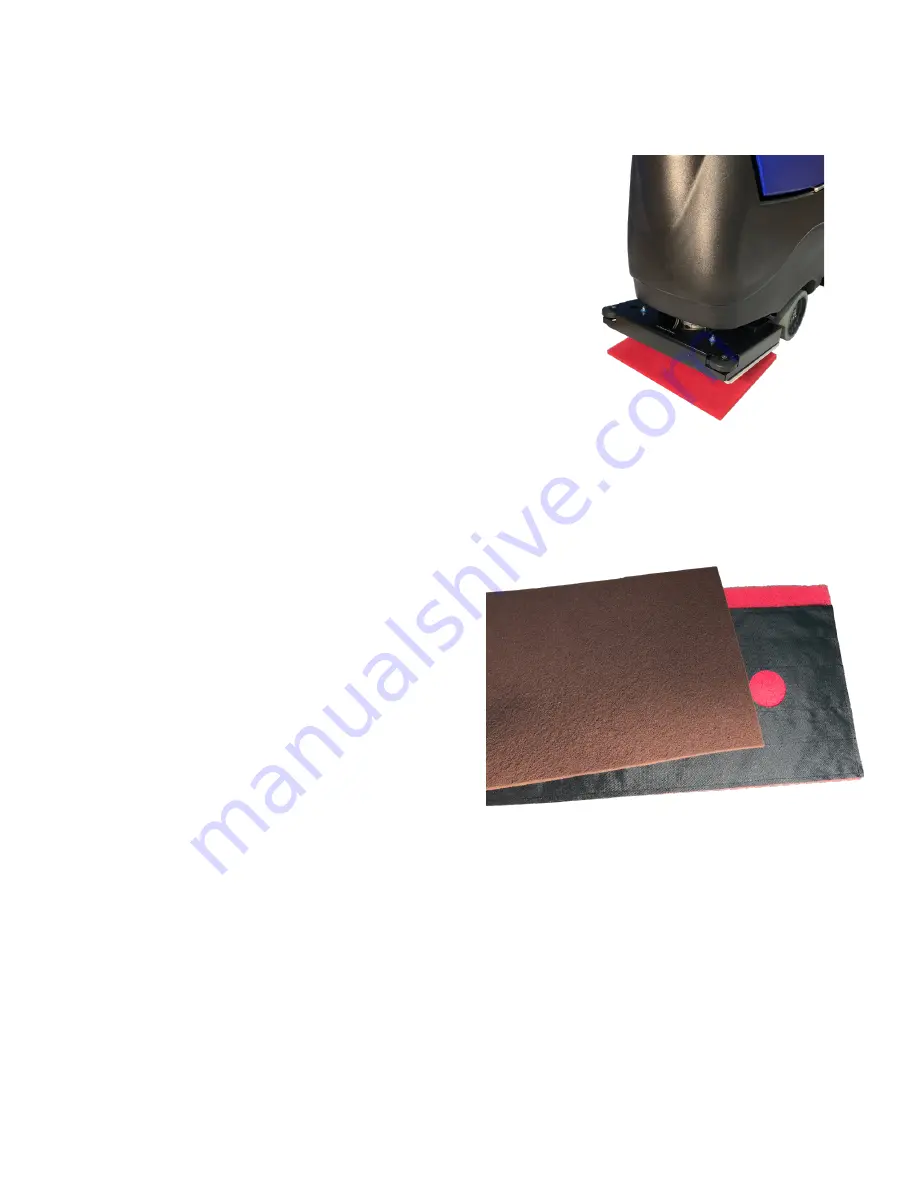
- 18 -
ORBITAL PADS & CHEMICAL-FREE FINISH REMOVAL (CFR)
NOTE
: Do not operate the Orbital Scrub Head without a pad installed. Operating the head without a pad will damage the
Mighty-Lok
®
face.
STANDARD OPERATION
1. Align the corners of the pad to the corners of the aluminum plate with
Mighty-Lok
®
face and press to attach.
2. Lower the scrub deck onto the pad.
3. Ensure the pad is properly aligned front-to-back and right-to-left. Water
should drip directly onto the top of the pad.
CHEMICAL-FREE FINISH REMOVAL (CFR) PAD ASSEMBLY & OPERATION
In addition to the traditional cleaning pad, a specialized surface preparation pad is required for chemical-free finish removal. The
standard red scrub pad acts as a “backer” and compensates for variances in the floor.
1. Place the black retainer pad 2” back from the front of the red
scrub pad.
2. Align the maroon CFR pad with the red scrub pad.
3. Ensure the pads are aligned so that the black pad is justified
towards the back of the machine, so that the gap described in Step
1 is towards the front of the machine.
4. Install the pads in accordance with the instructions above for
standard operation.
5. Fill the Solution Tank with clean water.
6. Set the Solution Flow to the medium setting. Adjust as needed
to obtain the optimum finish removal using the least amount of
water for effective rinsing.
7. Set the Speed Control to the medium setting.
8. Lower the Scrub Head to the Heavy Down Pressure setting.
Summary of Contents for S-24
Page 5: ...PAGE INTENTIONALLY BLANK ...
Page 48: ...RETURN TO TABLE OF CONTENTS 43 FRAME ASSEMBLY ...
Page 52: ...RETURN TO TABLE OF CONTENTS 47 SOLUTION TANK ...
Page 54: ...RETURN TO TABLE OF CONTENTS 49 OPTIONAL CHEMICAL INJECTION SYSTEM ...
Page 64: ...RETURN TO TABLE OF CONTENTS 59 S 24 DISK SCRUB HEAD ...
Page 66: ...RETURN TO TABLE OF CONTENTS 61 S 24 DISK SCRUB HEAD ...
Page 79: ...RETURN TO TABLE OF CONTENTS 74 PAGE INTENTIONALLY BLANK ...
Page 85: ...RETURN TO TABLE OF CONTENTS 80 OPTIONAL CHEMICAL INJECTION SYSTEM ...
Page 86: ...RETURN TO TABLE OF CONTENTS 81 OPTIONAL SCRUBSMART TELEMETRY SYSTEM ...
Page 87: ...RETURN TO TABLE OF CONTENTS 82 PAGE INTENTIONALLY BLANK ...
Page 88: ...RETURN TO TABLE OF CONTENTS 83 DATE MAINTENANCE LOG ...
Page 89: ...RETURN TO TABLE OF CONTENTS 84 DATE MAINTENANCE LOG ...
Page 91: ...RETURN TO TABLE OF CONTENTS 86 PAGE INTENTIONALLY BLANK ...
Page 92: ...www pacificfloorcare com ...