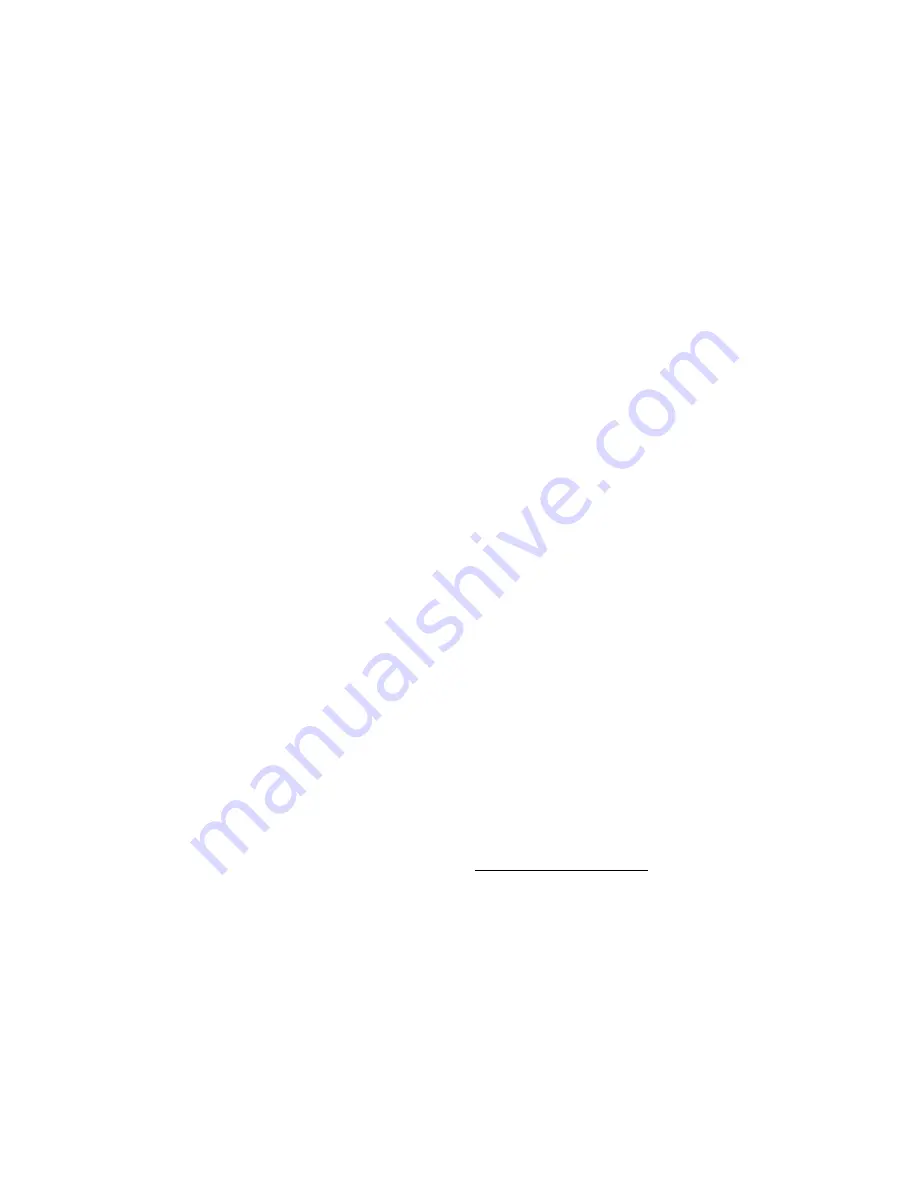
13
MACHINE MAINTENANCE
All general information about machine maintenance is based on
normal machine working conditions: indoor, moderate dust and low
moisture environment, and maximum rotation of 32 RPM of
turntable/rotary arm. They should be regarded as guidelines,
reviewed and corrected according to requirements of actual use
and conditions.
MOTOR MAINTENANCE
An occasional inspection of the brushes should be made in order to
establish a wear rate. Replacement brushes should be installed
before old brushes wear to 9/16” long, measured on the long side.
