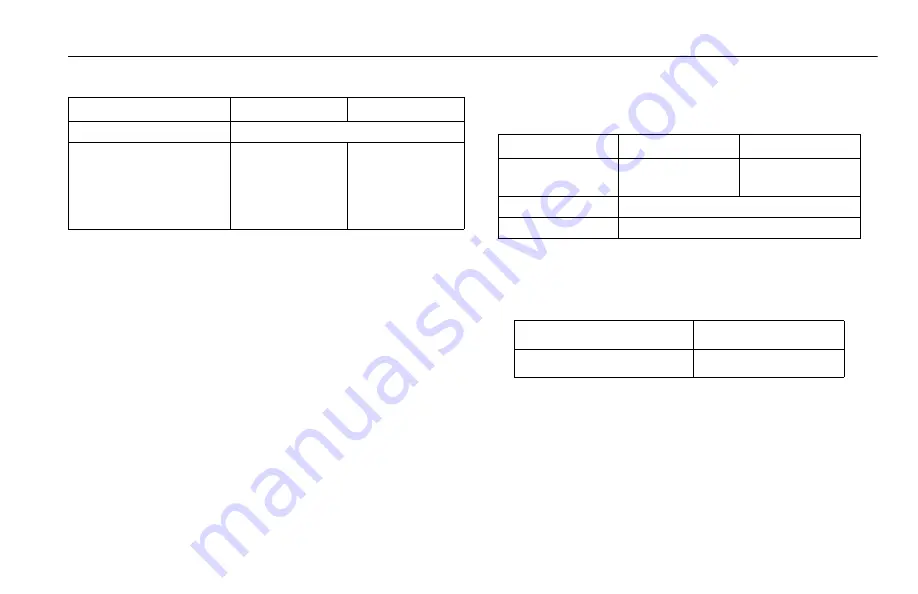
SECTION 6 - GENERAL SPECIFICATIONS AND OPERATOR MAINTENANCE
3121132
– JLG Lift –
6-3
Dimensional Data
Capacities
Outside Turning Radius
20 ft 1 in (6.12 m)
Gross Vehicle Weight w/ One
Extension
Note: Certain options or coun-
try
standards increase weight
11,910 lbs
(5,402 kg)
15,300 lbs
(6,940 kg)
Table 6-1. Operating Specifications
Model
3394RT
4394RT
Table 6-2. Dimensional Data
3394RT
4394RT
Machine Height
(rails down)
61.75 in (1.6 m)
70.4 in (1.8 m)
Machine Width
7ft 10in (2.4 m)
Machine Length
13 ft (4 m)
Table 6-3. Capacities
Fuel Tank
31.5 gal (119 l)
Hydraulic Tank
40 gal (151 l)