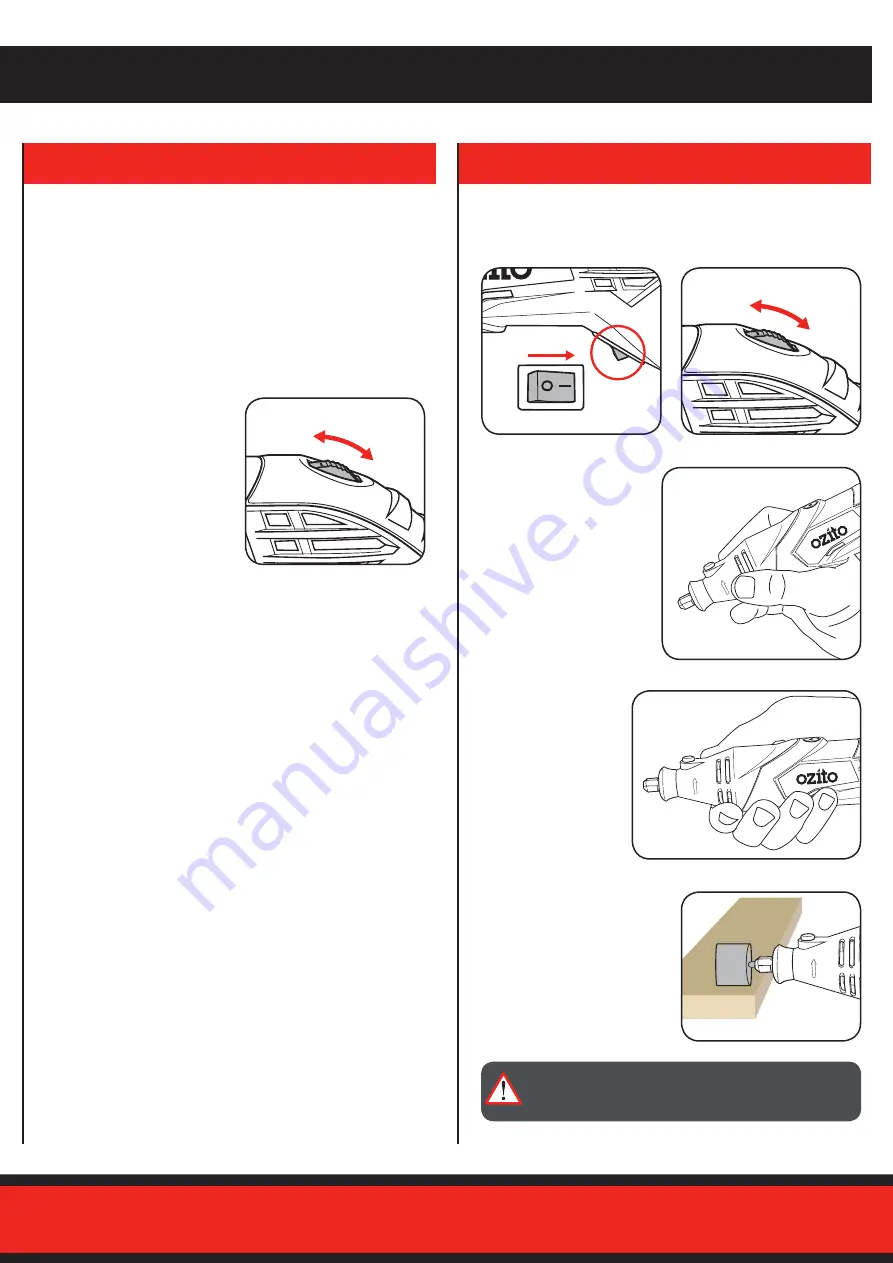
RTR-4100
6. CONTROLS
7. OPERATING THE ROTARY TOOL
The speed of the tool can be regulated to suit a variety of applications
and materials.
Low speed use:
Best for polishing applications and delicate projects
such as fragile model parts. It is recommended that the various shape
grinding stones be used at low speed to prevent them from becoming
too hot and deteriorating.
High speed use:
Best for carving and shaping materials. Metal and
glass projects require high speed drilling.
1 Rotate the variable speed dial
to select the desired speed.
Note:
The higher the number on
the variable speed dial, the faster
the speed of the rotary tool.
Variable Speed Dial
1 Ensure the workpiece is
securely clamped down and
then turn the rotary tool on.
2 Select the appropriate speed
for the application.
3 For high precision
applications such as
engraving or milling, hold
the rotary tool like a pen.
5 Gently apply the tip of the
accessory to the work piece.
4 For heavy work like
cutting or grinding,
hold the rotary tool
in the palm of your
hand.
WARNING!
PLACING EXCESSIVE LOAD ON THE ROTARY
TOOL WHILE IT IS RUNNING AT LOW SPEEDS MAY
CAUSE IT TO OVERHEAT AND THE MOTOR TO FAIL.