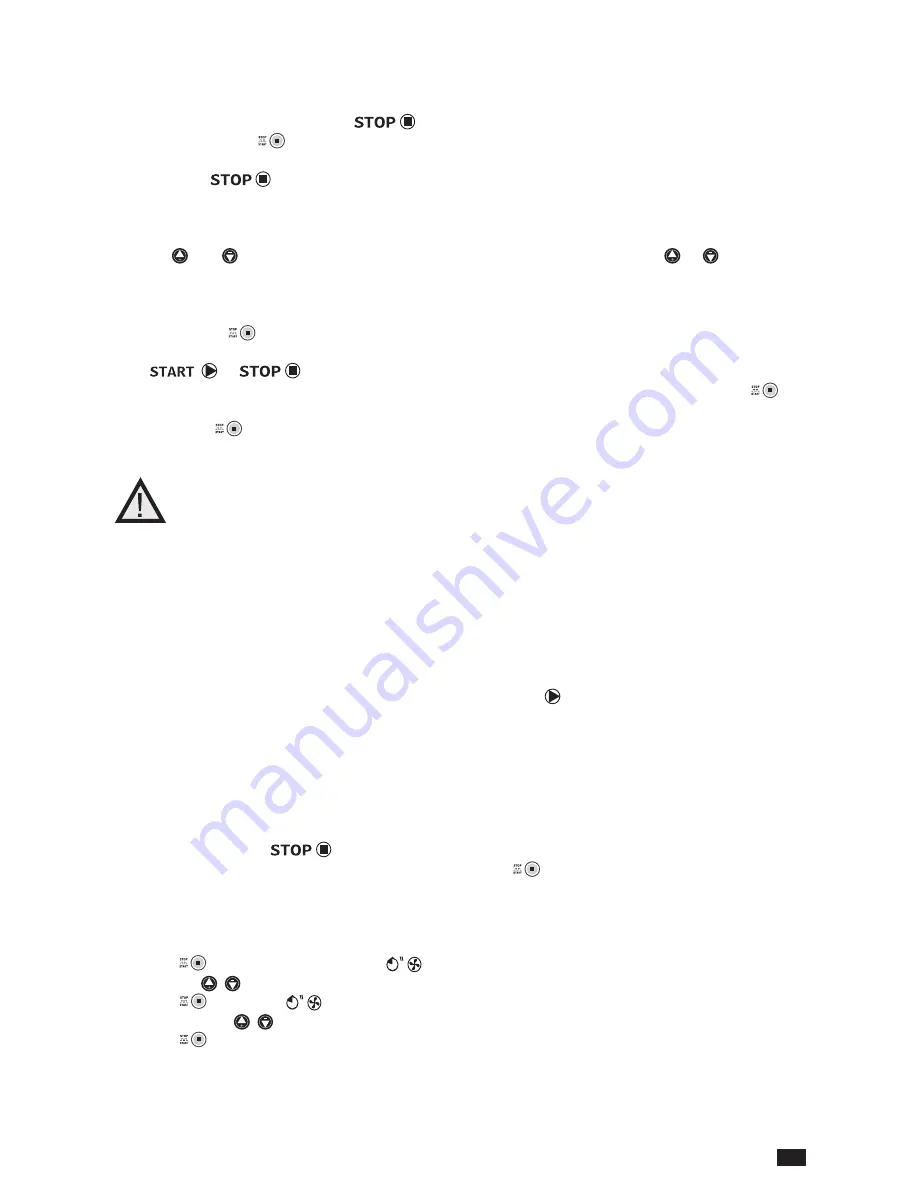
5
Operation description
After switching on, controller is in
, which is signaled by adequate diode. Operation
starts after pressing
or automatically, when boiler’s temperature increases above operating
threshold – temperature difference between set temperature and DT parameter set in the service
menu. Status
is automatically activated after 30 minutes since temperature decrease
below operating threshold. CONTROL socket which is located at the back panel of the controller
is for connection of remote control EKOSTER CONTROL.
Buttons and
are for setting's changes. During boiler operation, pressing
or causes
possibility to change desired boiler’s temperature. Pressing and withholding button causes
increase of speed of temperature changing.
Pressing button
causes:
• temperature below operating threshold:turning on/off of the controller signaled with diodes
or
,
• at temperature above operating threshold:fan operation blockade signaled by blinking
, diode, which makes possible to stoke the boiler. Return to automatic operation after
pressing
button.
ATTENTION!
Displaying „Er” on the controller informs about temperature increase above 99 °C,
below -9 °C or boiler sensor damage. To secure the boiler till sensor replacement,
pump will be automatically activated.
COMFORT SYSTEM
COMFORT SYSTEM function in controller prevents pump’s rotor from stone deposition.
Controller automatically activates pump after heating season for 30 seconds every 14 days.
Pump operation in this mode is signaled with flashing
PUMP
diode. Function activates after 1
minute since controller’s activation. Pump activation in this mode causes that 14 days period is
counted from the beginning.
Freezing and overheating function
Controller enables to turn on circulation pump In case if temperature drops to 4 °C or lower.
Exceeding 97°C causes fan to turn off and circulation pump activation. Boiler overheating is
signaled with flashing
diode. In such a case it is recommended to determine cause
of overheating, eliminate and turn on the boiler pressing
button. Pump is activated
permanently In case of boiler sensor damage.
Blow-through
• Press
and hold for 3 s till diode
starts blinking,
• Buttons , are for blow-through time setting in seconds,
•
Press
dtill diode
starts blinking,
• With buttons , set blow- through pause in minutes,
•
Press
.
From now on controller at temperatures higher than set one will activate blow-through.
Summary of Contents for ORLAN SUPER 130 kW
Page 1: ...ORLAN SUPER 130 kW INSTRUCTION MANUAL SERVICE MANUAL ...
Page 25: ...18 2 3 EKOSTER 2 electric scheme ...
Page 32: ...25 ...
Page 33: ......
Page 34: ......