After replacing brushes run the motor near rated speed for at least
l/2 hour with no load to seat the new brushes. Failure to properly
seat the new brushes may cause commutator damage and rapid
wear of the new brushes. If the commutator becomes rough,
scored or out of shape, a competent motor shop should
disassemble it and resurface the commutator. With every third
brush change, have a competent motor shop resurface the
commutator and blow the carbon dust out of the motor.
REDUCER OIL CHANGE
All external cap screws and plugs on the reducing transmission
should be checked for tightness after the first week. It is
recommended to change the oil every six months or at least 1800
hours of operation, whichever comes first. When adding or
changing oil, the transmission should never be filled above the oil
level mark indicated, because leakage and overheating may occur.
Below is the list of the type of lubricant that should be used. List of
recommended reducer oils:
Manufacturer Lubricant
American Oil Co. American Cyl Oil no: 196-L
Cities Service Oil Co. Citgo Cyl Oil 100-5
Gulf Oil Corp. Gulf Senate 155
Mobil Oil Corp. Mobil 600 W Suer-r Cyl. Oil
Philips Oil Corp. Andes S 180
Texaco Inc. 624 + 650T Cyl.Oil
Shell Oil Co. Velvata Oil J82
Union Oil of Cal. Red Line Worm Gear Lube 140
RING BEARING MAINTENANCE (when applicable)
The ring bearing (located under the turntable) should be re-
lubricated internally and externally.
Internally
: by injecting grease into all the lubrication nipples in
succession until a collar of fresh grease appears around the
perimeter of the ring. The re-lubrication interval suggested for these
bearings, used in Stretch Wrapping Machinery is 750 hours, with a
maximum period of 6 months. The lubricant should be fresh and
applied in sufficient quantities to make sure all surfaces are
lubricated.
Externally
: by lubricating and wiping the chain drive with oily cloth.
The frequency of lubrication depends on entirely upon the usage of
the machine and environment in which the machine is placed (dust,
moisture etc.). Machines working under extremely dirty conditions
should be lubricated every 400 operating hours but at minimum,
every 2 months. Longer lubrication intervals may occur only when
machine is working under very clean and dry conditions but should
be not be longer than 6 months.
List of recommended lubricants for the ring bearing lubrication
Manufacturer Lubricant
BP Energrease LS2
Castrol Speeroll AP2
Esso Beacon 2
Gulf Crown Grease 2
Mobil Mobilus 2
Shell Avania Grease R2
Texaco Glissando FT 2
Valvoline LB-2
TOWER RACEWAYS MAINTENANCE
The film distributor (carriage) is sliding on the plastic guides
attached behind its back plate. The section of the tower on which
the plastic guides move (raceways) should be cleaned and re-
greased approximately every 600 hours of machine operation.
NOTICE: If the machine works in a dusty and corrosive
environment, the raceways should be re-greased more often (at
least every 100 hours).
CHAIN MAINTENANCE
To clean the chain, wipe it with an oily cloth every month. When
machine is working in a dusty and damp environment, it may be
necessary to repeat the cleaning operation more often. As the
chain lubricants please use the most common chain lubricants on
the market. With time, the chain will tend to stretch. A loose tower
chain should be tightened by moving the reducer on its mounting
plate. Turntable is equipped with automatic chain tensionner and
does not need any adjustement.
NOTICE: First chain tension inspection must be done after the first
two weeks of machine usage.
CAM FOLLOWER MAINTENANCE (when applicable)
The cam followers have deep grease pockets and do not need
frequent relubrication. The portion of the tower on which the cam
followers run, should be cleaned and regreased every 300 hours of
operation. If the machine operates in a dusty or corrosive
environment the tower should be relubricated more often.
Summary of Contents for 2007-8899999
Page 6: ...6...
Page 7: ...7 Note For VFD adjustment please contact Orion Packaging service department...
Page 8: ...8...
Page 15: ...15...
Page 16: ...16...
Page 17: ...17...
Page 18: ...18...
Page 19: ...19...
Page 20: ...20...
Page 21: ...21...
Page 22: ...22...
Page 23: ...23...
Page 24: ...24...
Page 25: ...25...
Page 26: ...26...