it quickly. Repeat until the engine starts.
Note:
Do not let the Starter Handle snap back against the engine.
Hold it as it recoils so it doesn't hit the engine.
5. Allow the Engine to run for several seconds.
Then, if the Choke lever is in the CHOKE position,
move the Choke Lever very slowly to its RUN position.
Note:
Moving the Choke Lever too fast could stall the engine.
IMPORTANT:
Allow the engine to run at no load for five minutes with no
load after each start-up so that the engine can stabilize.
6. Adjust the Throttle as needed.
7.
Break-in Period:
a. Breaking-in the engine will help to ensure proper equipment and engine operation.
b. The operational break-in period will last about 3 hours of use. During this period:
• Do not apply a heavy load to the equipment.
• Do not operate the engine at its maximum speed.
c. The maintenance break-in period will last about 20 hours of use. After this period:
• Change the engine oil.
Under normal operating conditions subsequent maintenance follows the schedule
explained in the MAINTENANCE AND SERVICING section.
1
2
ON
OFF
O
I
ON
3
4
5
Summary of Contents for 69747
Page 1: ......