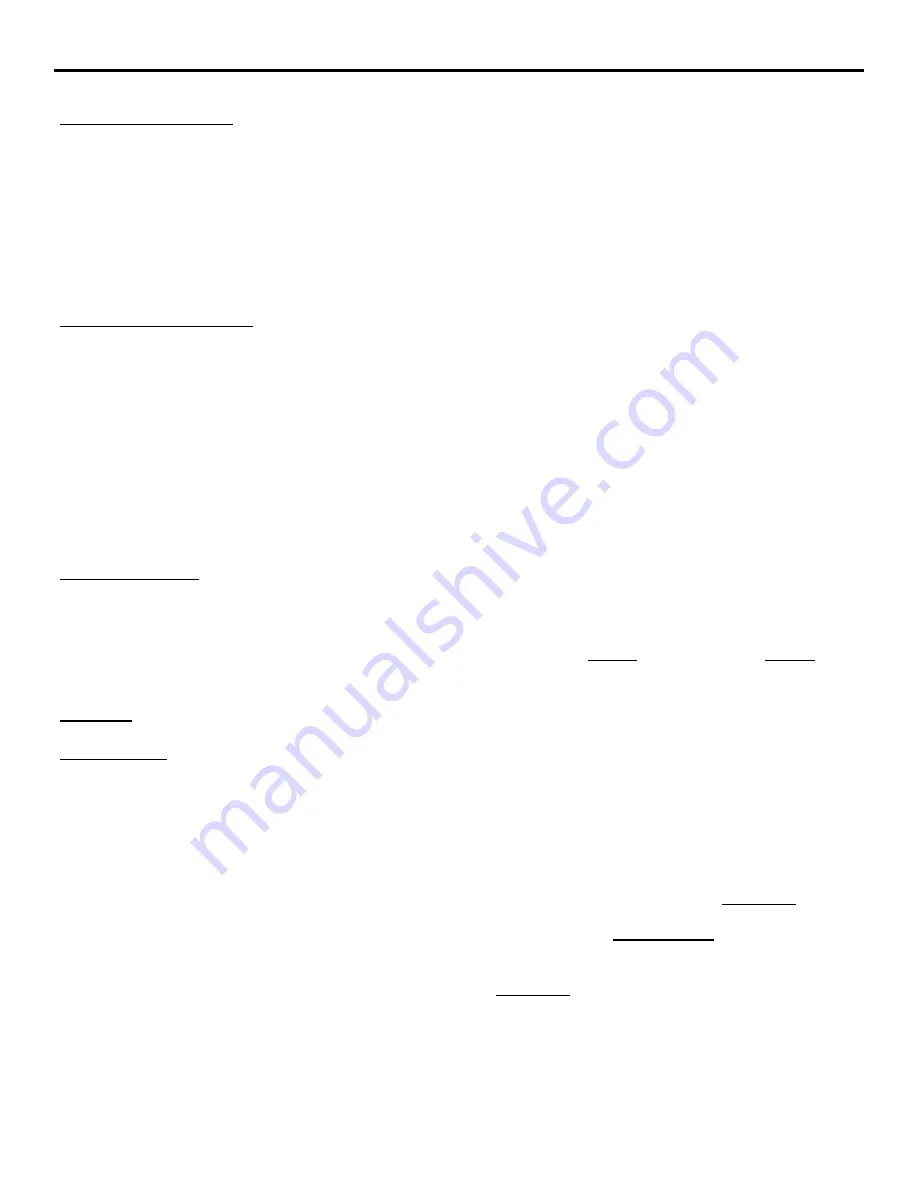
/20
4. Maintenance
4.1 Maintenance Safety
Turn off the gas to the main burner and allow the heater to cool before servicing
.
Service and repair should be
done by a qualified service person. A professional service technician should inspect the appliance before use
and at least annually. More frequent cleaning may be required due to excessive lint from carpeting, bedding
material, etc. It is important that the access door and circulating air passageways be kept clean to provide for
adequate cooling airflow. Do not substitute materials or use components other than factory supplied.
4.2 Recommended Service
1. Examine the venting system periodically.
2. Visually check the burner and pilot flame periodically (See Section 3.10.2 and Figure 3.12).
3. Visually check height and colour of flame periodically (See Section 3.10.3 and Figure 3.13).
4. Clean the glass as needed. See section 4.3 for instructions on glass cleaning.
3. Have the appliance inspected annually by a professional service technician.
5. Clean the appliance periodically and as required.
4.3 Glass Cleaning
The inside of the glass may require periodic cleaning to remove deposits left from impurities in the gas and
combustion air. For best results, use a ceramic glass cleaner or polish. A suitable cleaner is available from
your dealer. Avoid the use of ammonia based cleaners such as Windex.
Do not
clean while hot.
Do not
use
abrasive cleaners.
C
AUTION
: Be careful not to abuse the glass door, such as by striking or slamming it shut.
Door Removal
1. Ensure that the unit has cooled down.
2. Remove any door trim pieces as required. Most installations will be equipped with door trim pieces,
which are magnetically affixed to the doorframe. These pieces may be removed without any
mechanical aids.
3. Remove the top louvre assembly by lifting the assembly upwards and then out; (see Figure 4.1).
4. Release the door latches by pressing down on the individual toggles.
P
LEASE
N
OTE
:
The latches are
under tension – care should be taken when releasing them
.
5. Rotate the top of the door outwards, and lift out (see Figure 4.2).
6. Handle the door very carefully and set it
in
a safe place
, away from traffic areas.
7. Re-install in reverse order.
Summary of Contents for Designer DV36
Page 6: ...0...
Page 27: ...21 Figure 4 1 Top Louvre Assembly Removal Figure 4 2 Glass Door Removal...
Page 46: ...40 9 Label Information...