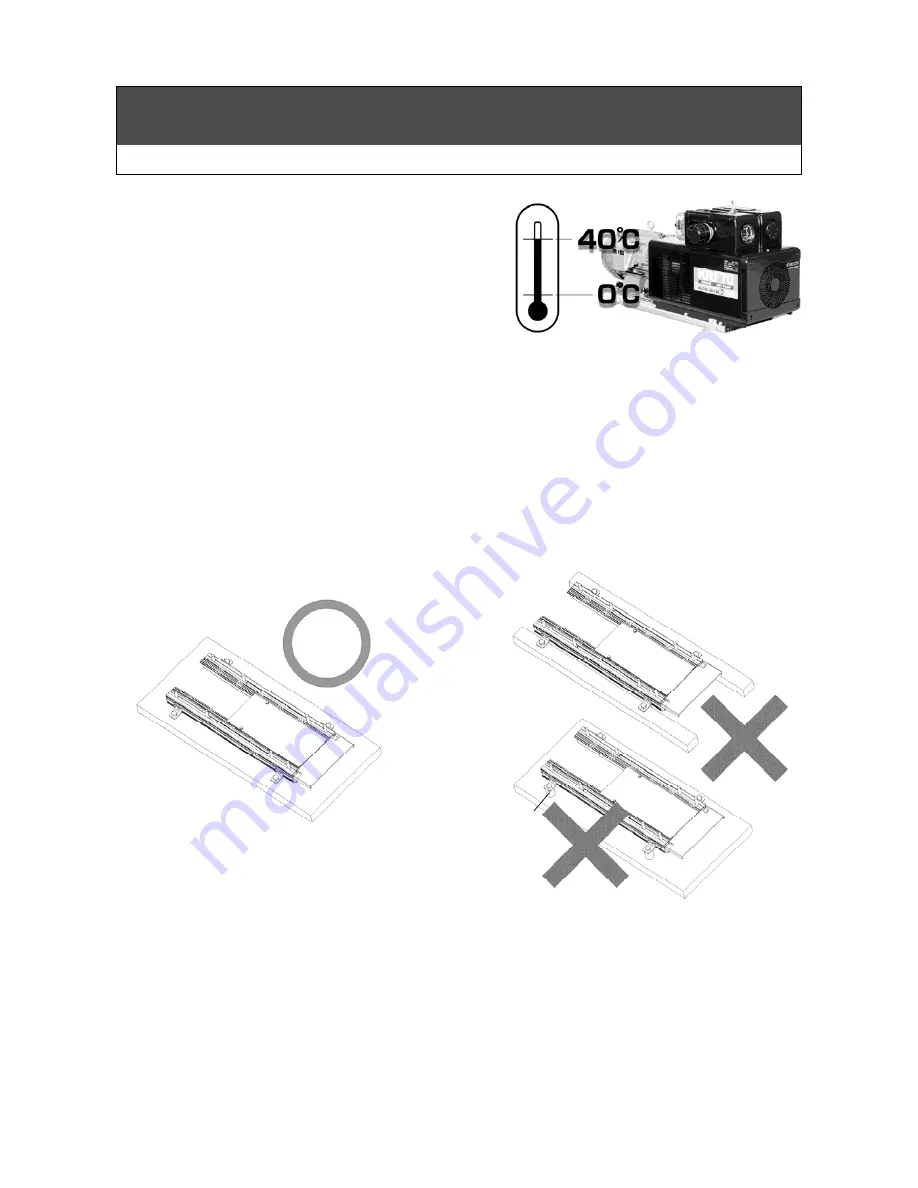
6
Precautions for Proper Operation
■
For inlet air, aim at normal temperature and normal
humidity clean air with little dust but free from
corrosive and explosive gases.
※
Normal temperature: 0 to 40 deg. C
※
Normal humidity: 65% +/- 20% (JIS Z 8703)
■
Prohibition of operation in reverse rotation.
■
Set the ambient temperature of the dry pump to the
range of 0 to 40 degrees C.
Try not to cause condensation inside the pump.
■
Keep the pump away from oil, water, dust, rain, etc.
Also, never lubricate the product.
■
Be sure to use under specified pressure or less.
■
Do not remove the main cover, and top and bottom partition plates. Removing these cover and plates
may result in shortening the life of product severely due to the temperature rise.
■
Install the product on a flat surface..
■
Periodically replace consumable parts (see pages 20) and replacement parts (see page 21).
■
Be sure to Install the product on the level while whole base is touching on the level surface like in
figure A.
※
do not Install the product like in figure B.
Fig.A
Fig.B
Cushion rubber etc
Summary of Contents for KRF110
Page 28: ...26 Dimensional Outline Drawing KRF70 V 01 04 KRF70 VH 01 04 unit mm...
Page 29: ...27 Dimensional Outline Drawing KRF70 B 01 04 KRF70 BH 01 04 unit mm...
Page 30: ...28 Dimensional Outline Drawing KRF70 VB 01 04 KRF70 VBH 01 04 unit mm...
Page 31: ...29 Dimensional Outline Drawing KRF110 V 01 04 unit mm...
Page 32: ...30 Dimensional Outline Drawing KRF110 B 01 04 unit mm...
Page 33: ...31 Dimensional Outline Drawing KRF110 VB 01 04 unit mm...
Page 34: ...37 memo...
Page 35: ...37 memo...
Page 36: ...K No 0322 12 2 1 C DG TY...