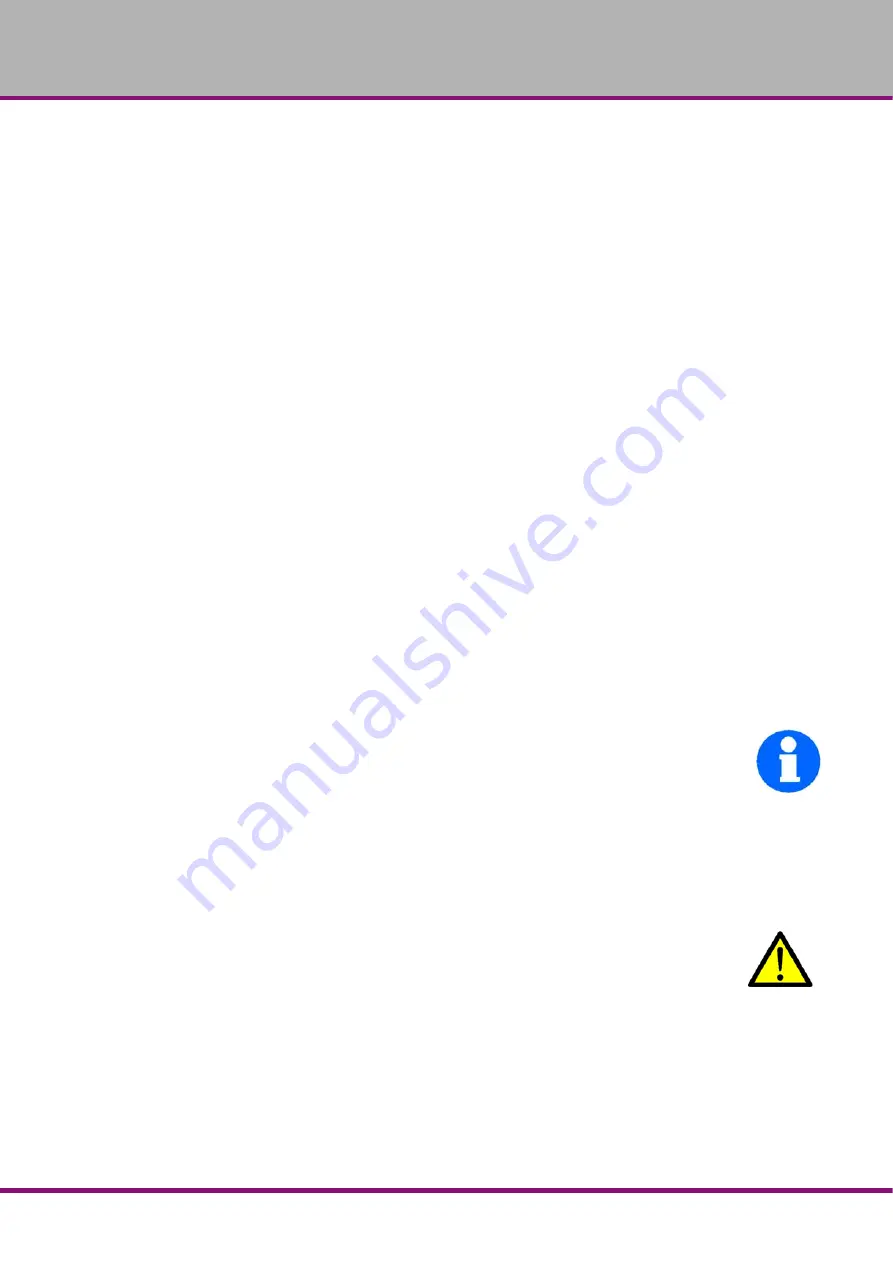
OPTIMUM
M A S C H I N E N - G E R M A N Y
Safety
Version 1.0.3 dated July 22, 2014
Page 9
Original operating instructions
B30 VGM
US
Use of cooling and lubricating agents in order to increase the durability of the tool and to
improve the surface quality.
Clamp the cutting tools and the workpieces on clean clamping surfaces.
Sufficiently lubricate the machine.
Correctly set the bearing clearance and guidance.
It is recommended to:
Use the drill in a way that it is exactly located between the three clamping jaws of the quick
action chuck.
When drilling, please observe that
It is necessary to set the suitable speed depending on the diameter of the drill,
The press-on must only be as intense that the drill can cut on no-load,
If the press-on is too intense, it might result in early tool wear perhaps even tool fracture
resp. jamming in the drill hole. If the tool gets jammed, immediately stop the main drive
motor by actuating the emergency-stop button,
For hard materials, e.g. steel, it is necessary to use commercial cooling/lubricating agents,
Generally always back out the tool from the workpiece while the shaft is turning.
1.4
Possible dangers caused by the geared drill
The geared drill is carried out with the latest technological advances.
Nonetheless, there remains a residual risk, since the geared drill operates with
high revolutions,
rotating parts,
electrical voltage and currents.
We have used construction resources and safety techniques to minimise the health risk to per-
sonnel resulting from these hazards.
If the geared drill is used by personnel who are not duly qualified, there may be a risk resulting
from incorrect operation or unsuitable maintenance.
INFORMATION
All personnel involved in assembly, commissioning, operation and maintenance must
be duly qualified,
follow this instruction manual.
Due to improper use
there may be a risk to personnel,
there may be a risk to machine and other items,
correct functioning of the geared drill may be affected.
Disconnect the geared drill whenever cleaning or maintenance work is being carried out.
WARNING!
The geared drill may only be used with the safety devices activated.
Disconnect the geared drill whenever you detect a failure in the safety devices or when
they are not fitted!
All additional installations carried out by the operator must incorporate the prescribed
safety devices.
This is your responsibility being the operator!